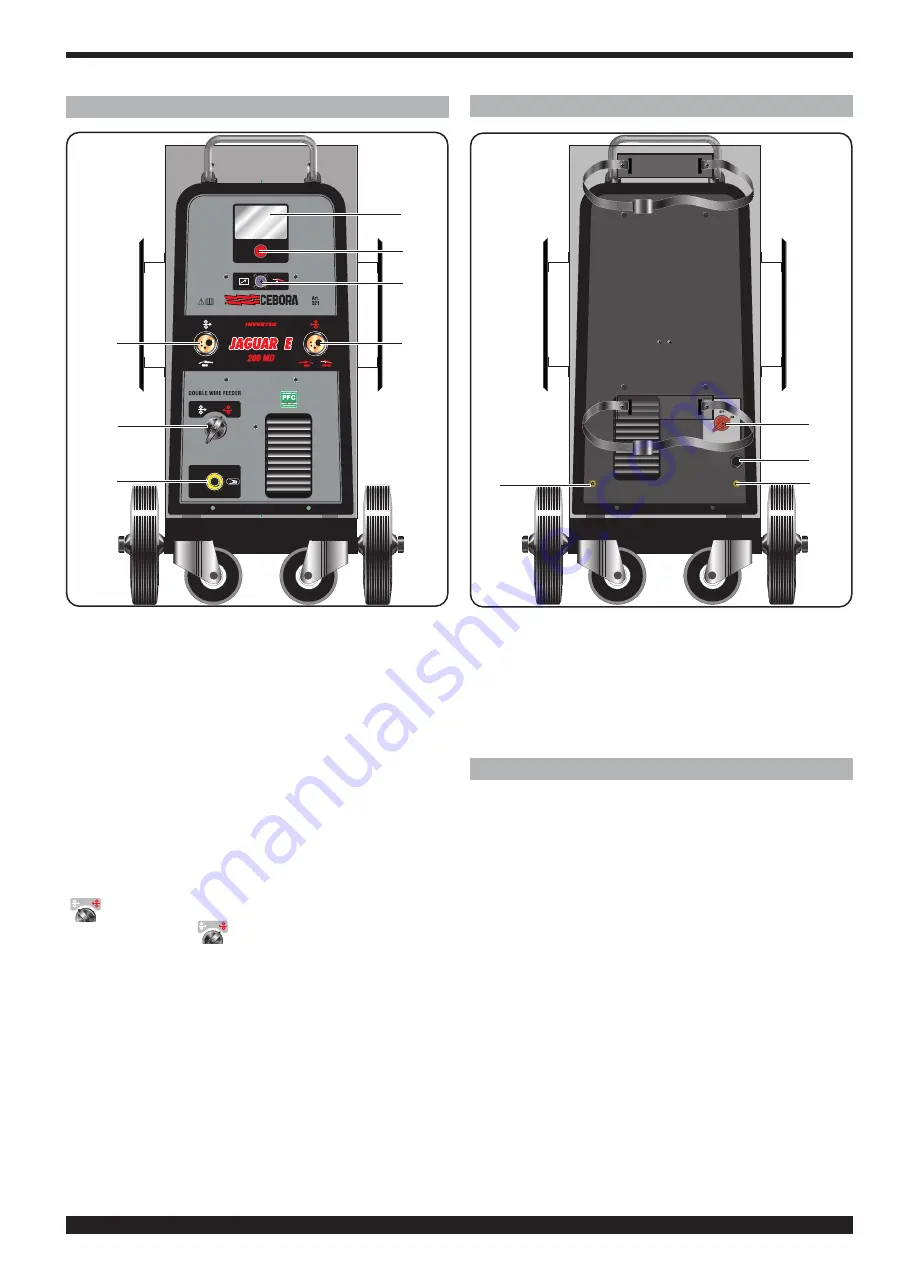
12
3 CONTROLS LOCATED ON FRONT PANEL.
C
D
B
C1
F
E
A
A – DISPLAY SCREEN.
This displays both the welding parameters and all the
welding functions.
C
–
CENTRAL ADAPTER
: Connect the welding torch
.
C1 – CENTRAL ADAPTER
.
This is where the welding torch or the Push-Pull system
torch Art. 2003/2009 is to be connected.
D – SOCKET (-):
this is where the earth cable is to be
connected.
E - SELECTOR SWITCH
:
Central adapter
C
is operated by selecting position (
) with the selector switch knob, on the contrary, by
selecting position (
) central adapter
C1
is operated.
F
–
CONNECTOR
: For connecting remote controls and
the welding control cable
Push–Pull Art.
4 CONTROLS LOCATED ON REAR PANEL.
I
H
G
I
G – MAIN CABLE
H – SWITCH.
Starts and stops the machine
G – GAS PIPE CONNECTION.
5 INSTALLATION AND START-UP
Position the welding machine so as to allow the free cir-
culation of air inside and, as much as possible, prevent
metal or other dusts from penetrating. Position the weld-
ing machine in an area that ensures good stability.The
weight of the welding machine is approximately 68 Kg.
Only skilled personnel should install the machine.All con-
nections must be carried out in compliance with current
standards (IEC/CEI EN 60974-9) and in full observance
of current safety laws.Make sure that the supply voltage
corresponds to the rated voltage of the welding machine.
Size the protective fuses based on the data listed on the
technical specifications plate. Mount the plug on the pow
-
er cord, being especially carefully to connect the yellow/
green conductor to the earth pole. This welding machine
has been designed to contemporarily mount 2 welding
torches and 2 coils of wire having a diameter of
MAX
300mm.
This machine cannot weld with the 2 torches at the
same time
, the torch selection is made by means of se-
lector switch
E
.
The rear shelf can hold 2 cylinders having diameter
MAX