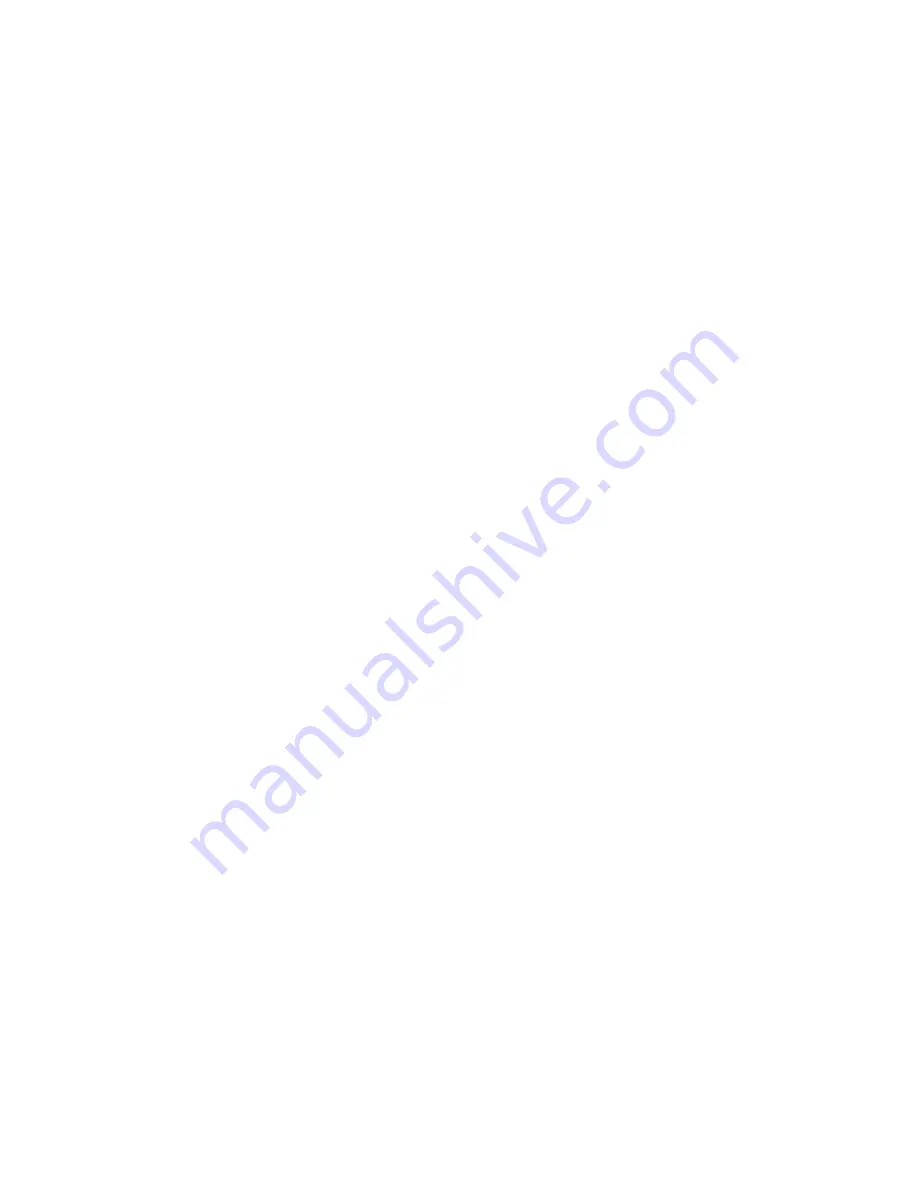
18
Compressor Rotation —
To determine whether or not
compressor is rotating in the proper direction:
1. Connect service gages to suction and discharge pressure
fittings.
2. Energize the compressor.
3. The suction pressure should drop and the discharge pres-
sure should rise, as is normal on any start-up.
4. If the suction pressure does not drop and the discharge
pressure does not rise to normal levels, the compressor
may be rotating in the wrong direction.
5. Since the compressor and fan motors are connected in
phase during production, it is likely that the evaporator
and condenser fans are probably also rotating in the
wrong direction.
6. Turn off power to the unit, lock and tag disconnect per
standard safety procedures.
7. Reverse any two of the unit power leads.
8. Remove lock and tag per standard safety procedures and
reapply power to the unit.
9. The suction and discharge pressure levels should now
move to their normal start-up levels.
NOTE: When the compressor is rotating in the wrong direc-
tion, the unit makes an elevated level of noise and does not
provide cooling.
