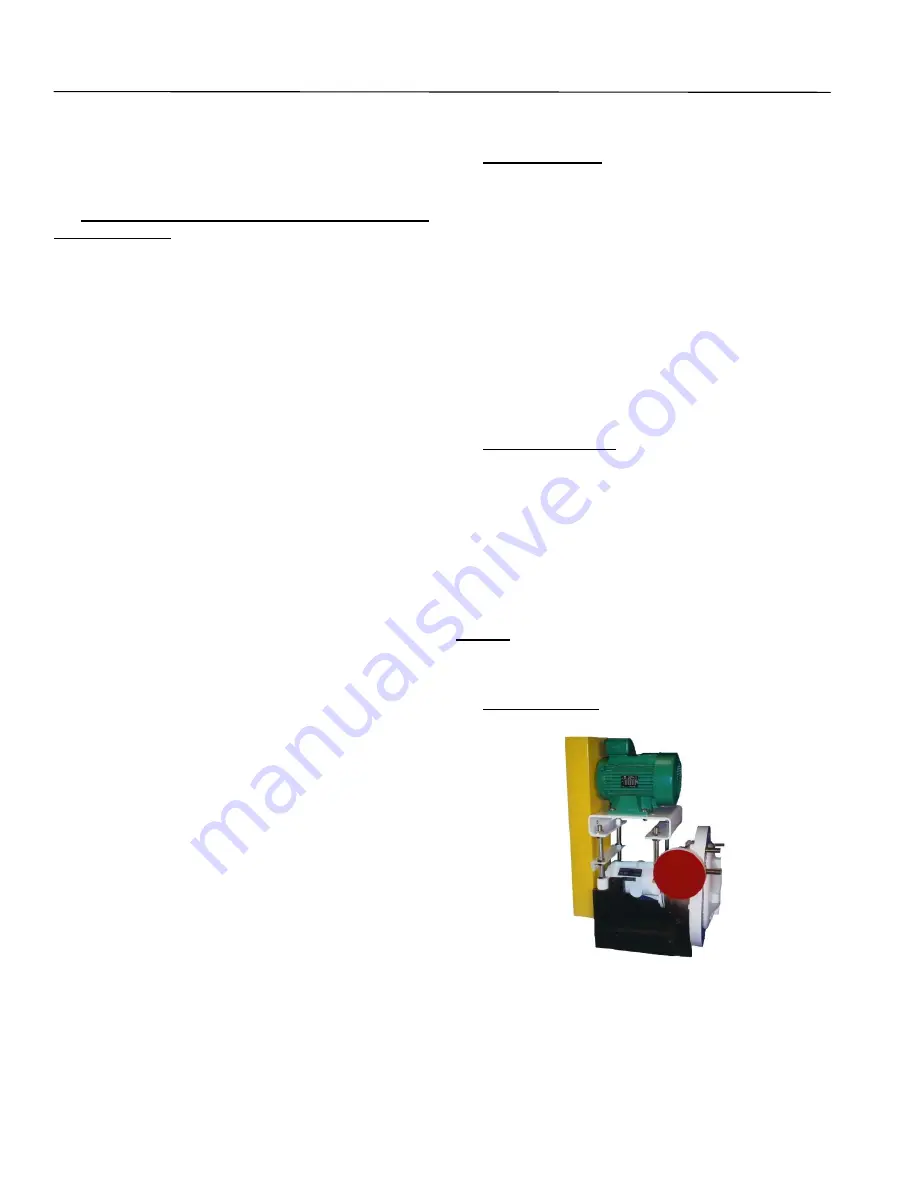
I-855
855
–
Filtrate Pump
855-15.04.EN
4
moving vane-type meters should not be
grounded nor held during measurements.
Do NOT use test equipment known to be
damaged or in poor condition.
H. NON-COMPLIANCE
WITH
SAFETY
INSTRUCTIONS.
Non-compliance
with
safety
instructions may result in personal injury, property
damage, or unnecessary damage to the pumping unit.
Non-compliance with these safety instructions will also
lead to forfeiture of any and all rights to claims for
damages. Non-compliance, can for example, result in:
Failure of important pumping unit functions.
Failure of prescribed maintenance and servicing
practices.
Hazard to personnel by electrical, mechanical,
and chemical effects.
Hazard to the environment due to leakage of
hazardous substances.
Avoid Possible Non-Compliance.
The following
specific safety precautions apply to the pumping unit:
Do NOT exceed maximum discharge pressure
on discharge case (100 psig/ 690 kpa).
Do NOT operate pump without fluid to seal or
packing.
Do NOT run pump dry for extended periods of
time (longer than 1/2 hour)
Do NOT run pump against a closed discharge
valve.
Do NOT exceed the Maximum rated speed
(2400 rpm).
A check valve should be installed in the
discharge line.
Pumps assembled by Carver without a motor
will have a Declaration of Incorporation and will
not have a CE mark. When a motor is added, all
guards must be installed, the motor must be CE
marked and the completed machine reviewed
for compliance for applicable EHSRs before a
CE mark is attached.
III. EQUIPMENT DESCRIPTION.
A. PUMP HISTORY.
The Filtrate Pump line was desig
ned in the late 1950’s
at the request of a large Original Equipment
Manufacturer (OEM) of vacuum filtration equipment.
The company had found that the typical centrifugal
pump would not operate against the high vacuum in a
filtrate receiver tank without the inclusion of a
hydrostatic leg in order to provide enough Net Positive
Suction Head Available (NPSHA) to prevent the pump
from cavitating and destroying itself.
The receiver tank flange-mounted Filtrate Pump was
designed to solve the OEM's problem and they have
been used in pumping liquids under vacuum or with very
low suction pressures ever since.
B. PUMP FEATURES.
The Filtrate Pumps do not require a hydrostatic leg, will
operate against vacuums up to 660 mm Hg (
26” Hg) on
the suction side and if, on occasion, it pumps the
receiver tank dry, or the inflow of process liquid into the
tank is interrupted, it will continue to run, will maintain
the vacuum in the system, and when the suction again
becomes flooded it will prime itself and resume pumping
the process liquid.
An important aspect of the pump’s
operation is that it accomplishes all of the foregoing
without
the use of mechanical or electrical level
controls on the receiver tank, thereby simplifying and
enhancing the reliability of the entire system.
C. PUMP DETAILS.
Figure 1. Model 855-OH Pump
The line has two variations. The standard is the flange
mounted Model 855-OH which features an overhead v-
belt drive arrangement for varying the pump speed and
Summary of Contents for 855 Series
Page 38: ...I 855 855 Filtrate Pump 855 15 04 EN 32 Figure 17 Optional Swing out Assembly ...
Page 39: ...I 855 855 Filtrate Pump 855 15 04 EN 33 Figure 18 Model 855 Tank Mounting Flange ...
Page 40: ...I 855 855 Filtrate Pump 855 15 04 EN 34 Figure 19 Model 855 Universal Discharge Flange ...
Page 41: ...I 855 855 Filtrate Pump 855 15 04 EN This page intentionally left blank ...