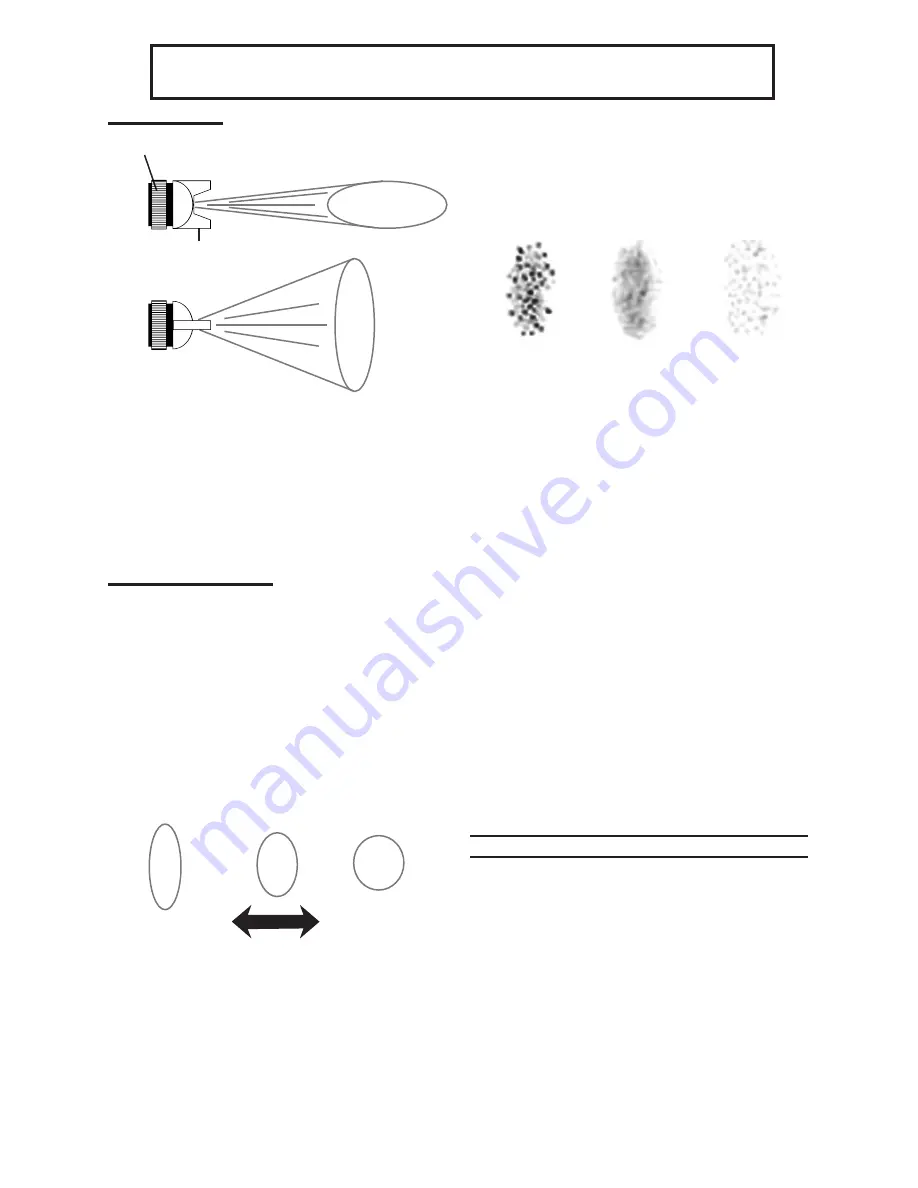
ImPOrtant: clean the spray gun ImmedIately after use.
Improper cleaning will cause the spray gun not to work.
SKU 66801
Page 11
For technical questions, please call 1-800-444-3353;
troubleshooting section near the end of manual.
Fan direction
Figure 4
Horizontal Fan
Vertical
Fan
Air Cap (1)
Lock Ring
1. To change the direction of the fan
from horizontal to vertical, loosen the
Lock Ring and turn the Air Cap (1) 90
degrees. After the adjustment, tighten
the Lock Ring by hand - See Figure
4.
Pattern adjustment
warnIng! never exceed the maxi-
mum operating pressure.
Adjust the air pressure during op
-
1.
eration with the Trigger (36) fully
depressed and the Air Control Knob
(19) fully open. If you need to reduce
the air pressure for specific areas,
use the Air Control Knob or adjust the
air compressor.
Figure 5
Flat/Open
Round/Closed
2.
To set the spray pattern size specific
to the job, use the Pattern Control
Knob (23). Turn the Pattern Control
Knob counterclockwise (all the way
open) to flatten the spray pattern.
Turn it clockwise for a round spray
pattern - See Figure 5.
Turn the Fluid Control Knob (12)
3.
clockwise until it is fully closed.
Figure 6
Too Fine
(Loosen)
Too Coarse
(Tighten)
Correct
4. After setting up a piece of scrap
material, squeeze the Trigger (36)
in short bursts while tuning the Fluid
Control Knob (12) counterclockwise
and observe the spray patterns until
you see the pattern you want. Also,
look at the pattern for consistency.
Too much air may cause the spray
to come out too fine. Reduce the air
pressure or allow more material to
come out by opening the Fluid Con-
trol Knob (12). If the spray appears
too thick (you see globs of paint),
close down the Fluid Control Knob
slowly, checking the mixture after
each adjustment. Use the counter nut
next to the Fluid Control Knob to lock
the setting in place.
work Piece and work area set up
Designate a work area that is clean
1.
and well-lit. The work area must not
allow access by children or pets to
prevent injury and distraction.
Route the air hose along a safe route
2.
to reach the work area without creat-
ing a tripping hazard or exposing the
air hose to possible damage. The air
hose must be long enough to reach