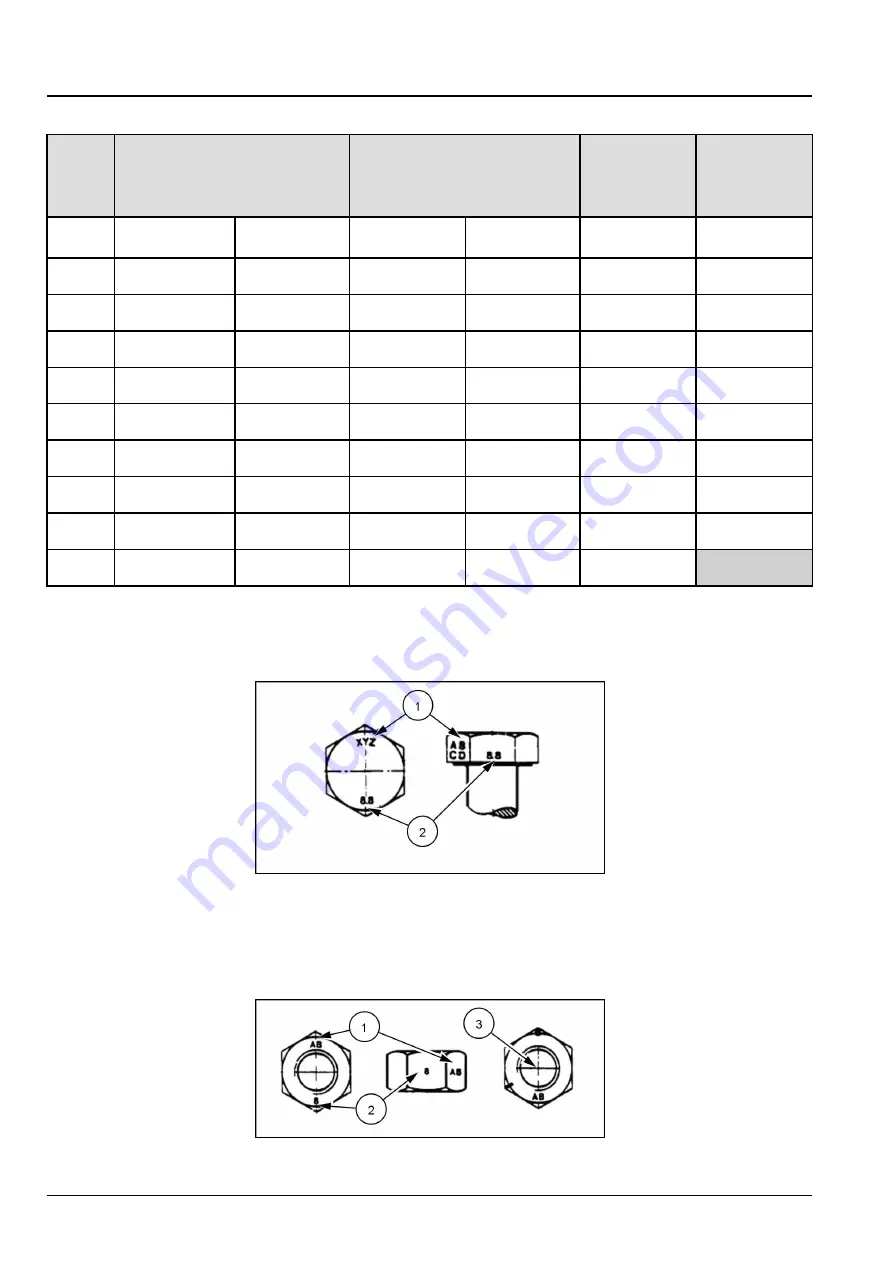
INTRODUCTION
METRIC FLANGED HARDWARE
NOM.
SIZE
CLASS 8.8 BOLT and
CLASS 8 NUT
CLASS 10.9 BOLT and
CLASS 10 NUT
LOCKNUT
CL.8
W/CL8.8
BOLT
LOCKNUT
CL.10
W/CL10.9
BOLT
UNPLATED
PLATED
W/ZnCr
UNPLATED
PLATED
W/ZnCr
M4
2.4 N·m
(
21 lb
in
)
3.2 N·m
(
28 lb
in
)
3.5 N·m
(
31 lb
in
)
4.6 N·m
(
41 lb
in
)
2.2 N·m
(
19 lb
in
)
3.1 N·m
(
27 lb
in
)
M5
4.9 N·m
(
43 lb
in
)
6.5 N·m
(
58 lb
in
)
7.0 N·m
(
62 lb
in
)
9.4 N·m
(
83 lb
in
)
4.4 N·m
(
39 lb
in
)
6.4 N·m
(
57 lb
in
)
M6
8.3 N·m
(
73 lb
in
)
11 N·m
(
96 lb
in
)
12 N·m
(
105 lb
in
)
16 N·m
(
141 lb
in
)
7.5 N·m
(
66 lb
in
)
11 N·m
(
96 lb
in
)
M8
20 N·m
(
179 lb
in
)
27 N·m
(
240 lb
in
)
29 N·m
(
257 lb
in
)
39 N·m
(
343 lb
in
)
18 N·m
(
163 lb
in
)
27 N·m
(
240 lb
in
)
M10
40 N·m
(
30 lb ft
)
54 N·m
(
40 lb
ft
)
57 N·m
(
42 lb ft
)
77 N·m
(
56 lb
ft
)
37 N·m
(
27 lb ft
)
53 N·m
(
39 lb ft
)
M12
70 N·m
(
52 lb ft
)
93 N·m
(
69 lb
ft
)
100 N·m
(
74 lb
ft
)
134 N·m
(
98 lb
ft
)
63 N·m
(
47 lb ft
)
91 N·m
(
67 lb ft
)
M16
174 N·m
(
128 lb
ft
)
231 N·m
(
171 lb
ft
)
248 N·m
(
183 lb
ft
)
331 N·m
(
244 lb
ft
)
158 N·m
(
116 lb
ft
)
226 N·m
(
167 lb
ft
)
M20
350 N·m
(
259 lb
ft
)
467 N·m
(
345 lb
ft
)
484 N·m
(
357 lb
ft
)
645 N·m
(
476 lb
ft
)
318 N·m
(
235 lb
ft
)
440 N·m
(
325 lb
ft
)
M24
607 N·m
(
447 lb
ft
)
809 N·m
(
597 lb
ft
)
838 N·m
(
618 lb
ft
)
1118 N·m
(
824 lb ft
)
552 N·m
(
407 lb
ft
)
IDENTIFICATION
Metric Hex head and carriage bolts, classes 5.6 and up
20083680
1
1. Manufacturer's Identification
2. Property Class
Metric Hex nuts and locknuts, classes 05 and up
20083681
2
48190544 26/09/2017
18
Summary of Contents for 770 EX
Page 5: ...INTRODUCTION 48190544 26 09 2017 1 Find manuals at https best manuals com ...
Page 31: ...SERVICE MANUAL Engine 770EX Magnum 770EX 48190544 26 09 2017 10 ...
Page 33: ...Engine 10 Engine and crankcase 001 770EX Magnum 770EX 48190544 26 09 2017 10 1 10 001 1 ...
Page 51: ...This as a preview PDF file from best manuals com Download full PDF manual at best manuals com ...