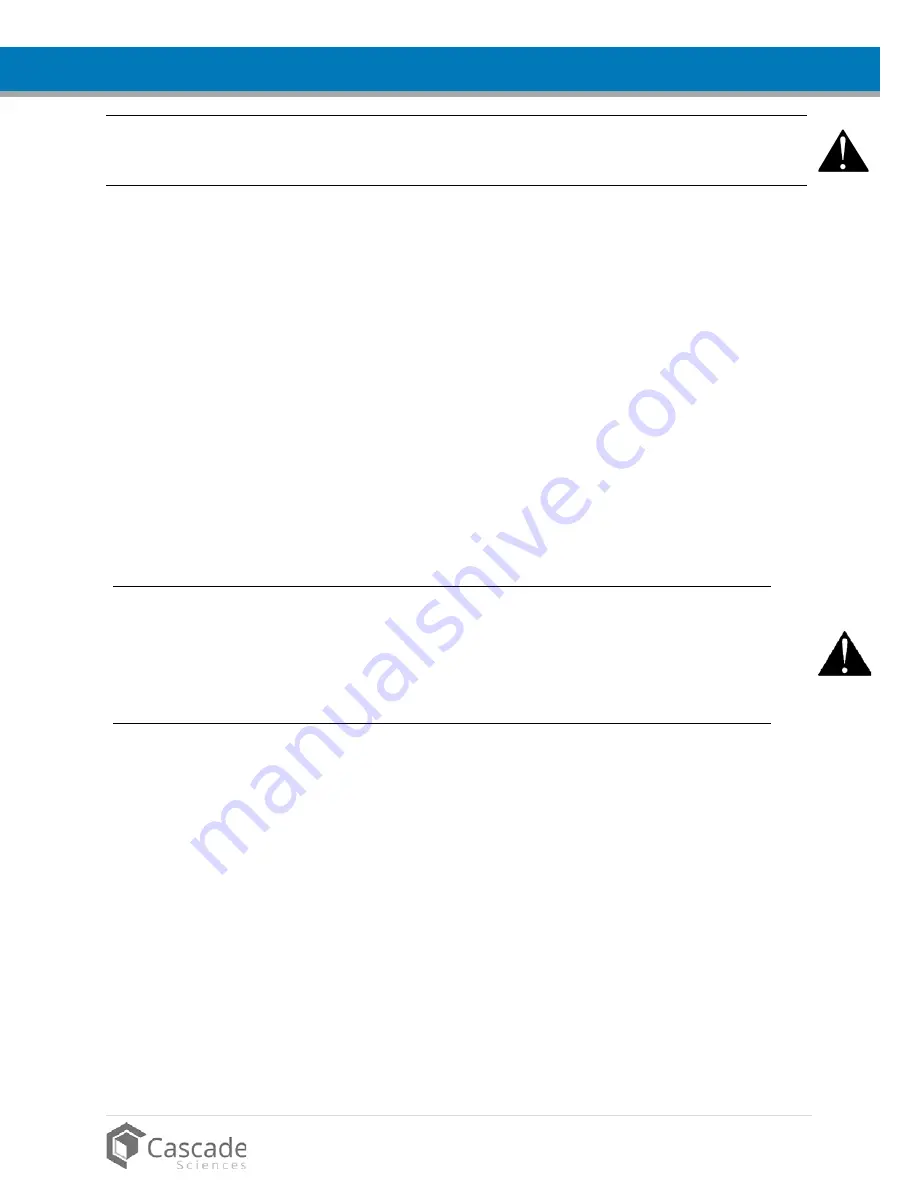
47
|
P a g e
cascadesciences.com
|
Tel. 503 847-9047
USER MAINTENANCE
Warning
: Disconnect the unit from its power supply prior to maintenance or cleaning of this unit.
Avertissement
: Avant d'effectuer toute maintenance ou entretien de cet appareil, débrancher le cordon
secteur de la source d'alimentation.
C
LEANING AND
D
ISINFECTING
If a
hazardous material or substance
has spilled in the unit, immediately initiate your site Hazardous
Material Spill Containment protocol. Contact your local Site Safety Officer and follow instructions per
the site policy and procedures.
•
The oven chamber should be cleaned prior to first use.
•
Periodic cleaning is required.
•
Do not use spray-on cleaners or disinfectants. These can leak through openings and coat
electrical components.
•
Do not use cleaners or disinfectants that contain solvents capable of harming paint coatings,
glass, or stainless steel surfaces.
Do not use chlorine-based bleaches or abrasives—these
will damage the chamber liner.
•
Consult with the manufacturer or their agent if you have any doubts about the compatibility
of decontamination or cleaning agents with the parts of the equipment or with material
contained in it.
Warning
: Exercise caution if cleaning the unit with alcohol or flammable cleaners. Always allow the
unit to cool down to room temperature prior to cleaning and make sure all cleaning agents have
evaporated or otherwise been completely removed prior to putting the unit back into service.
Avertissement:
Soyez prudent lorsque vous nettoyez l'appareil avec de l'alcool ou des produits de
nettoyage inflammables. Laissez toujours refroidir l'appareil à la température ambiante avant le
nettoyage et assurez-vous que tous les produits de nettoyage se sont évaporés ou ont été
complètement enlevés avant de remettre l'appareil en service.
Cleaning
1.
Remove all removable chamber accessory items (shelves, racks, and any additional items), if
present.
2.
Clean the chamber interior with a mild soap and water solution, including all corners.
3.
Take special care when cleaning around the temperature sensor probes. Do not clean the
probes.
4.
Clean all removable accessories and components.
5.
Rinse the chamber surfaces and shelving with distilled water and wipe dry with a soft cloth.
Do not use deionized water.
•
Deionized water is an aggressive solvent that will attack most metals. Never use
deionized water to clean your oven, even if it is readily available in your laboratory or
production workspace.
Summary of Contents for CVAC-9.3
Page 1: ...Installation Operation Manual CVAC 9 3 Vacuum Oven ...
Page 5: ...5 P a g e cascadesciences com Tel 503 847 9047 REPLACEMENT PARTS 53 ...
Page 6: ...6 P a g e cascadesciences com Tel 503 847 9047 TABLE OF CONTENTS ...
Page 8: ...8 P a g e cascadesciences com Tel 503 847 9047 CERTIFICATIONS ...
Page 12: ...12 P a g e cascadesciences com Tel 503 847 9047 INTRODUCTION ...
Page 28: ...28 P a g e cascadesciences com Tel 503 847 9047 INSTALLATION ...
Page 30: ...30 P a g e cascadesciences com Tel 503 847 9047 GRAPHIC SYMBOLS ...
Page 34: ...34 P a g e cascadesciences com Tel 503 847 9047 CONTROL OVERVIEW ...
Page 46: ...46 P a g e cascadesciences com Tel 503 847 9047 OPERATION ...
Page 54: ......