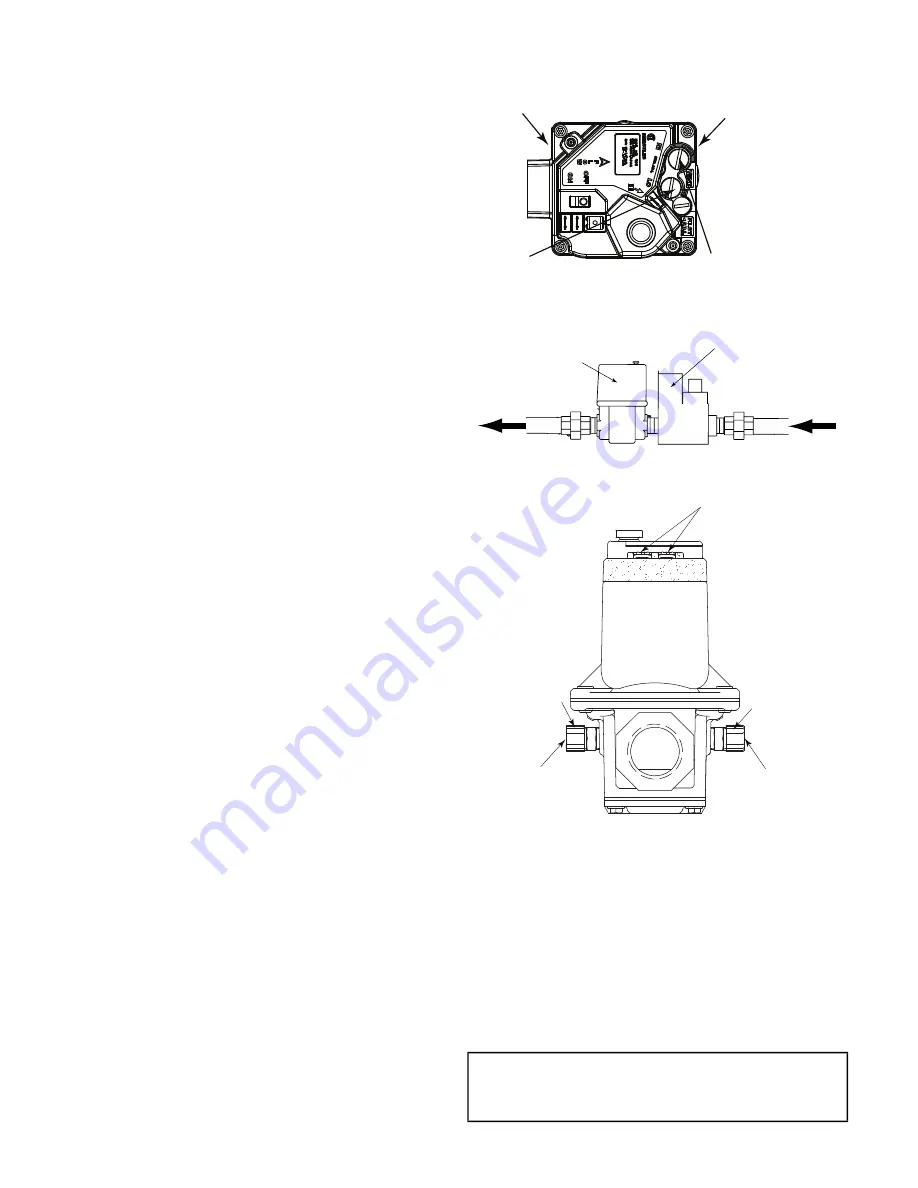
184
Gas System Adjustment (48N Only)
TWO-STAGE GAS VALVE ADJUSTMENT
The gas valve opens and closes in response to the unit control.
When power is supplied to valve terminals D1 and C2, the
main valve opens to its preset position.
The regular factory setting is stamped on the valve body
(3.3 in. wg).
To adjust regulator:
1. Set thermostat at setting for no call for heat.
2. Switch main gas valve to OFF position.
3. Remove
1
/
8
-in. pipe plug from manifold or gas valve pres
-
sure tap connection. Install a suitable pressure-measuring
device.
4. Switch main gas valve to ON position.
5. Set thermostat at setting to call for heat.
6. Remove screw cap covering regulator adjustment high-fire
screw (see Fig. 78).
7. Turn adjustment screw clockwise to increase pressure or
counterclockwise to decrease pressure.
8. Once desired pressure is established, set thermostat setting
for no call for heat, turn off main gas valve, remove pres
-
sure-measuring device, and replace
1
/
8
-in. pipe plug and
screw cap.
