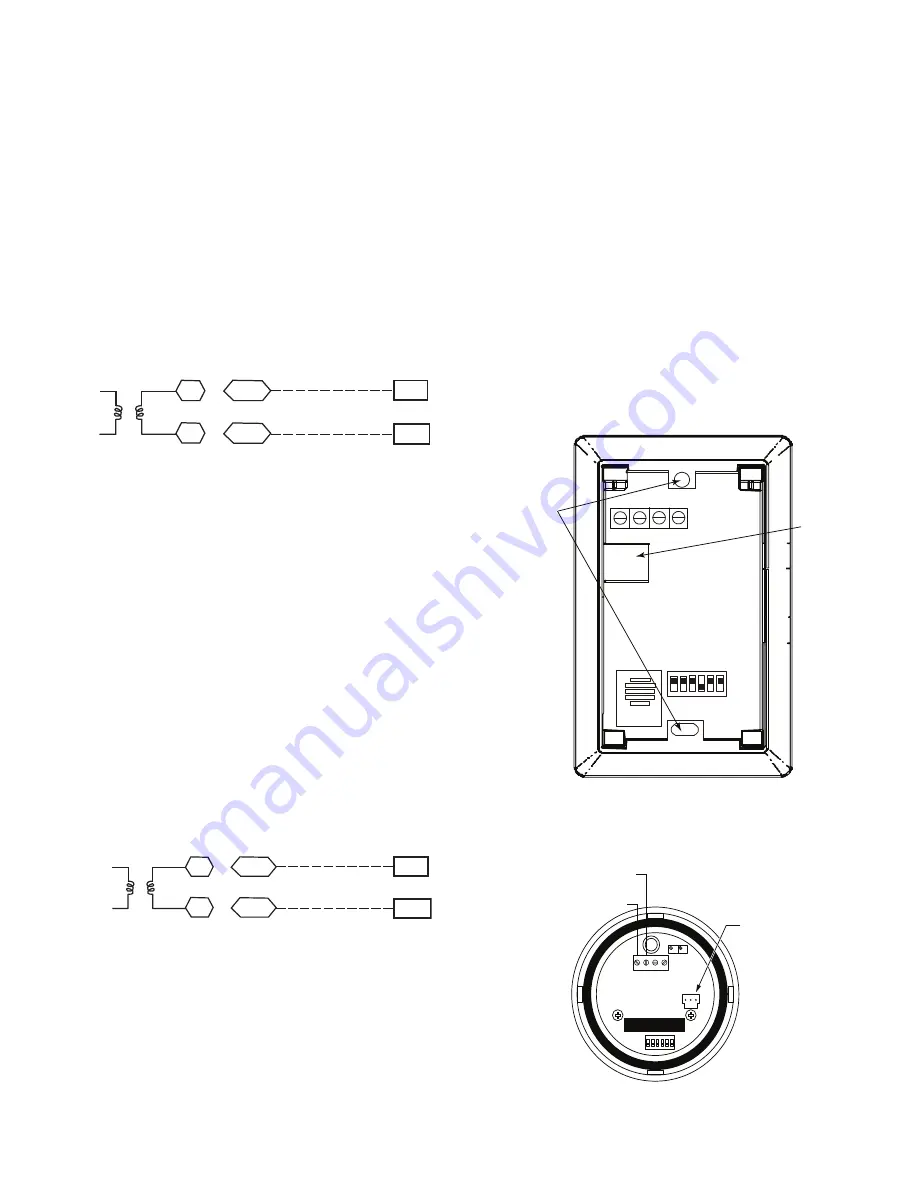
57
Do not mount the IAQ sensor in drafty areas such as near
supply ducts, open windows, fans, or over heat sources. Al-
low at least 3 ft (0.9 m) between the sensor and any corner.
Avoid mounting the sensor where it is influenced by the sup-
ply air; the sensor gives inaccurate readings if the supply air
is blown directly onto the sensor or if the supply air does not
have a chance to mix with the room air before it is drawn into
the return airstream.
Wiring the Indoor Air Quality Sensor
For each sensor, use two 2-conductor 18 AWG (American
Wire Gage) twisted-pair cables (unshielded) to connect the
separate isolated 24 vac power source to the sensor and to
connect the sensor to the control board terminals.
To connect the sensor to the control, identify the positive
(4 to 20 mA) and ground (SIG COM) terminals on the sensor.
See Fig. 68. Connect the 4-20 mA terminal to the RTU Open
controller at J4-2 and connect the SIG COM terminal to the
RTU Open controller at J4-3. See Fig. 85.
Fig. 85 — RTU Open Controller/Indoor CO
2
Sensor
(33ZCSENCO2) Connections
OUTDOOR AIR QUALITY SENSOR (P/N 33ZCSENCO2
PLUS WEATHERPROOF ENCLOSURE)
The outdoor air CO
2
sensor is designed to monitor carbon
dioxide (CO
2
) levels in the outside ventilation air and inter-
face with the ventilation damper in an HVAC system. The
OAQ sensor is packaged with an outdoor cover. See Fig. 70.
