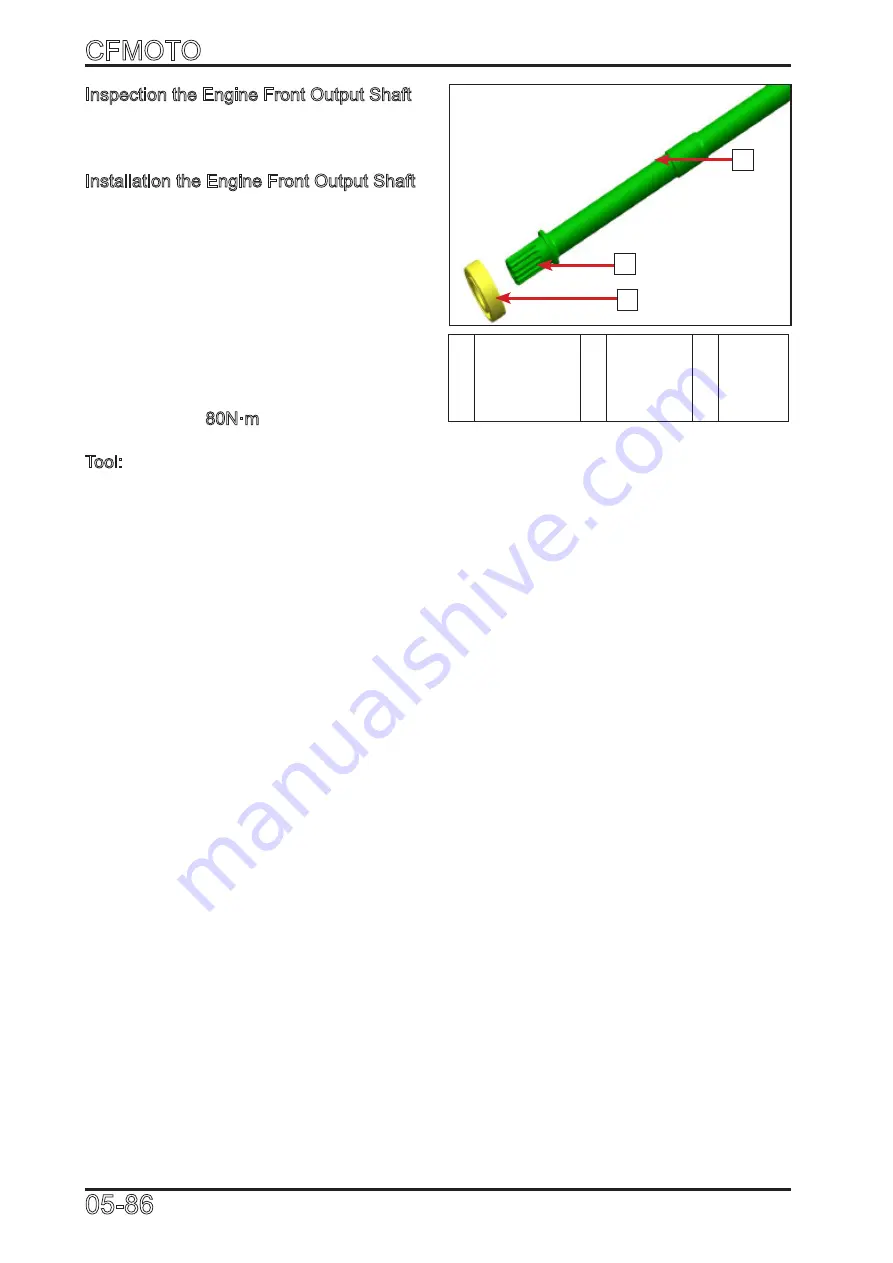
CFMOTO
05-86
058601
1 Front Output
Shaft
2
Cover 648
Cylinder
Locker
Position
3 Bearing
Inspection the Engine Front Output Shaft
Inspect the bearing to see if it can work
smoothly or have other wearing. Replace
the part if necessary.
Installation the Engine Front Output Shaft
Reverse the removal procedure for
installation.But pay attention to details
below:
When installing front output shaft, cover
the 648 cyl-inder locking glue on bearing
surface(See pic on right). Do not cover on
spline.
Cover 243 thread locker on bearing
retainer(Counterclockwise). Use special
tool to tight up in special torque.
Tighten torque 80N·m
Replace the oil-seal with grease on the lip.
Tool:
Bearing 6205 pressor
CF188-062301-921-001
Bearing retainer wrench
CF188-060008-922-001
Oil seal pressor
0800-060000-923-001
Front output shaft pressor
0800-062301-923-001
1
3
2
Summary of Contents for CF1000ATR 2018
Page 1: ...CFMOTO SERVICE MANUAL CF1000AU CF1000ATR CFORCE 1000 ...
Page 81: ...CFMOTO 05 6 5 1 4 EIN Location EIN Location Engine left side Engine right side 050601 050602 ...
Page 351: ...06 Vehicle chassis 06 41 6 7 3 Front and rear CV shaft disassemble view 064101 064102 ...
Page 363: ...Appendix A ...
Page 364: ...Appendix B ...
Page 365: ...Appendix C ...