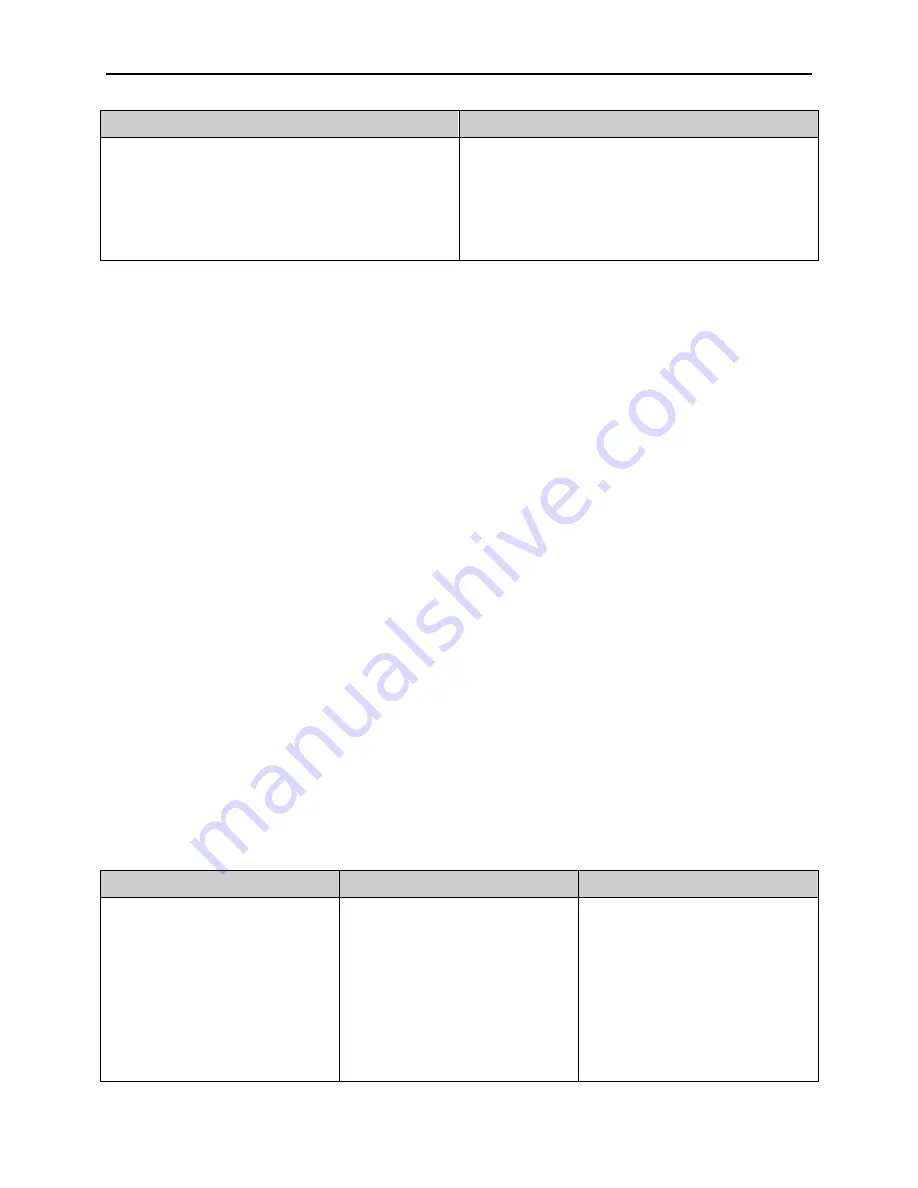
RS Series – Multi-Stage, Ring Section Pumps
January 2001
19
Table 10. Recommended Torque Values
Fastener Size
Torque (foot pounds)
1/4-20 UNC
5
5/16-18 UNC
10
3/8-16 UNC
15
1/2-13 UNC
30
7/8-14 UNF
315
1-12 UNF
446
D. Disassembly and Assembly
Preparations
NOTE
Refer to Section V, paragraph H for oil
lubrication and water cooling
disassembly and assembly procedures.
During disassembly, match mark parts so they
can be replaced in their original position. All
parts should be thoroughly cleaned or replaced
with new, if necessary. Sealing faces should be
perfectly clean. Carver Pump Company
recommends that all o-rings and shims are only
used once.
NOTE
To avoid damage to o-rings, check to
make sure all parts are free of sharp
edges or burrs.
Close suction and/or discharge valves. The
pump cases should be cooled down to ambient
temperature. Cases must be empty and not
under pressure.
After prolonged operation, components may not
be easily removed from shaft. In such instances,
rust solvent may be used and suitable extracting
tools applied wherever possible. Do NOT use
force under any circumstances. Refer to Table
11, Recommended Tools, for proper tooling
during disassembly and assembly.
Refer to appropriate sectional drawing, for
location of parts followed by an item number.
Assemble the pump in accordance with
accepted rules of engineering practice. Coat
individual components with a suitable lubricant
before assembling. Assembly of unit should be
performed on a flat surface.
While assembling the pumping unit, Carver
Pump Company recommends that the following
parts be replaced with new:
•
O-rings
•
Shims
•
Bearings
•
Grease seals
•
Mechanical seals
If new impellers or new shaft protecting sleeves
are fitted, impellers must be axially aligned with
respect to diffusers. Refer to paragraph F of this
section for procedures regarding axial impeller
alignment.
Table 11. Recommended Tools
Tools
Materials
Testing Equipment
Spanner wrench
Grease (Rykon) or oil
Coupling alignment gauges
Rawhide or wood mallet
Wooden wedge
Allen wrench set
Socket, open, & box wrench set
Vice grips
“C” clamp
Summary of Contents for RS A
Page 1: ...I 280...
Page 2: ......
Page 4: ...NOTES ON INSPECTION AND REPAIRS INSPECTION DATE REPAIR TIME REPAIRS COST REMARKS...
Page 32: ...26 BLANK...
Page 38: ...32 BLANK...
Page 40: ...34 BLANK...
Page 44: ...RS Series Multi Stage Ring Section Pumps January 2001 38 THIS PAGE INTENTIONALLY LEFT BLANK...
Page 46: ...40 BLANK...
Page 48: ...42 BLANK...
Page 54: ...48 BLANK...
Page 56: ...50 BLANK...
Page 62: ...56 BLANK...
Page 64: ...58 BLANK...
Page 66: ......
Page 67: ...I 280 REV 04 March 2002...