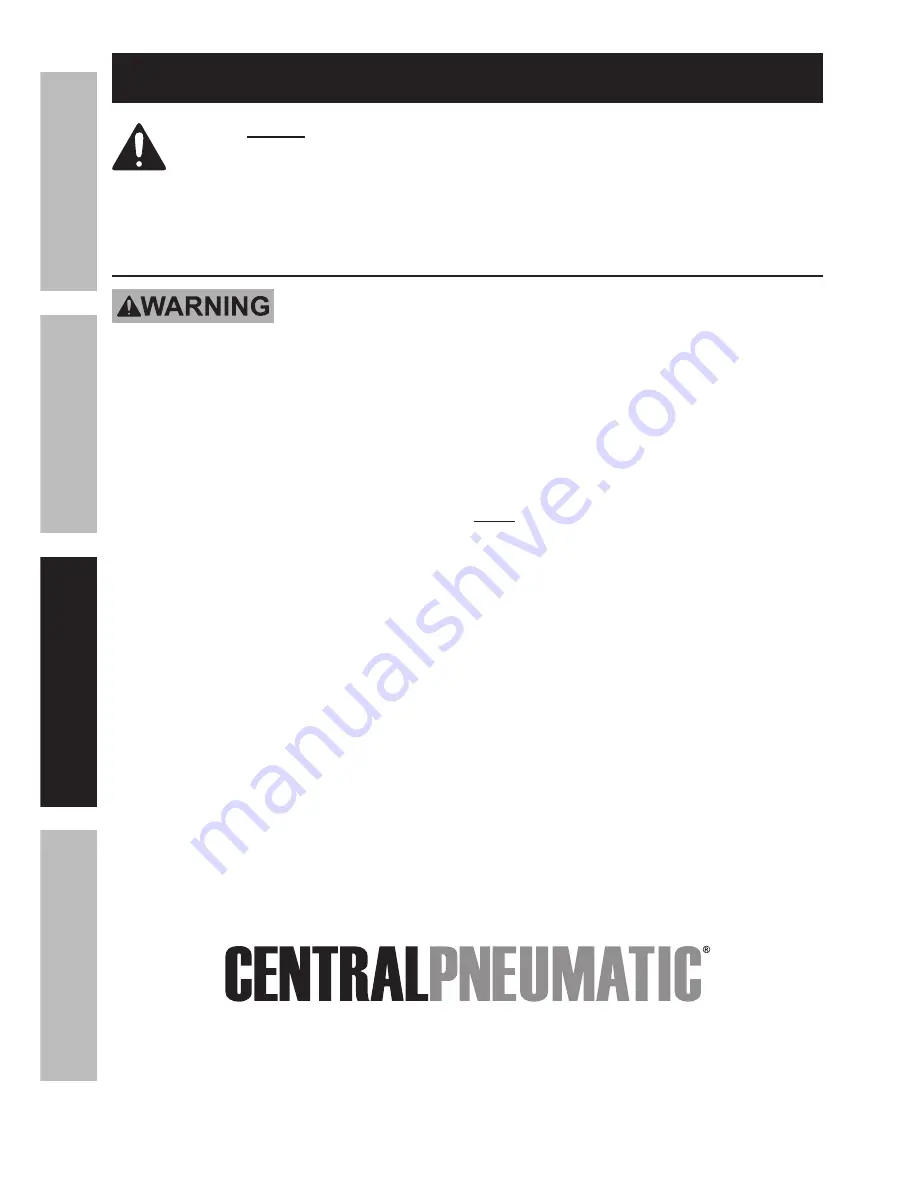
Page 12
For technical questions, please call 1-800-444-3353.
Item 68152
SAFET
y
Op
ERA
TION
M
AINTENAN
c
E
SETU
p
Operating Instructions
Read the ENTIRE IMpORTANT SAFETy INFORMATION section
at the beginning of this manual including all text under subheadings therein
before set up or use of this product.
Inspect tool before use, looking for damaged, loose, and missing parts.
If any problems are found, do not use tool until repaired.
Tool Set Up
TO pREVENT SERIOUS INJURy FROM AccIDENTAL OpERATION:
Turn off the tool, detach the air supply, safely discharge any residual
air pressure in the tool, and release the trigger before performing
any inspection, maintenance, or cleaning procedures.
TO pREVENT SERIOUS INJURy:
Do not adjust or tamper with any control or component in a way not specifically
explained within this manual. Improper adjustment can result in tool failure or
other serious hazards.Designate a work area that is clean and well-lit.
1. To install the Backing Pad, turn the Spindle
Lock so it engages with the Drive Spindle,
keeping it from freely turning while installing
the Backing Pad. See Figure C.
2. With the Drive Spindle locked in place,
thread the Backing Pad securely
into the Drive Spindle. Then turn the
Spindle Lock back, allowing the Drive
Spindle to freely turn. See Figure C.
Note:
Ensure that the Spindle Lock is fully
disengaged from the Drive Spindle prior to
use. If the tool is operated with the Spindle
Lock engaged with the Drive Spindle, the
Sander will spin rather than randomly orbit.
3. The Sander ONLY uses 6" diameter, PSA
(Pressure Sensitive Adhesive) sanding
discs (sold separately). Firmly attach
the sanding disc to the Backing Pad.
Summary of Contents for 68152
Page 1: ......