The outdoor air CO
2
sensor must be located in the economiz-
er outside air hood.
Wiring the Outdoor Air CO
2
Sensor
A dedicated power supply is required for this sensor. A
two-wire cable is required to wire the dedicated power supply
for the sensor. The two wires should be connected to the pow-
er supply and terminals 1 and 2.
To connect the sensor to the control, identify the positive
(4 to 20 mA) and ground (SIG COM) terminals on the OAQ
sensor. See Fig. 68. Connect the 4 to 20 mA terminal to the
RTU Open controller at J4
-
5. Connect the SIG COM terminal
to the RTU Open controller at J4
-
6. See Fig. 86.
Fig. 86 — RTU Open Controller/Outdoor CO
2
Sensor
(33ZCSENCO2) Connections
SPACE RELATIVE HUMIDITY SENSOR OR
HUMIDISTAT
Humidi-MiZer
®
System Control Wiring
In units equipped with the Humidi-MiZer option there are
two pink (PNK) wires loose in the control box used to control
the dehumidification function of the unit. These pink wires
are meant to be tied to a space humidistat or thermidistat on
an electromechanical unit. On RTU Open controller equipped
units these pink wires must be connected to J11
-
7 and 8 to al-
low the Open board to operate the dehumidification function
for the unit. Disconnect the J11 Phoenix style connector from
the board and use the plug screws to secure the pink wires in
pins 7 and 8, reconnect the plug to the board at J11.
Relative Humidity Sensors (Space or Duct Mounted)
The accessory space humidity sensor (33ZCSENSRH-01)
or duct humidity sensor (33ZCSENDRH-01) is used to mea-
sure the relative humidity of air within the space or return air
duct. The RH reading is used to control the Humidi-MiZer
option of the rooftop unit. For wiring distances up to 500 ft
(152 m), use a 3-conductor, 18 or 20 AWG shielded cable.
The shield must be removed from the sensor end of the cable
and grounded at the unit end. The current loop power for sen-
sor is provided by the RTU Open controller as 24 vdc. Refer
to the instructions supplied with the RH sensor for the electri-
cal requirements and terminal locations. RTU Open controller
configurations must be changed after adding an RH sensor.
See Fig. 87 and 88 for typical RH sensor wiring.
• J4
-
1 or J4
-
4 = 24 vdc loop power
• J4
-
2 or J4
-
5 = 4-20mA signal input
NOTE: The factory default for dehumidification control is nor-
mally open humidistat.
Fig. 87 — Space Relative Humidity Sensor Typical
Wiring
Fig. 88 — Duct Relative Humidity Sensor Typical
Wiring
SEN
COM
J4-2
J4-3
IAQ Sensor
24 VAC
SEN
COM
J4-5
J4-6
OAQ Sensor/RH Sensor
24 VAC
SW2
1
2
3
4
5
6
ON
Io
Vin
Gnd
Vo
MOUNTING
HOLES
WIRING
OPENING
Vin - J4-1 or J4-4 24 vdc
Io - J4-2 or J4-5 -20mA output
SPAN
ZERO
4-20
mA
VAC
or
VDC
GND 0-5V
or
0-10V
1
2
3
4
5
6
ON
J4-1 or J4-4 + 24 VDC
SUPPLY VOLTAGE
J4-2 or J4-5 (-)4 to 20 mA Current
LOOP OUTPUT TO RTU OPEN
RELATIVE HUMIDITY SENSOR
(POLARIZED MALE CONNECTOR)
Summary of Contents for WeatherMaster 50HC14
Page 4: ...4 Fig 2 Unit Dimensional Drawing 14 Size Unit ...
Page 5: ...5 Fig 2 Unit Dimensional Drawing 14 Size Unit cont HORIZONTAL ECONOMIZER VERTICAL ECONOMIZER ...
Page 8: ...8 Fig 4 Roof Curb Details ...
Page 24: ...24 Fig 46 Typical Humidi MiZer Adaptive Dehumidification System Humidistat Wiring ...
Page 39: ...39 Fig 54 50HC14 Control Box Component Locations with ComfortLink Controls ...
Page 40: ...40 Fig 55 50HC14 ComfortLink Control Wiring Diagram ...
Page 41: ...41 Fig 56 50HC14 ComfortLink Power Wiring Diagram ...
Page 42: ...42 Fig 57 50HC14 ComfortLink with Humidi MiZer Power Wiring Diagram ...
Page 44: ...44 Fig 60 PremierLink Wiring Schematic ...
Page 45: ...45 Fig 61 PremierLink Wiring Schematic with Humidi MiZer System Option ...
Page 53: ...53 Fig 80 RTU Open System Control Wiring Diagram ...
Page 54: ...54 Fig 81 RTU Open System Control Wiring Diagram with Humidi MiZer System Option ...
Page 64: ......
Page 65: ......