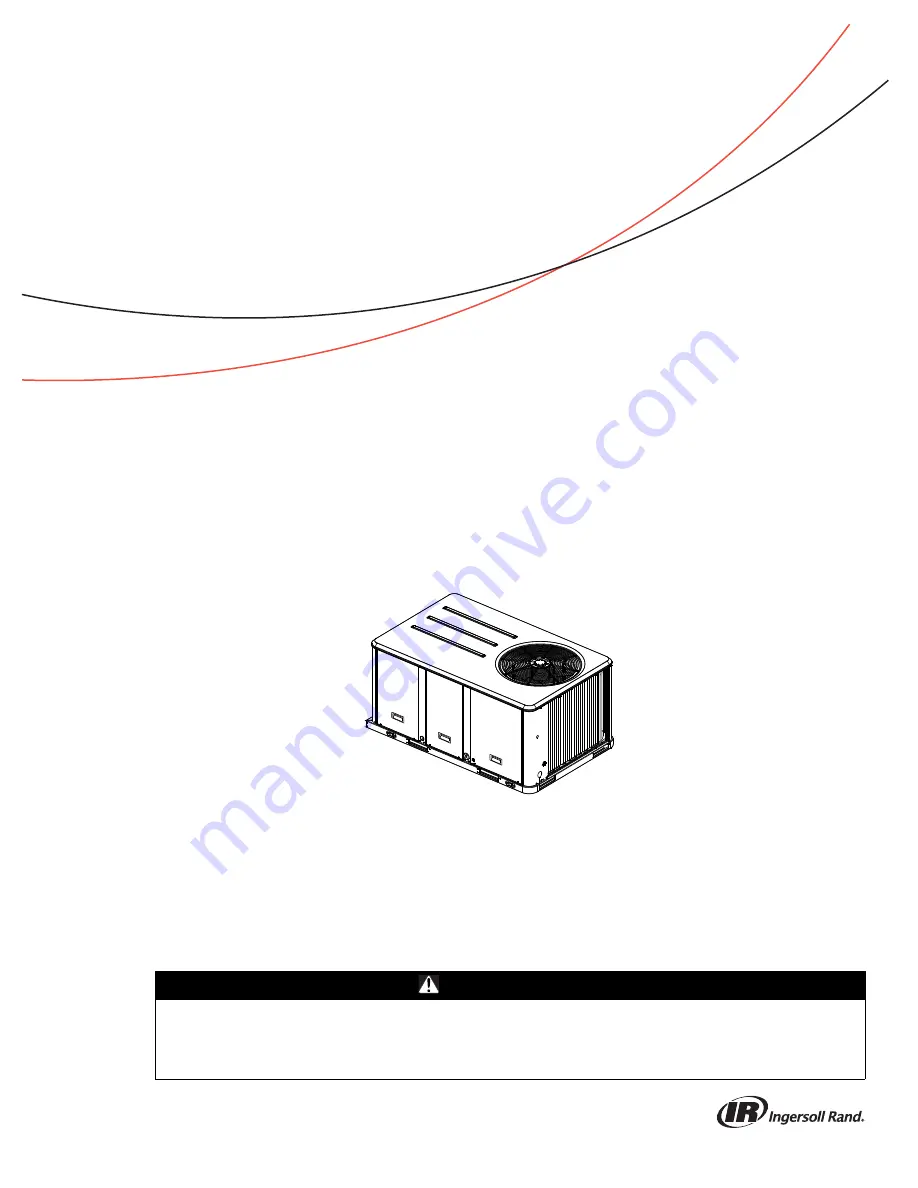
SAFETY WARNING
Only qualified personnel should install and service the equipment. The installation, starting up, and servicing
of heating, ventilating, and air-conditioning equipment can be hazardous and requires specific knowledge and
training. Improperly installed, adjusted or altered equipment by an unqualified person could result in death or
serious injury. When working on the equipment, observe all precautions in the literature and on the tags,
stickers, and labels that are attached to the equipment.
Packaged Rooftop Air Conditioners
Precedent™ — Heat Pump
3 to 10 Tons — 60 Hz
Installation, Operation,
and Maintenance
Model Numbers
WSC036H-WSC060H
WSC072H, WSC090E, WSC102H & WSC120H
W/DHC036H-W/DHC060H
RT-SVX23M-EN
April 2018
Summary of Contents for Precedent WSC072E
Page 67: ......