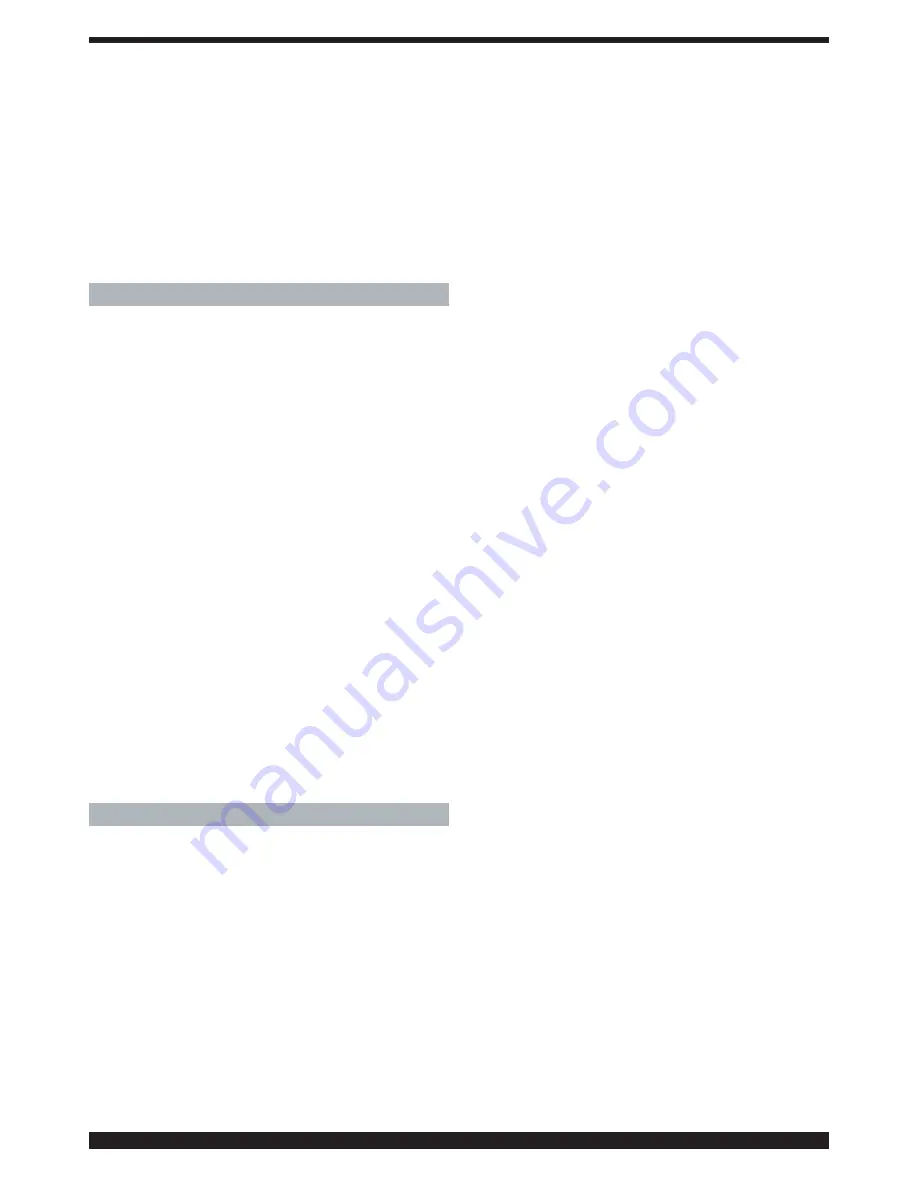
15
rent, and when it ends LED A lights. All knobs are dis-
abled.
To see the setting of the service function related to the
saved program, press the key R and hold it down; after 2
sec. the display G shows the first message dSP. Pressing
the torch trigger will display the abbreviations of the vari-
ous functions in sequence, and display Q shows the set-
ting.
To return to welding with a saved program, release the
key R.
To exit saved programs, press the key R and, while hold-
ing it down, briefly press and release the key O.
7 M
MAINTENANCE
• Safety ggas nnozzle
This nozzle must be periodically cleaned to remove splat-
tered metal. Replace if distorted or squashed.
• Contact ttip.
Only a good contact between this contact tip and the wire
can ensure a stable arc and optimum current output; you
must therefore observe the following precautions:
A) The contact tip hole must be kept free of grime and
oxidation.
B) Splattered metal sticks more easily after long welding
sessions, blocking the wire flow.
The tip must therefore be cleaned more often, and
replaced if necessary.
C) The contact tip must always be firmly screwed onto
the torch body. The thermal cycles to which the torch is
subjected can cause it to loosen, thus heating the torch
body and tip and causing the wire to advance unevenly.
• Wire lliner.
This is an important part that must be checked often,
because the wire may deposit copper dust or tiny shav-
ings. Clean it periodically along with the gas lines, using
dry compressed air.
The liners are subjected to constant wear and tear, and
therefore must be replaced after a certain amount of time.
• Gearmotor ggroup.
Periodically clean the set of feeder rollers, to remove any
rust or metal residue left by the coils. You must periodi-
cally check the entire wire feeder group: hasp, wire
guide rollers, liner and contact tip.
8 A
ACCESSORIES
Art. 1434 Wire feeder.
Art. 1242 Torch 3.5mt
Art. 129
Kit for coil diameter 300 Kg 15
Art. 2003 Pull 2003 torch with UP/DOWN command
on grip.