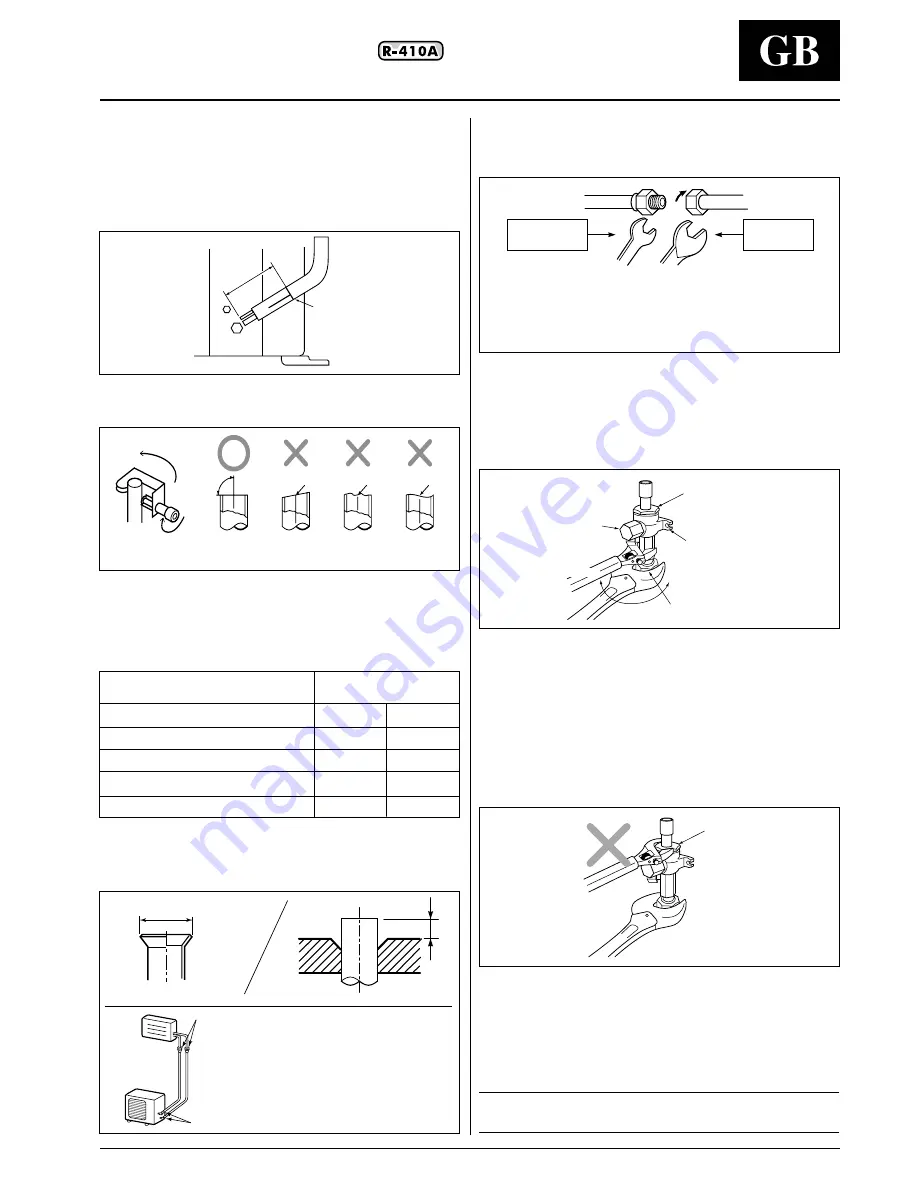
GB - 5
38VYX050/38VYX080
E N G L I S H
38 VYX 050
Pipe forming / positioning
• Pipe forming.
Form the pipe along with a marked line of the cabinet.
• End positioning of pipe.
Match the ends of both pipes at a distance of 85 mm apart from
the marked line.
Refrigerant piping
Flaring
1. Cut the pipe with a pipe cutter.
2. Insert a flare nut into the pipe, and flare the pipe.
As the flaring sizes of R410A differ from those of refrigerant R22,
the flare tools newly manufactured for R410A are recommended.
Table V: Pipe outer diameter
• In case of flaring for R410A with the conventional flare tool, pull it
out approx. 0.5 mm more than that of R22 to adjust to the
specified flare size.
The copper pipe gauge is useful for adjusting projection margin
size.
A
B
Outer dia. of copper pipe
A
+ 0
mm
-0,4
R410A
R22
6,35
9,1
9,0
9,52
13,2
13,0
12,7
16,6
16,2
15,9
19,7
19,4
90˚
Obliquity
Roughness
Warp
Flare at indoor unit side
Flare at outdoor unit side
Marked line
85 mm
lign the centres of the connecting pipes and tighten the flare nut
as strong as possible with your fingers.
Then fix the nut with a spanner and tighten it with torque wrench as
shown in the figure.
• As shown in the figure, use two spanners to unscrew or tighten
the valve flare nut, at gas side.
If using a single spanner, the nut cannot be tightened with
necessary tightening torque.
On the contrary, use a single spanner to loosen or tighten the flare
nut of the valve at liquid side.
REQUIREMENT:
1. Do not put the spanner on the cap. The valve may be broken.
2. If applying excessive torque, the nut may be broken according to
some installation conditions.
• After the installation work, be sure to check gas leak of connecting
part of the pipes with nitrogen.
• Pressure of R410A is higher than that of R22 (Approx. 1.6 times).
Therefore, using a torque wrench, tighten the flare pipe
connecting sections which connect the indoor/outdoor units at the
specified tightening torque.
Incomplete connections may cause not only a gas leak, but also a
trouble of the refrigeration cycle.
IMPORTANT:
Do not apply refrigerating machine oil to the flared surface.
Cover
Half union or packed valve
Flare nut
Internally threaded side
C
D
Externally threaded side
C Fix with spanner.
D Tighten with torque wrench.
Cover
Piping valve
Flare nut
E Tightened
F Loosened
E
F