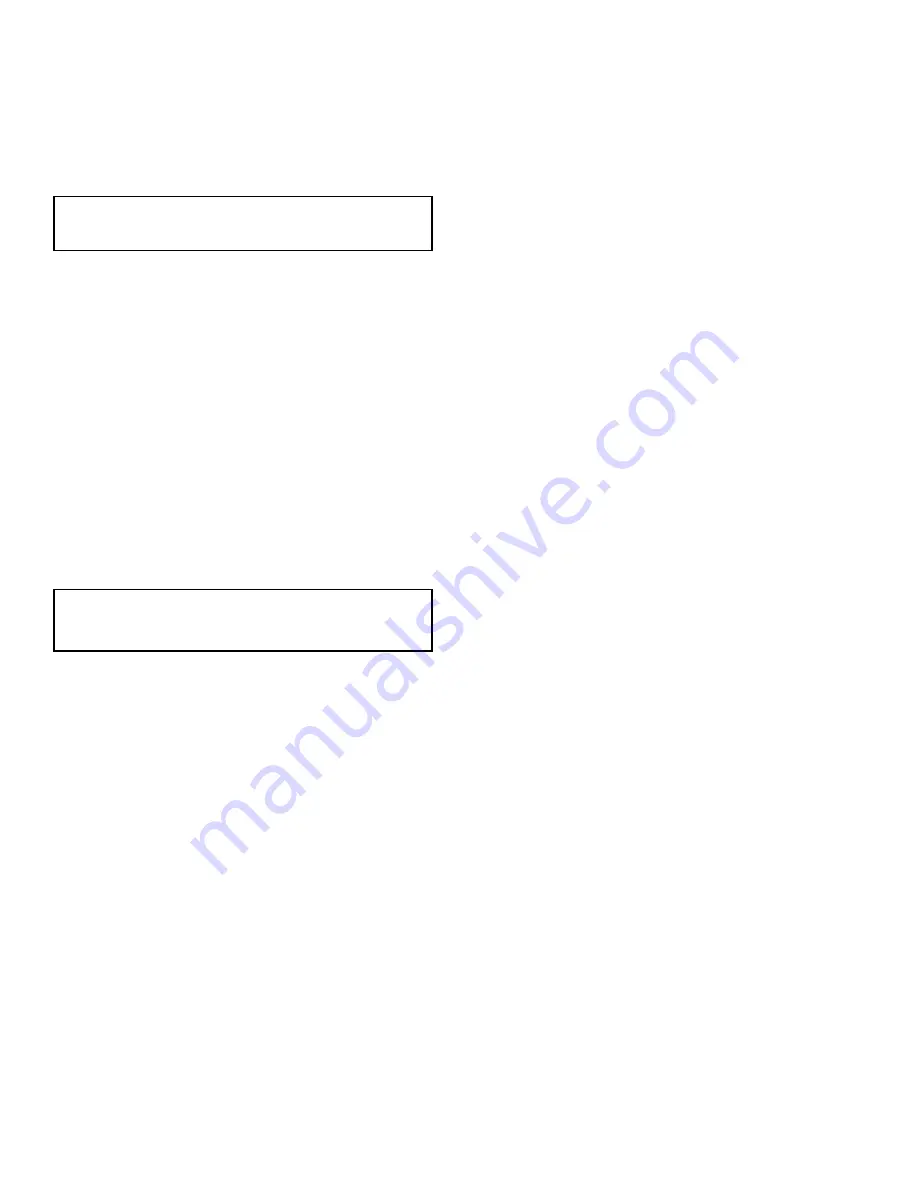
8
Accessory Installation
Check to make sure that all accessories, including space ther-
mostats and sensors, have been installed and wired as required
by the instructions and unit wiring diagrams.
Crankcase Heaters
Crankcase heaters are energized as long as there is power to the
unit, except when the compressors are running.
Evaporator Fan
Fan belt and fixed pulleys are factory-installed. See Tables 3-24
for fan performance. Remove tape from fan pulley, and be sure
that fans rotate in the proper direction. Static pressure drop is
shown in Table 25. See Tables 26-28 for motor limitations.
FIELD-SUPPLIED FAN DRIVES
Supply fan and power exhaust fan drives are fixed-pitch, non-
adjustable selections, for maximum reliability and long belt
life. If the factory drive sets must be changed to obtain other
fan speeds, consult the nearest Browning Manufacturing Co.
sales office with the required new wheel speed and the data
from Physical Data and Supply Fan Drive Data tables (center
distances, motor and fan shaft diameters, motor horsepower) in
Installation Instructions for a modified drive set selection. For
minor speed changes, the fan sheave size should be changed.
(Do not reduce the size of the motor sheave; this will result in
reduced belt horsepower ratings and reduced belt life.) See
page 154 for belt installation procedure.
Controls
Use the following steps for the controls:
1. Set any control configurations that are required (field-
installed accessories, etc.). The unit is factory configured
for all appropriate factory-installed options.
2. Enter unit set points. The unit is shipped with the set point
default values. If a different set point is required, use the
scrolling marquee, Navigator™ display, or CCN interface
to change the configuration values.
3. If the internal time schedules are going to be used, config-
ure the Occupancy schedule.
4. Verify that the control time periods programmed meet cur-
rent requirements.
5. Use Service Test mode to verify operation of all major
components.
6. If the unit is a VAV unit make sure to configure the static
pressure set point. To check out the VFD, use the VFD
instructions shipped with the unit.
Gas Heat
Verify gas pressure before turning on gas heat as follows:
1. Turn off field-supplied manual gas stop, located external
to the unit.
2. Connect pressure gages to supply gas tap, located at field-
supplied manual shutoff valves.
3. Connect pressure gages to manifold pressure tap on unit
gas valve.
4. Supply gas pressure must not exceed 13.5 in. wg. Check
pressure at field-supplied shut-off valve.
5. Turn on manual gas stop and initiate a heating demand.
Jumper R to W1 in the control box to initiate heat.
6. Use the Service Test procedure to verify all heat stages of
operation.
7. After the unit has run for several minutes, verify that
incoming pressure is 5.0 in. wg or greater and that the
manifold pressure is 3.5 in. wg. If manifold pressure must
be adjusted, refer to the Gas Valve Adjustment section on
page 177.
IMPORTANT: Unit power must be on for 24 hours prior to
start-up of compressors. Otherwise, damage to compressors
may result.
IMPORTANT: The unit is shipped with the unit control dis-
abled. To enable the control, set Local Machine Disable
(
Service Test
STOP
) to No.
Summary of Contents for Weathermaster 48P2030-100
Page 130: ...130 Fig 19 Typical Power Schematic Sizes 040 075 Shown ...
Page 131: ...131 Fig 20 Main Base Board Input Output Connections ...
Page 132: ...132 Fig 21 RXB EXB CEM SCB Input Output Connections ...
Page 133: ...133 Fig 22 Typical Gas Heat Unit Control Wiring 48P030 100 Units Shown ...
Page 134: ...134 Fig 23 Typical Electric Heat Wiring 50P030 100 Units Shown ...
Page 135: ...135 Fig 24 Typical Power Wiring 115 V ...
Page 136: ...136 Fig 25 Typical Gas Heat Section Size 030 050 Units Shown ...
Page 138: ...138 Fig 27 Component Arrangement Size 030 035 Units ...
Page 139: ...139 Fig 28 Component Arrangement Size 040 075 Units ...
Page 140: ...140 Fig 29 Component Arrangement Size 090 100 Units ...