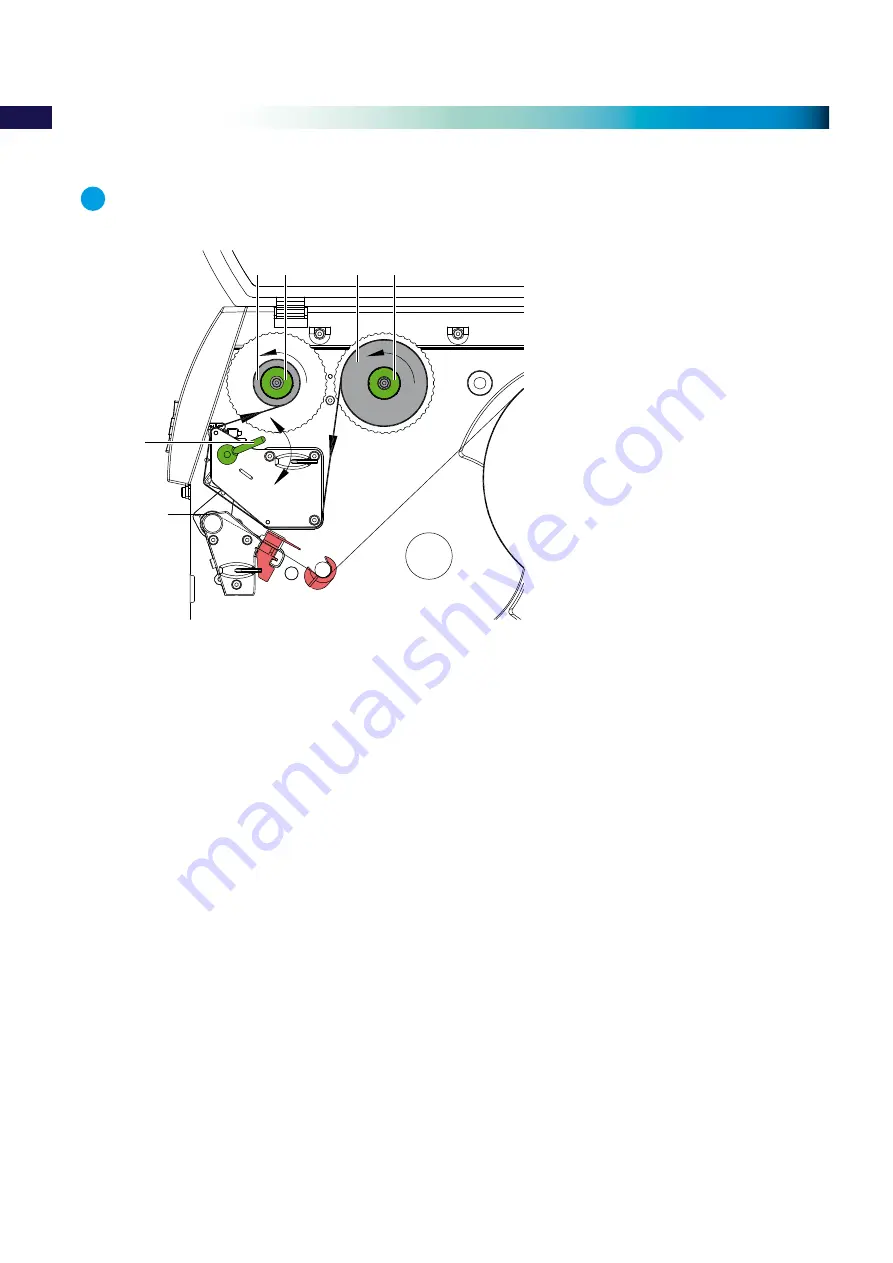
16
4.2
Loading ribbon
i
Notice!
The printer is supplied with a ribbon already installed, to replace it proceed as follow.
1
3
4
5
2
Fig. 15 Feed path of the ribbon
1. Clean printhead before loading the ribbon (
5.3 on page 18).
2. Turn lever (5) counterclockwise to lift the printhead.
3. Slide ribbon roll (3) onto the ribbon supply hub (4) until it stops and so that the colour coating of the ribbon faces
downward when being unwound.
4. Hold ribbon roll (3) firmly and turn knob on ribbon supply hub (4) counterclockwise until the ribbon roll is secured.
5. Slide suitable transfer ribbon core (1) onto the ribbon take-up hub (2) and secure it in the same way.
6. Guide ribbon through the print unit as shown in Fig. 15.
7. Secure starting end of transfer ribbon to the transfer ribbon core (1) with adhesive tape. Ensure counterclockwise
rotation direction of the transfer ribbon take-up hub.
8. Turn ribbon take-up hub (2) counterclockwise to smooth out feed path.
9. Turn lever (5) clockwise to lock the printhead.
4
Loading material