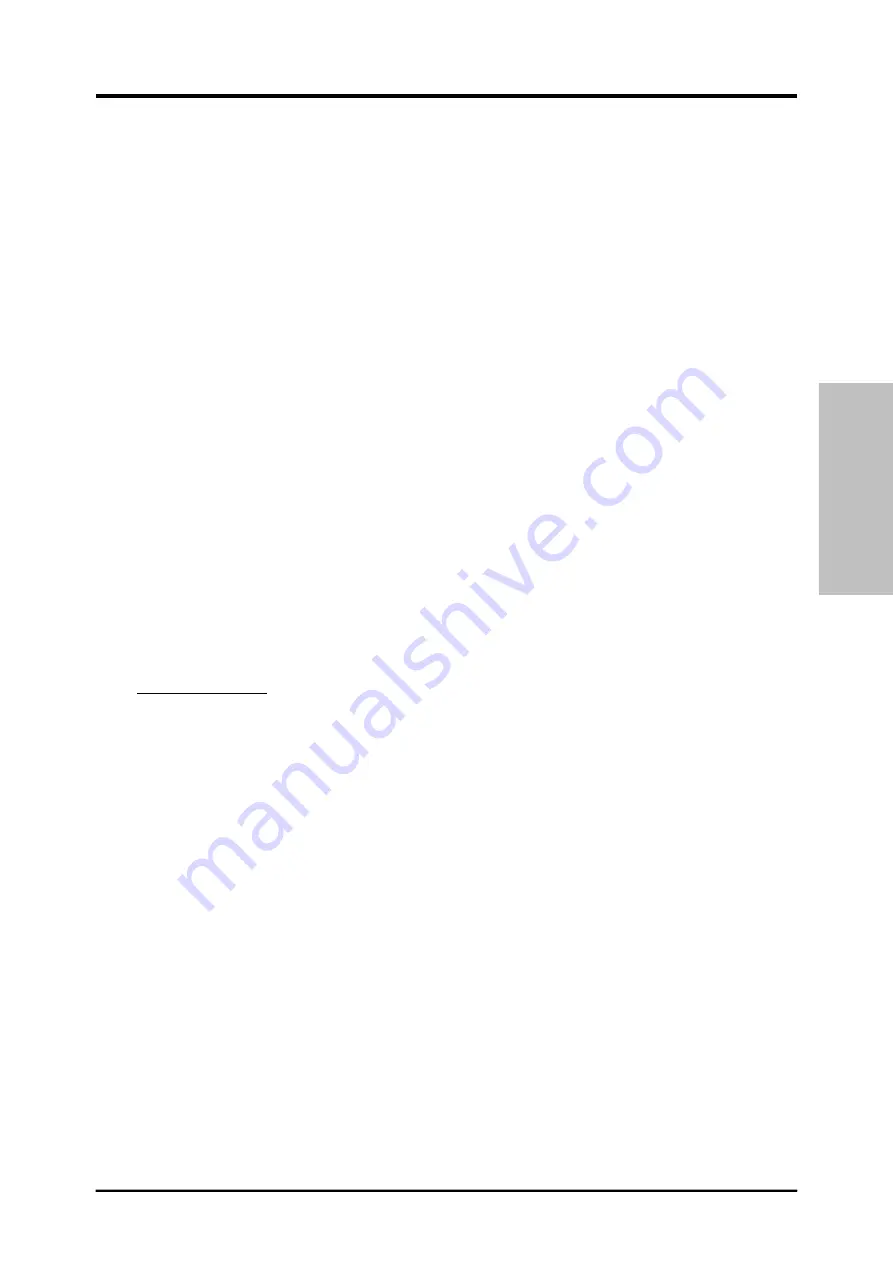
CEBORA S.p.A.
15
3.300.160-F
10-03-2016
GB
BW - Cap.
Cooling liquid tank cap.
BT - Quick-fitting valves.
Connect the hoses of the Power Source - Wire Feeder extension (2) marked with the adhesive red and
blue bands. Match the hose and valve colours correctly.
5.3
Protections description.
5.3.1
Coolant pressure.
This protection is achieved by means of a pressure switch, inserted in the fluid delivery circuit, which
controls a microswitch.
Low pressure is indicated by the abbreviation
H2O
flashing on the display
O
of the Control Panel.
5.3.2
Fuse (T 1.6A/400V - Ø 6.3x32) mm.
This fuse is inserted to protect the pump, and is located on the rear panel of the Power Source.
5.4
Managing the cooling unit (see Control Panel Instruction Manual).
On the Control Panel, press the button
AO
and, while holding it down, press the button
E
to enter a
submenu.
Use the knob
N
to make your choice:
H2O.
Turn the knob
Q
to select the type of operation:
OFF
= off;
OnC
= always on;
OnA
= automatic start-up.
Press once again the keys
AO
and
E
to exit the submenu, storing automatically the actual setup.
At Power Source start-up, the unit starts running to place the liquid in the cooling circuit under pressure.
If the start command (ARC-ON signal) does not arrive within 15 seconds, the unit stops.
At each start command (ARC-ON signal) the unit begins operating and stops 3 minutes after the start
signal disappears.
If the coolant pressure is too low, the Power Source delivers no current and on the display
O
the message
H2O
will appear, flashing, on the display.
6
MAINTENANCE.
6.1
Periodic inspection, cleaning.
Periodically make sure that the Welding System equipment and all connections are in proper condition to
ensure operator safety.
Periodically open the panels of the Power Source to check the internal parts. Periodically remove dirt or
dust from the internal parts, using a jet of low-pressure dry compressed air or a brush.
Check the condition of the internal power connections and connectors on the electronic boards; if you
find “loose” connections, tighten or replace the connectors.
To ensure proper air flow and thus adequate cooling of the internal parts of the Power Source,
periodically open the grids on the Power Source and check the interior of the aeration tunnel.
Periodically remove dirt or dust from the internal parts of the tunnel, using a jet of low-pressure dry
compressed air or a brush.
Check the condition of the electrical connectors, the power cable and the pneumatic fittings; replace if
damaged.
After making a repair, be careful to arrange the wiring in such a way that the parts connected to the power
supply are safely insulated from the parts connected to the welding circuit.
Do not allow wires to come into contact with moving parts or those that heat up during operation.
Mount the clamps as on the original machine to prevent, if a conductor accidentally breaks or becomes
disconnected, a connection from occurring between power supply and the welding circuits.
Summary of Contents for MIG 5040/T
Page 35: ...CEBORA S p A 35 3 300 160 F 10 03 2016 Art 287 80 ...
Page 37: ...CEBORA S p A 37 3 300 160 F 10 03 2016 Art 289 80 ...
Page 39: ...CEBORA S p A 39 3 300 160 F 10 03 2016 ...
Page 40: ...CEBORA S p A 40 3 300 160 F 10 03 2016 GR 52 ...
Page 42: ...CEBORA S p A 42 3 300 160 F 10 03 2016 ...