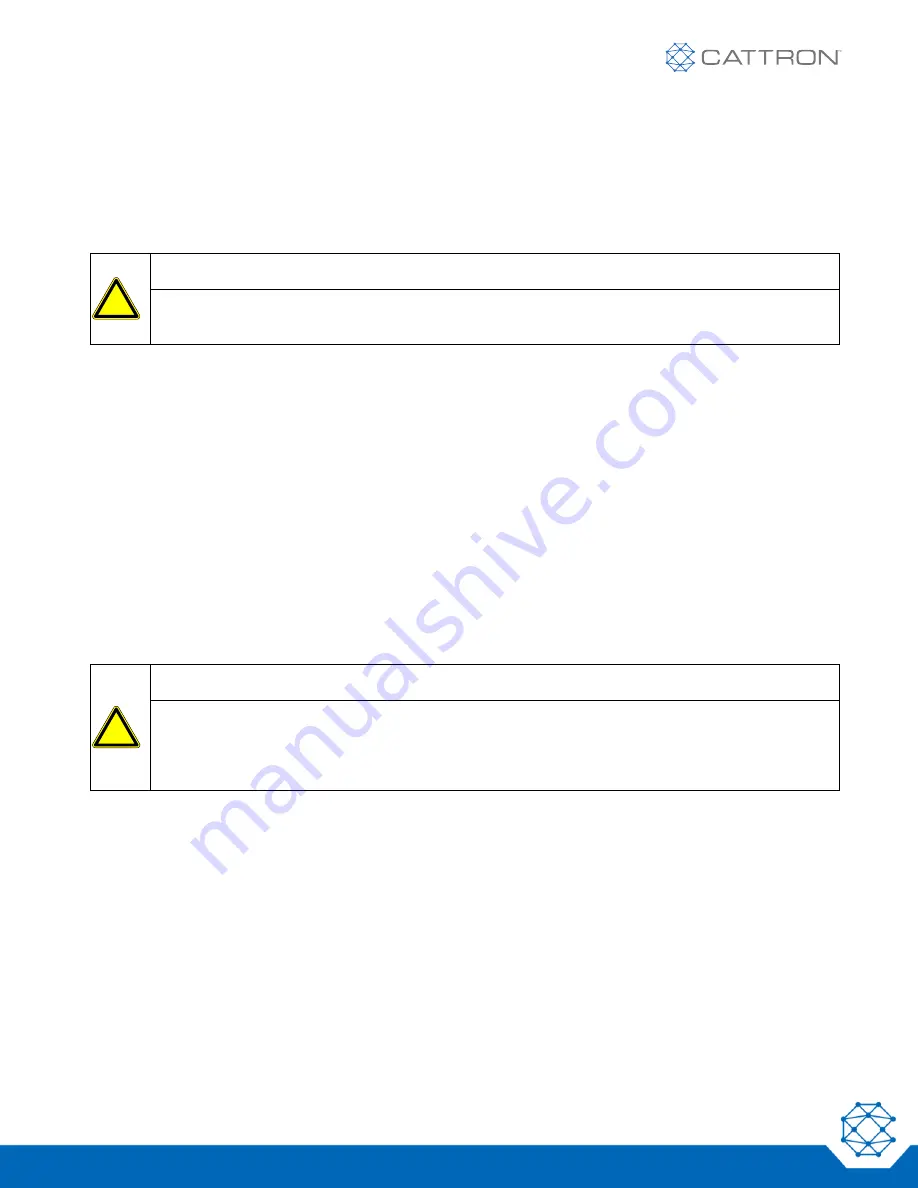
CANplus CP1000
Control Panel Operation Manual
*Patent Pending
44
9M02-1000-A401-EN Revision G
equipment, improper wire sizes, faulty wiring, or nearby lightning strikes.
11.3.5 Suppression of Voltage Transients (Spikes)
CAUTION
THE INSTALLATION OF VOLTAGE TRANSIENT SUPPRESSION AT THE TRANSIENT SOURCE IS
REQUIRED. CATTRON FOLLOWS SAE RECOMMENDED ELECTRICAL ENVIRONMENT
PRACTICES.
Inductive devices such as relays, solenoids and motors generate voltage transients and noise in electrical
circuits. Unsuppressed voltage transients can exceed SAE specifications and damage electronic controls.
Relays and solenoids with built-in voltage transient suppression diodes are recommended whenever possible.
Ensure the proper installation of diodes when built-in voltage transient suppression is not available.
Locate inductive devices as far as possible from the components of the electronic control system. When using
electric motors, it may also be necessary to add isolation relays to eliminate voltage transients, noise and
prevent back feed.
11.3.6 Welding on Equipment with Electronic Controls
Proper welding procedures should be observed to avoid damage to electronic controls, sensors, and associated
components. The component should be removed for welding when possible.
The following procedure must be followed if the component must be welded while installed on equipment with
electronic controls. This procedure will minimize the risk of component damage.
CAUTION
DO NOT GROUND THE WELDER TO ELECTRICAL COMPONENTS SUCH AS THE CONTROL
GROUND OR SENSORS. IMPROPER GROUNDING CAN CAUSE DAMAGE TO ELECTRICAL
COMPONENTS. CLAMP THE GROUND CABLE FROM THE WELDER TO THE COMPONENT
BEING WELDED. PLACE THE CLAMP AS CLOSE AS POSSIBLE TO THE WELD TO REDUCE THE
POSSIBILITY OF DAMAGE.
1.
Stop the engine. Turn the key switch to the OFF position.
2.
Disconnect the negative battery cable from the battery.
3.
Open any installed battery disconnect switch.
4.
Unplug the control system if possible.
5.
Connect the welding ground cable as close as possible to the area to be welded.
6.
Protect the wiring harness from welding debris and spatter.
7.
Use standard welding methods to weld the materials.
!
!