MODULATING GAS VALVE ADJUSTMENT
The modulating gas valve is an electrically operated valve con
-
trolled by a 0 to 20 vdc input directly to valve terminals or
from an external controller. The modulating gas valve is in
-
stalled downstream from a separate pressure regulator, such as
a 2-stage gas valve. See Fig. 79.
The modulating gas valve has both sides fitted for low fire ad
-
justment. When 0 vdc is applied at the connect terminals, the
bypass provides a minimum outlet pressure of 0.3 in. wg for
2.0 in. wg at the gas regulator upstream the modulating valve
(factory setting).
For low fire adjustment (see Fig. 80):
1. Disconnect a wire from modulating valve connect terminals.
NOTE: Do not allow wire to come into contact with any
other part.
2. Remove the left bypass cap.
3. Turn adjustment screw using a small screwdriver to the
desired low fire adjustment.
NOTE: Clockwise screw rotation reduces flow rate. Do
not over tighten.
MAIN BURNERS
For all applications, main burners are factory set and should re
-
quire no adjustment.
MAIN BURNER REMOVAL AND REPLACEMENT
1. Shut off (field-supplied) manual main gas valve.
2. Shut off power to unit.
3. Remove gas section access door, door frame, and corner post.
4. Disconnect gas piping from gas valve inlet.
5. Remove wires from gas valve.
6. Remove wires from rollout switch.
7. Remove sensor wire and igniter cable form IGC board.
8. Remove 2 screws securing manifold bracket to basepan.
9. Remove 2 screws that hold the burner support plate flange
to the vestibule plate.
10. Lift burner assembly out of unit.
11. Replace burner assembly. Reinstall by reversing Steps 1 to 10.
Fig. 78 —
Two-Stage Gas Valve
Fig. 79 —
Modulating Gas Valve Location
Fig. 80 —
Modulating Gas Valve Bypass
Adjustment
Moisture/Liquid Indicator
A clear flow of liquid refrigerant indicates sufficient charge in
the system. Bubbles indicate undercharged system or the pres
-
ence of noncondensables. Moisture in the system measured in
parts per million (ppm) changes the color of the indicator:
Green — moisture below 45 ppm (dry)
Chartreuse — 45 to 130 ppm (caution!)
Yellow — moisture above 130 ppm (wet)
Change filter driers at the first sign of moisture in the system.
See Carrier Charging Handbook for more information.
IMPORTANT: Unit must be in operation at least 12 hours
before moisture indicator can give an accurate reading.
With unit running, indicating element must be in contact
with liquid refrigerant to give a true reading.
INLET PRESSURE
TAP (ON SIDE)
1/8-IN. 27 NPT
OUTLET PRESSURE
TAP (ON SIDE)
1/8-IN. 27 NPT
HIGH-FIRE REGULATOR
ADJUSTMENT SCREW
LOW-FIRE REGULATOR
ADJUSTMENT SCREW
2-STAGE
GAS VALVE
MODULATING
GAS VALVE
TERMINALS
RIGHT
BYPASS
CAP
LEFT
BYPASS
CAP
LEFT
ADJUSTMENT
SCREW
(HIDDEN)
RIGHT
ADJUSTMENT
SCREW
(HIDDEN)
Summary of Contents for WeatherExpert 48N2
Page 135: ...135 Fig 18 48 50N Typical Power Schematic Nominal 075 Ton Unit Shown ...
Page 136: ...136 Fig 19 48 50N Typical Power Schematic Nominal Ton 90 150 Units Shown ...
Page 137: ...137 Fig 20 48 50N Main Base Board Input Output Connections ...
Page 138: ...138 Fig 21 48 50N RXB EXB CEM Input Output Connections a48 9307 ...
Page 139: ...139 Fig 22 48 50N EXV SCB Input Output Connections a48 9308 ...
Page 140: ...140 Fig 23 48N Typical Modulating Gas Heat Unit Control Wiring ...
Page 141: ...141 Fig 24 50N Typical Electric Heat Unit Control Wiring ...
Page 144: ...144 Fig 27 48N Typical Gas Heat Section Wiring Nominal Ton 120 to 150 Units ...
Page 145: ...145 Fig 28 48 50N Typical Power Component Control Wiring 460 v ...
Page 146: ...146 Fig 29 48 50N Component Control Wiring 575 v Nominal Ton 075 to 150 Units ...
Page 147: ...147 Fig 30 48 50N Component Arrangement Power Box ...
Page 148: ...148 Fig 31 48 50N Component Arrangement Control Box ...
Page 240: ...240 APPENDIX D VFD INFORMATION CONT Fig G VFD Bypass Wiring Diagram WHEN USED ...