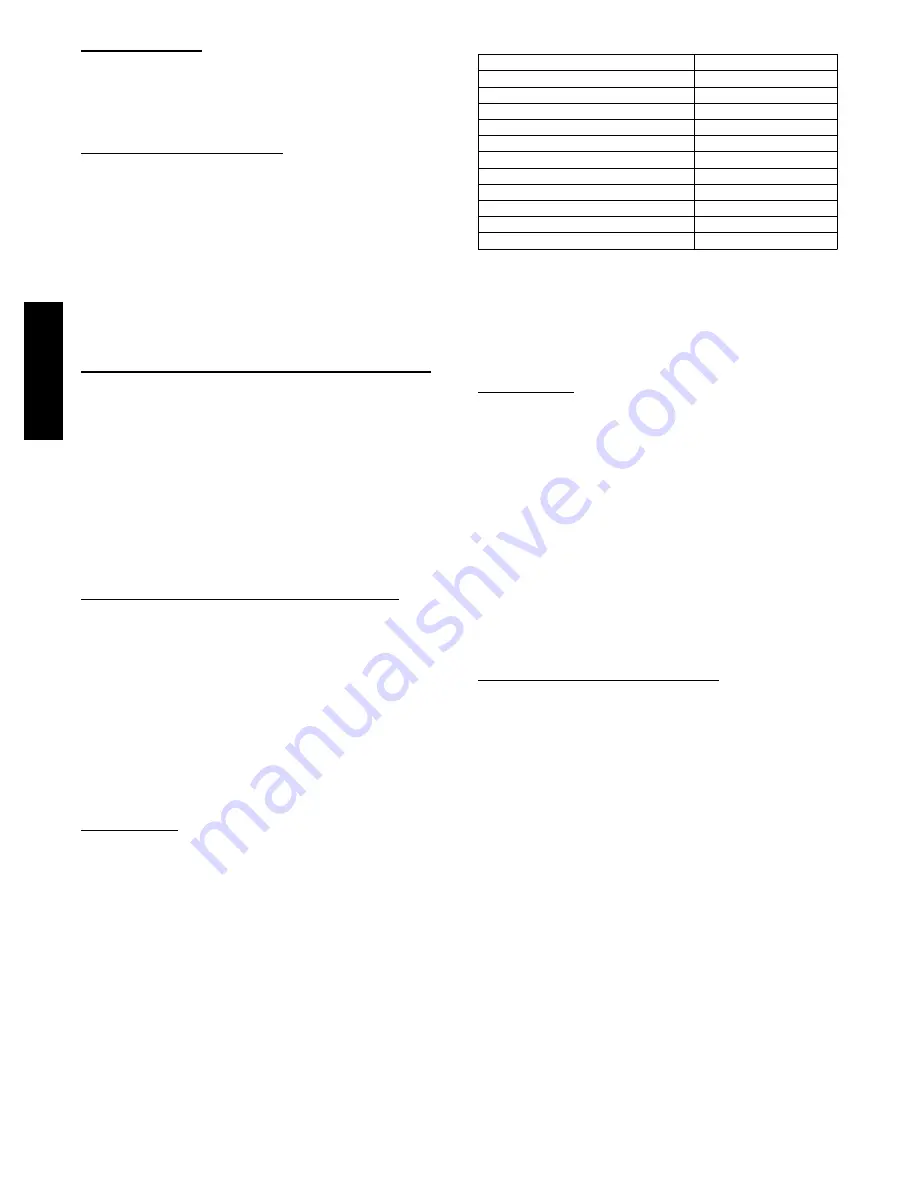
22
Normal Operation
An LED (light--emitting diode) indicator is provided on the
integrated gas unit controller (IGC) to monitor operation. The IGC
is located by removing the control access panel (see Fig. 20).
During normal operation, the LED is continuously on (See Table 7
for error codes).
Airflow and Temperature Rise
The heating section for each size unit is designed and approved for
heating operation within the temperature--rise range stamped on the
unit rating plate.
Table 10, 11 and 12 show the approved temperature rise range for
each heating input, and the air delivery cfm at various temperature
rises for a given external static pressure. The heating operation
airflow must produce a temperature rise that falls within the
approved range. For single phase units only, “High” blower speed
is for high static cooling only and must not be used for gas heating
speed.
Refer to Indoor Airflow and Airflow Adjustments section to adjust
heating airflow when required.
Heating Sequence of Operation (Single Phase Models)
(See Fig. 14 and unit wiring label)
On a call for heating, terminal W of the thermostat is energized,
starting the induced-draft motor for a 5 second pre-purge. When
the pressure switch senses that the induced-draft motor is moving
sufficient combustion air, the burner sequence begins.
This
function is controlled by the integrated gas unit controller (IGC).
The indoor (evaporator) –fan motor is energized 30 seconds after
flame is established. When the thermostat is satisfied and W is
de-energized, the burners stop firing and the indoor (evaporator)
fan motor shuts off after a 90 second time-off delay. Please note
that the IGC has the capability to automatically reduce the indoor
fan motor on delay and increase the indoor fan motor off delay in
the event of high duct static and/or a partially-clogged filter.
