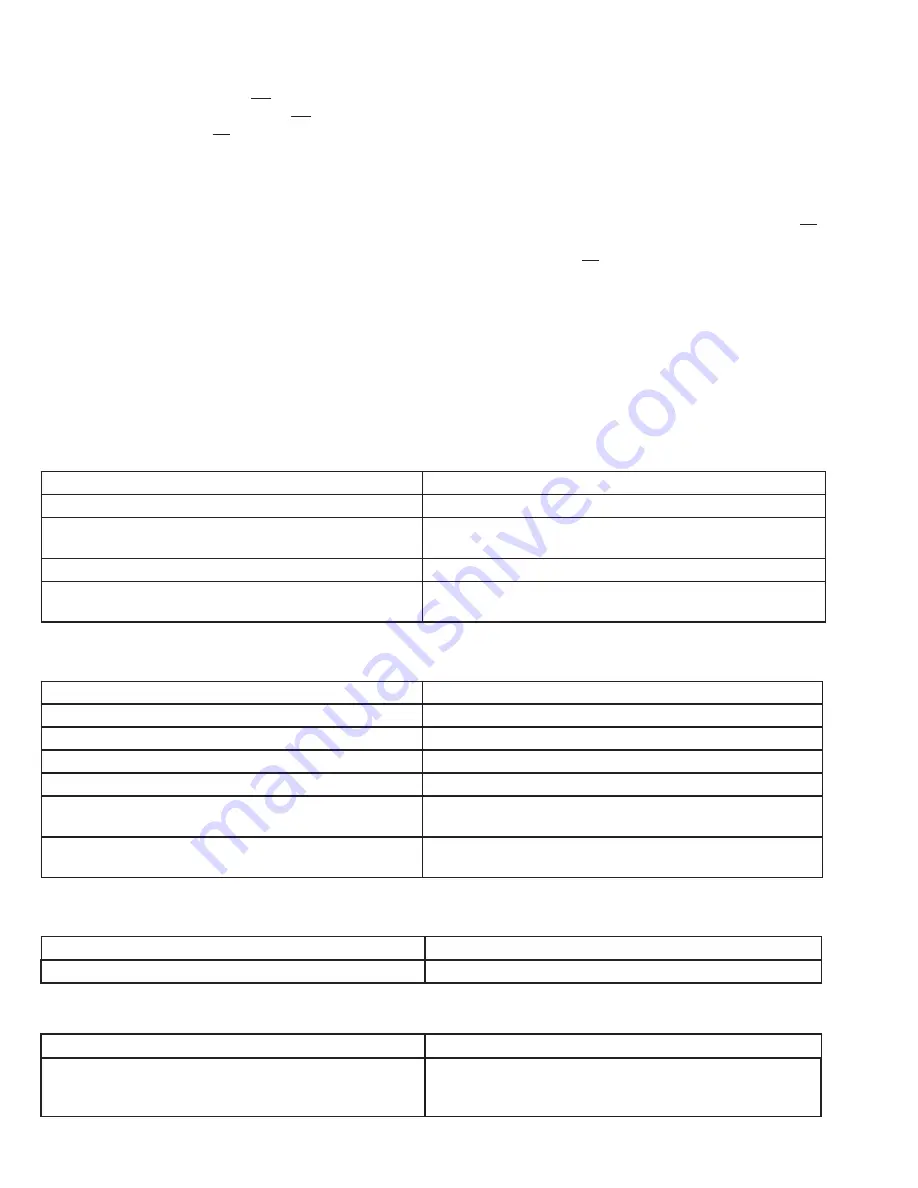
IOM-POSR-2
14
7. Slowly pressurize the inlet of the main valve
(MV) and pilot valve (PV) to 100 psig (6.9 Barg).
NOTE:
If the pilot valve (PV) has any other
range spring (15) above 5–15 psig (.34–1.03
Barg), the test pressure can be raised to 200
psig (13.8 Barg)
.
8. Using a solution of leak detection fluid and
water, apply a liberal amount of the solution to
cover each external joint, including the thread ed
fittings (20), tub ing (21) and the interconnecting
pipe nipple (19) threaded con nec tions. Wait
a minimum of five min utes to allow sufficient
time for a leak to form bub bles. Repeat this
procedure with a second five minute wait.
SECTION VIII
9. Identify and mark any observed leakage.
Dis as sem ble down to the point of leakage
and determine the cause of the leak. Repair
and reassemble per instructions in Section
VI. Retest per Section VII.
10. Shut off pressure to inlet connection of
main valve (MV) and remove all leak testing
equip ment. Reset the adjusting screw (19)
back to its normal setpoint by rotating the
screw (19) CCW (viewed from above) the
same num ber of revolutions recorded in Ar ti cle
6. pre vi ous, this subsection.
VIII. TROUBLE SHOOTING GUIDE
1. Erratic or Noisy Operation.
Possible Cause
Remedy
a.
Wet steam or condensate at the inlet.
a.
Install a steam trap on the inlet side of the regulator.
b.
Clogged pilot valve screen.
b.
Clean or replace. Blowdown inlet drip leg. Install up-
stream strainer, if severe.
c.
Regulator oversized for flow conditions.
c.
Install correct size.
d.
Insufficiently sloped line.
d.
Move tap from top of pipe to side; or, increase sensing
tube to 3/8" OD.
2. Regulator won't maintain downstream set pressure.
Possible Cause
Remedy
a.
Valve undersized.
a.
Resize based on actual service conditions.
b.
Incorrect range spring.
b.
Replace range spring.
c.
Failed bellows.
c.
Replace bellows assembly.
d.
Failed piston seal ring.
d.
Replace seal ring.
e.
Pressure drop less than required 15 or 20 psid
(1–1.4 Bard).
e.
Contact your Cashco Representative.
f.
Insufficiently sloped line.
f.
Move tap from top of pipe to side; or, increase sensing
tube to 3/8" OD.
Possible Cause
Remedy
a.
Defective diaphragm.
a.
Replace diaphragm.
3. Leakage through the pilot spring chamber vent hole.
4. Excessive pressure downstream.
Possible Cause
Remedy
a.
Main valve or pilot plug not closing.
a.
Inspect the seating of the main valve and then the
pilot plug seating. Clean or replace. Check seat
gaskets; replace.