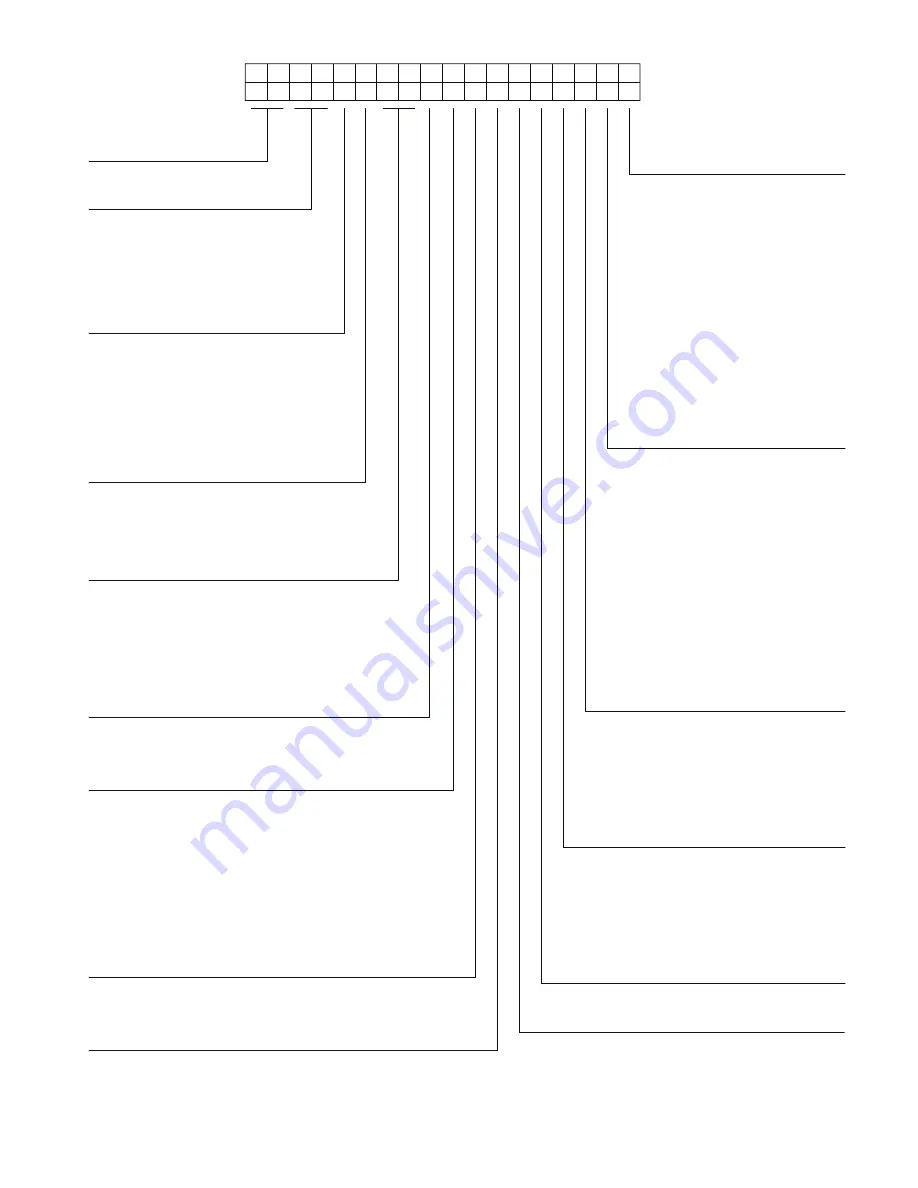
5
Fig. 1 — 48HC 07-12 Model Number Nomenclature (Example)
4
8
H
C
D
E
0
9
A
2
A
6
A
0
A
3
B
0
1
2
3
4
5
6
7
8
9
10
11
12
13
14
15
16
17
18
Model Series - WeatherMaster
®
HC - High Efficiency
Unit Heat Type
48 - Gas Heat Packaged Rooftop
Cooling Tons
07 - 6 ton
08 - 7.5 ton
09 - 8.5 ton
11 - 10 ton (12.0 EER)
12 - 10 ton (11.5 EER)
Heat Options
D = Low Gas Heat
E = Medium Gas Heat
F = High Gas Heat
S = Low Heat w/ Stainless Steel Exchanger
R = Medium Heat w/ Stainless Steel Exchanger
T = High Heat w/ Stainless Steel Exchanger
(Low NO
x
models include – Stainless Steel HX)
Sensor Options
A = None
B = RA Smoke Detector
C = SA Smoke Detector
D = RA + SA Smoke Detector
E = CO
2
F = RA Smoke Detector and CO
2
G = SA Smoke Detector and CO
2
H = RA + SA Smoke Detector and CO
2
Indoor Fan Options
1 = Standard Static Option - Belt Drive
2 = Medium Static Option - Belt Drive
3 = High Static Option - Belt Drive
Refrig. Systems Options
A = Single stage cooling models
B = Single stage cooling models
with
Humidi-MiZer
®
D = Two stage cooling models
E = Two stage cooling models with Humidi-MiZer
F = Single stage cooling models with
MotorMaster Low Ambient Controller
G = Two stage cooling models with
MotorMaster Low Ambient Controller
Coil Options (RTPF) (Outdoor - Indoor - Hail Guard)
A = Al/Cu - Al/Cu
B = Precoat Al/Cu - Al/Cu
C = E-coat Al/Cu - Al/Cu
D = E-coat Al/Cu - E-coat Al/Cu
E = Cu/Cu - Al/Cu
F = Cu/Cu - Cu/Cu
M = Al/Cu -Al/Cu — Louvered Hail Guard
N = Precoat Al/Cu - Al/Cu — Louvered Hail Guard
P = E-coat Al/Cu - Al/Cu — Louvered Hail Guard
Q = E-coat Al/Cu - E-coat Al/Cu — Louvered Hail Guard
R = Cu/Cu - Al/Cu — Louvered Hail Guard
S = Cu/Cu - Cu/Cu — Louvered Hail Guard
Voltage
1 = 575/3/60
5 = 208-230/3/60
6 = 460/3/60
Design Revision
A = Factory Design Revision
Base Unit Controls
0 = Electromechanical Controls can be used with W7212
EconoMi$er (Non-Fault Detection and Diagnostic)
1 = PremierLink
TM
Controller
2 = RTU Open Multi-Protocol Controller
6 = Electro-mechanical w/ 2-speed fan and W7220
Econo controller controls. Can be used with W7220
EconoMi$er X (w/ Fault Detection & Diagnostic)
D = ComfortLink Controls
Intake / Exhaust Options
A = None
B = Temperature Economizer w/ Barometric Relief
F = Enthalpy Economizer w/ Barometric Relief