Heating Sequence of Operation (3 Phase Models)
(See Fig. 15 and 16 and unit wiring label.)
On a call for heating, terminal W of the thermostat is energized,
starting the induced--draft motor. When the pressure switch senses
that the induced--draft motor is moving sufficient combustion air,
the burner sequence begins. This function is performed by the
integrated gas unit controller (IGC). The indoor (evaporator)--fan
motor is energized 45 sec after flame is established. When the
thermostat is satisfied and W is de--energized, the burners stop
firing and the indoor (evaporator) fan motor shuts off after a
45--sec time--off delay. Please note that the IGC has the capability
to automatically reduce the indoor fan motor on delay and increase
the indoor fan motor off delay in the event of high duct static
and/or partially--clogged filter.
Limit Switches
Normally closed limit switch (LS) completes the control circuit.
Should the leaving--air temperature rise above the maximum
allowable temperature, the limit switch opens and the control
circuit “breaks.” Any interruption in the control circuit instantly
closes the gas valve and stops gas flow to the burners. The blower
motor continues to run until LS resets.
When the air temperature at the limit switch drops to the
low--temperature setting of the limit switch, the switch closes and
completes the control circuit. The direct--spark ignition system
cycles and the unit returns to normal heating operation.
Table 7 – LED Indications
STATUS CODE
LED INDICATION
Normal Operation
2
On
No Power or Hardware Failure
Off
Check fuse, low voltage circuit
1 Flash
Limit Switch Fault
2 Flashes
Flame Sense Fault
3 Flashes
Four Consecutive Limit Switch Faults
4 Flashes
Ignition Lockout Fault
5 Flashes
Pressure Switch Fault
6 Flashes
Rollout Switch Fault
7 Flashes
Internal Control Fault
8 Flashes
Temporary 1 hr auto reset
1
9 Flashes
NOTES:
1.This code indicates an internal processor fault that will reset itself in one
hr. Fault can be caused by stray RF signals in the structure or nearby. This
is a UL requirement.
2. LED indicates acceptable operation. Do not change ignition control
board.
3. When W is energized the burners will remain on for a minimum of 60 sec.
4. If more than one error code exists they will be displayed on the LED in
sequence.
Rollout Switch
The function of the rollout switch is to close the main gas valve in
the event of flame rollout. The switch is located above the main
burners. When the temperature at the rollout switch reaches the
maximum allowable temperature, the control circuit trips, closing
the gas valve and stopping gas flow to the burners. The indoor
(evaporator) fan motor (IFM) and induced draft motor continue to
run until switch is reset. The IGC LED will display FAULT CODE
7.
Step 3 — Start--up Cooling and Make Adjust-
ments
Complete the required procedures given in the Pre--Start--Up
section before starting the unit. Do not jumper any safety devices
when operating the unit. Do not operate the compressor when the
outdoor temperature is below 40
F (4.4
C) (unless accessory
low--ambient kit is installed). Do not rapid--cycle the compressor.
Allow 5 minutes between on cycles to prevent compressor damage.
Checking Cooling Control Operation
Start and check the unit for proper cooling control operation as
follows:
1. Place room thermostat SYSTEM switch in OFF position.
Observe that blower motor starts when FAN switch is
placed in ON position and shuts down when FAN switch is
placed in AUTO position.
2. Place SYSTEM switch in COOL position and FAN switch
in AUTO position. Set cooling control below room
temperature. Observe that compressor, condenser fan, and
evaporator blower motors start. Observe that cooling cycle
shuts down when control setting is satisfied. The evaporator
fan will continue to run for 90 sec.
3. When using an auto--changeover room thermostat, place
both SYSTEM and FAN switches in AUTO positions.
Observe that unit operates in Heating mode when
temperature control is set to call for heating (above room
temperature) and operates in Cooling mode when
temperature control is set to call for cooling (below room
temperature).
IMPORTANT
: Three--phase, scroll compressors are direction
oriented. Unit must be checked to ensure proper compressor
3--phase power lead orientation. If not corrected within 5 minutes,
the internal protector will shut off the compressor. The 3--phase
power leads to the unit must be reversed to correct rotation. When
turning backwards, the difference between compressor suction and
discharge pressures will be minimal.
PY4G
Summary of Contents for PY4G B Series
Page 4: ...4 A190121 Fig 3 24 36 Unit Dimensions PY4G ...
Page 5: ...5 A190122 Fig 4 42 60 Unit Dimensions PY4G ...
Page 16: ...16 A150502 Fig 14 208 230 1 60 Connection Wiring Diagram PY4G ...
Page 17: ...17 A150510 Fig 14 Cont 208 230 1 60 Ladder Wiring Diagram PY4G ...
Page 18: ...18 A150508 Fig 15 208 230 3 60 Connection Wiring Diagram PY4G ...
Page 19: ...19 A150511 Fig 15 Cont 208 230 3 60 Ladder Wiring Diagram PY4G ...
Page 20: ...20 A150509 Fig 16 460 3 60 Connection Wiring Diagram PY4G ...
Page 21: ...21 A150512 Fig 16 Cont 460 3 60 Ladder Wiring Diagram PY4G ...