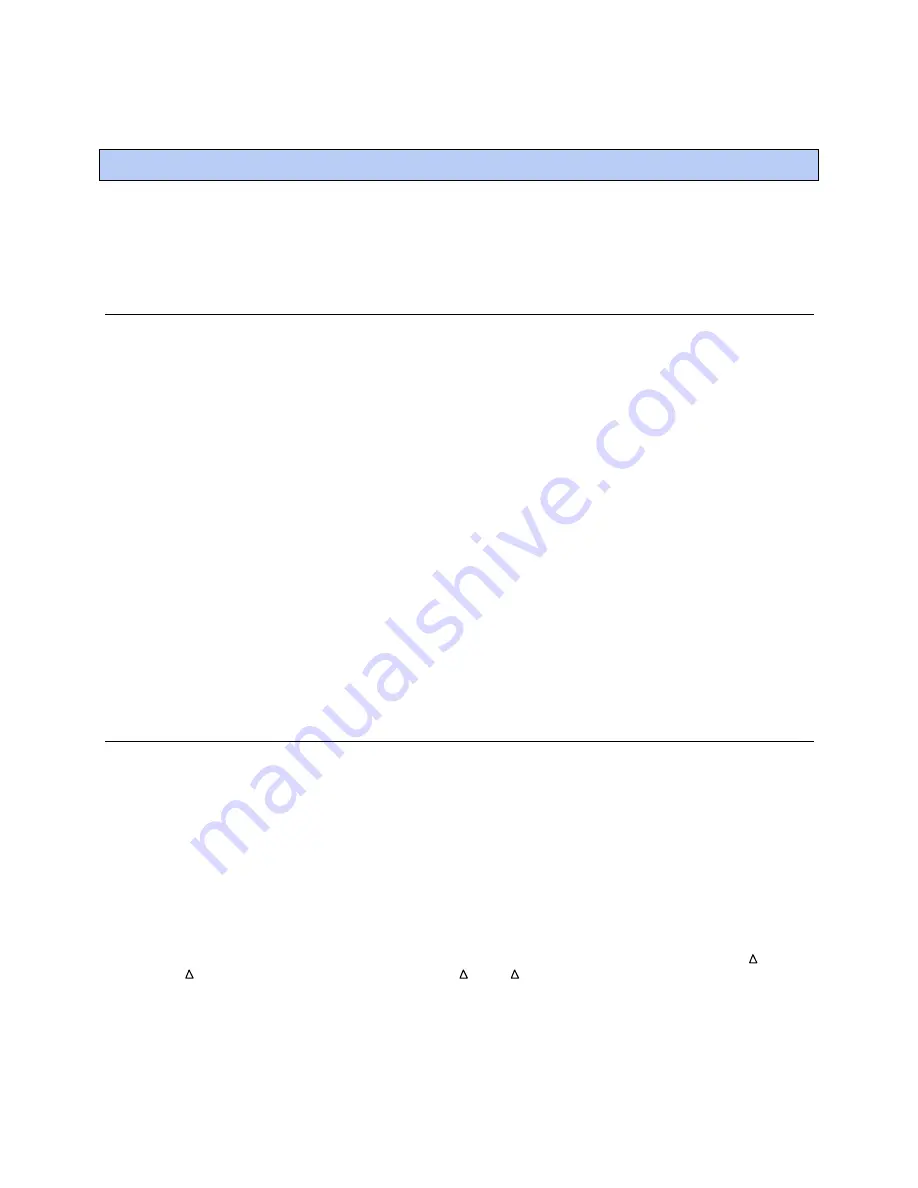
Sequence of operation
TruVu™ VVTBP
-E2
©2022 Carrier.
Installation and Start-up Guide
All rights reserved.
41
The TV-VVTBP-E2 maintains supply duct static pressure under all system operating conditions and can operate as
part of a linked VVT system or as a stand-alone controller.
Duct static pressure control
The TV-VVTBP-E2 modulates a bypass damper or VFD to maintain the static pressure in the supply duct of the
pressure-dependent VVT system. The TV-VVTBP-E2 has a damper actuator that provides 45 in./lbs (5 Nm) of
torque.
You can use the controller's 0
–
10 Vdc output to:
•
Drive a larger actuator if the TV-VVTBP-E2's actuator's torque is insufficient. The actuator must be installed so
that 0 volts causes the bypass damper to fully open. See
NOTE
below and High-torque actuator.
•
Drive multiple damper actuators from a single bypass controller. See
NOTE
below and Linked actuators.
•
Control a VFD
NOTE
You cannot use the TV-VVTBP-E2's actuator if external actuator(s) are wired to the analog output.
If linkage is active, normal duct static pressure control is overridden if the linked air source is in either of the
following modes:
•
Fire shutdown or evacuation mode
–
The bypass damper will be fully open. If controlling a VFD, the VFD
output will be at 0%.
•
Pressurization mode
–
The bypass damper will be fully closed. If controlling a VFD, the VFD output will be at
100%.
LAT monitoring and limiting
To protect the air source from excessive supply air temperature conditions, the TV-VVTBP-E2 monitors the supply
air temperature. If the temperature reaches either the
Minimum Cooling SAT
[45°F (7.2°C) default] or the
Maximum Heating SAT
[120° F (48.9°C) default], the Bypass controls to the
LAT Duct Static Pressure Setpoint
which increases airflow through the air source.
The amount of increase in airflow is related to the square root of the pressure increase. For example, a 25%
increase in airflow at 1 in. (.249 kPa) of static pressure would require a 56% increase in duct static pressure [(1
in.H
2
O (.249 kPa) * (1.25)
2
) = 1.56 in. H
2
O (.388 kPa)]. The default
LAT Duct Static Pressure Setpoint
of 0.8
in.H
2
O (.199 kPa) provides a maximum 25% increase in airflow over the default Duct Static Pressure Setpoint of
.5 in.H
2
O (.125 kPa). [(.5 in.H
2
O (.125 kPa)* (1.25)
2
) = .75 [~.8] in.H
2
O (.199 kPa)]. When the LAT exceeds the
Maximum Heating SAT
or
Minimum Cooling SAT
, the controller detects and indicates the excessive LAT condition
and displays the
Controlling Pressure Setpoint
and the associated
LAT Airflow Increase
(%).
The Bypass does not resume normal control to the Duct Static Pressure Setpoint until the SAT drops 15 °F
(8.3 °C) below the Maximum Heating Sat or rises 7 °F (3.9 °C) above the Minimum Cooing Setpoint.
If the supply air temperature exceeds the configured limits, a
Supply Air Temperature Alarm
is generated. If
Linkage is active, the controller monitors the supply air temperature from the equipment rather than its own
temperature input for faster response.
Sequence of operation
Summary of Contents for TruVu VVTBP-E2
Page 5: ...Document revision history 84...
Page 6: ......
Page 91: ......
Page 92: ...Carrier 2022 Catalog No 11 808 875 01 7 22 2022...