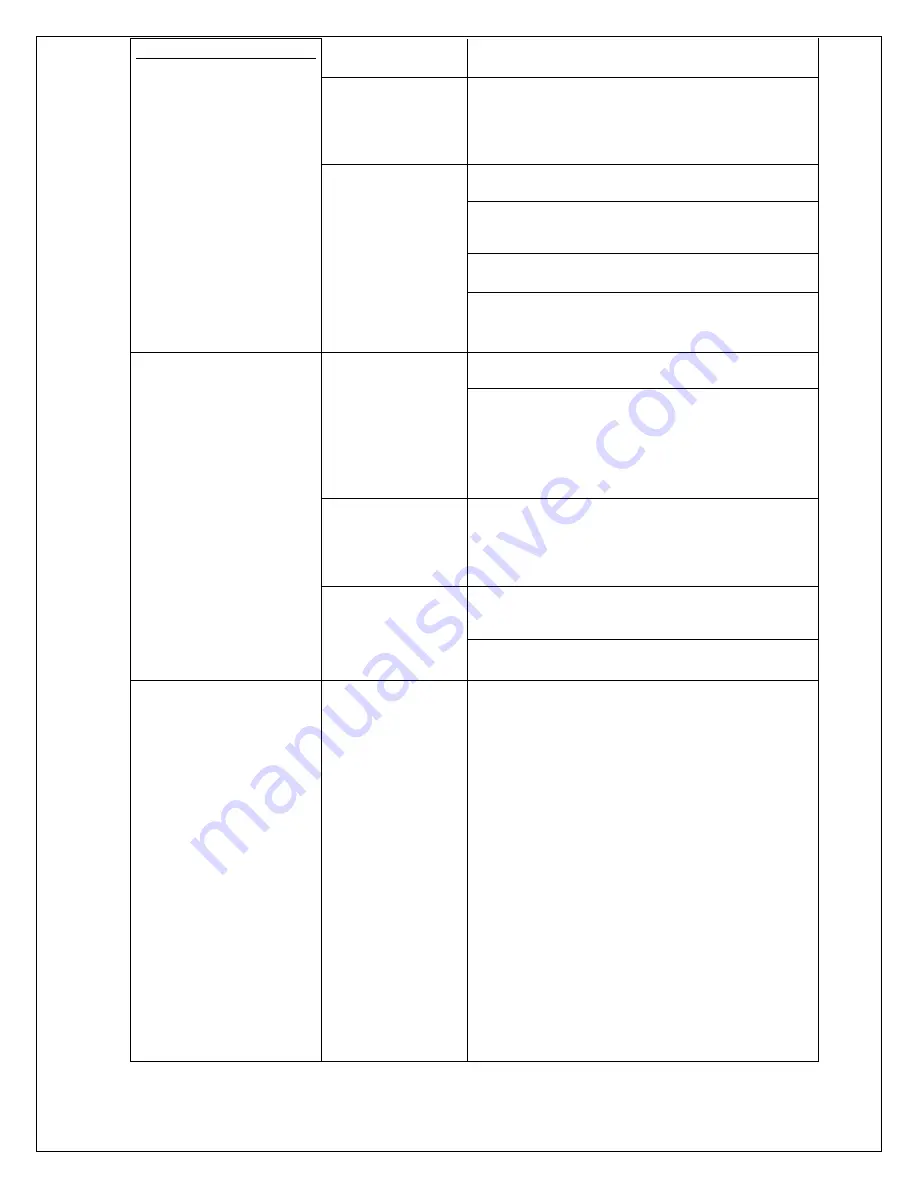
35
V3.15.22
Issues
(Cont.) No cooling: no
refrigerant flow.
If the "snowflake" icon is
illuminated on the
temperature display
control, the compressor
should be running.
Possible Causes
Potential Solutions
(Cont.) High
pressure safety
shutdown / high
discharge
pressure
Dirty or obstructed condenser coil: clean and
remove all obstructions to airflow.
Intermittent power
to compressor
Check for loose wires and secure.
Compressor cycling on internal thermal overload
protection. Replace start capacitor/relay
assembly
Compressor cycling on high pressure - see "High
pressure safety shutdown" section.
Faulty compressor. Consult factory.
No cooling: Evaporator
fan not blowing.
If the "fan" icon is
illuminated on the
temperature display
control, the fan should be
blowing air.
No power to fan(s)
Power supply to Evaporator interrupted. Restore
power.
Power supply to fan interrupted: loose wire.
Inspect for loose fan wiring and reconnect.
Fan capacitor: check for loose wires or out of
spec capacitance. Reconnect loose wires or
replace capacitor(s).
Fan obstructed
With power to unit disconnected, check the
rotation of the blower fan. If fan does not spin
freely, inspect for and remove obstructions. If no
obstructions are found, the fan may need to be
replaced. Consult factory.
Fan running but
not drawing air
through coil.
Fan short cycling: Make sure all housing panels
are attached to the unit. Replace missing panels.
Coil is blocked with ice. Refer to the "Iced coil"
section.
Iced coil
Temperature
displayed is higher
than actual cellar
temperature
If using a bottle probe, check placement and
compare to actually cellar temp. Relocate probe
if necessary to better correlate to actual cellar
temperature.
Probe fault: check for loose connections if
splices were added in the field.
Moisture in bottle probe jack: Can cause high
readings, consult factory for solution.