K = 2-Position Damper
U = Low Leak Temperature Economizer
w/ Barometric Relief
W = Low Leak Enthalpy Economizer
w/ Barometric Relief
Service Options
0 = None
1 = Unpowered Convenience Outlet
2 = Powered Convenience Outlet
3 = Hinged Panels
4 = Hinged Panels and
Unpowered Convenience Outlet
5 = Hinged Panels and
Powered Convenience Outlet
C = Foil Faced Insulation
D = Foil Faced Insulation with
Unpowered Convenience Outlet
E = Foil Faced Insulation with
Powered Convenience Outlet
F = Foil Faced Insulation & Hinged Panels
G = Foil Faced Insulation & Hinged Panels
with Unpowered Convenience Outlet
H = Foil Faced Insulation & Hinged Panels
with Powered Convenience Outlet
Factory Assigned
0 = Standard
1 = LTL
Electrical Options
A = None
B = HACR Breaker
C = Non-Fused Disconnect
D = Thru-The-Base Connections
E = HACR and Thru-The Base Connections
F = Non-Fused Disconnect and
Thru-The-Base
Connections
G = 2-Speed Indoor Fan (VFD) Controller
H = 2-Speed Fan Controller (VFD) and
HACR
Breaker
J = 2-Speed Fan Controller (VFD) and
Non-Fused
Disconnect
K = 2-Speed Fan Controller (VFD) and
Thru-The-Base
Connections
L = 2-Speed Fan Controller (VFD) w/ HACR
Breaker and Thru-The Base Connections
M = 2-Speed Fan Controller (VFD) with
Non-Fused Disconnect and
Thru-The-Base
Connections
Example:
Position:
Summary of Contents for WeatherMaster 48HC07 Series
Page 6: ...6 Fig 2 Unit Dimensional Drawing Sizes 07 09 ...
Page 7: ...7 Fig 2 Unit Dimensional Drawing Sizes 07 09 cont ...
Page 8: ...8 Fig 3 Unit Dimensional Drawing Sizes 11 and 12 ...
Page 9: ...9 Fig 3 Unit Dimensional Drawing Sizes 11 and 12 cont ...
Page 26: ...26 Fig 41 Typical Humidi MiZer Adaptive Dehumidification System Humidistat Wiring ...
Page 28: ...28 Fig 43 Electro Mechanical Control Wiring Diagram ...
Page 29: ...29 Fig 44 Electro Mechanical Control Wiring Diagram with Humidi MiZer System ...
Page 30: ...30 Fig 45 Typical ComfortLink Control Wiring Diagram 48HC 08 09 shown ...
Page 32: ...32 Fig 47 Typical PremierLink Control Wiring Diagram ...
Page 33: ...33 Fig 48 Typical PremierLink Control Wiring Diagram with Humidi MiZer System Option ...
Page 34: ...34 Fig 49 Typical RTU Open Controller Wiring Diagram ...
Page 35: ...35 Fig 50 Typical RTU Open Controller Wiring Diagram with Humidi MiZer System Option ...
Page 53: ......