Operating Sequence —
All units require the addition
of a thermostat accessory package to complete the control cir-
cuit. The sequence of operation may vary depending on which
package is selected.
ROOM-MOUNTED THERMOSTAT — These units use an
electronic thermostat mounted in the conditioned space.
FAN CIRCULATION — The indoor-fan motor is energized
through G on the thermostat and the indoor-fan contactor is
energized. This starts the indoor-fan motor (IFM). The fan will
operate to provide continuous air circulation.
COOLING — The indoor fan will operate continuously or
when the compressor runs, depending on the setting of the ther-
mostat fan selector switch. When the thermostat closes (on a
call for cooling Y1 on the thermostat), the control relay (CR),
outdoor-fan contactor (OFC) and compressor contactor(s) (C1
and C2 on 50XCR12-16 units) close. The control relay will
start the indoor fan if it is not already running. The compressor
contactors will immediately start the first stage compressor(s).
A second stage on 50XCR12-16 units will close if addition-
al cooling demand is required, and will then start the second-
stage compressor. When the thermostat is satisfied, the second
stage compressor will stop first, and then the first stage com-
pressors will stop when cooling demand is satisfied.
ALL UNITS — The control circuit incorporates a current
sensing lockout relay (Cycle-LOC™ device) that locks off the
compressor(s) for 5 minutes when any safety device is activat-
ed (low or high pressure switches, or compressor internal over-
load). If any compressor safety device opens, the compressor
will stop. High and low-pressure switches and compressor mo-
tor overload protectors will reset automatically when the condi-
tion which caused the device to trip has dropped below the re-
set condition. To reset the Cycle-LOC control device, manually
turn the control power OFF, then back ON.
SERVICE
Cleaning Evaporator Coil —
Do not use high-pressure
water or air. Damage to fins may result. Clean coils with a vac-
uum cleaner, fresh water, compressed air, or a bristle brush (not
wire). Backflush coil to remove debris. Commercial coil clean-
ers may also be used to help remove grease and dirt. Steam
cleaning is NOT recommended.
Units installed in corrosive environments should be cleaned
as part of a planned maintenance schedule. In this type of appli-
cation, all accumulations of dirt should be cleaned off the coil.
Take care not to get water in the system ducts or unit
insulation.
Lubrication —
Fan motors have permanently lubricated
bearings.
Indoor Fan Adjustment —
To prevent personal injury,
be sure wire fan guards (provided by customer) are secured in
place over each fan discharge (or that fans are ducted) before
starting the unit.
TO CHANGE FAN SPEED
1. Shut off unit power supply. Lock out power supply and
tag disconnect locations.
2. Loosen fan belt by loosening fan motor belt adjusting
bolts. Do not loosen fan motor mounting bracket from
unit.
3. Loosen movable pulley flange setscrew (Fig. 11).
4. Screw movable flange toward fixed flange to increase fan
speed and away from fixed flange to decrease speed. In-
creasing fan speed increases load on motor. Do not ex-
ceed maximum allowable fan speed or motor full load
amps indicated on unit nameplate and in Table 5.
5. Set movable flange setscrew at nearest flat of pulley hub
and tighten setscrew.
6. Check pulley alignment and belt tension adjustment as
described below.
7. Check fan operation. Repeat above procedure as required.
Pulley Alignment —
Shut off unit power supply. Lock
out power supply and tag disconnect locations. Loosen fan
motor pulley setscrews and slide fan pulley along fan shaft.
Make angular alignment by loosening motor from mounting
bracket (see Fig. 11). Check alignment with a straightedge.
Belt Tension Adjustment —
Shut off unit power sup-
ply. Lock out power supply and tag disconnect locations. Loos-
en fan motor mounting plate bolts. Do not loosen motor
mounting bracket from unit. Adjust belt tensioning bolt until
proper belt tension is obtained.
Changing Fan Wheel —
If a fan wheel should fail, it
may be replaced as follows:
1. Shut off unit power supply. Lock out power supply and
tag disconnect locations.
2. Remove belts from fan pulley.
3. Loosen locking collars on the fan bearings and set screws
on the fan wheels.
4. Remove the shaft through the access panel on either side
of the unit.
5. Remove the fan cut-off plate in the fan discharge.
6. Remove the fan wheel through the fan discharge opening.
7. Replace the wheel, and reverse Steps 1-5 above.
Fan Bearing Replacement —
If a fan bearing fails,
replace it as follows:
1. Shut off unit power supply. Lock out power supply and
tag disconnect locations.
2. Remove belts from the fan pulley.
3. Support fan shaft.
4. Loosen locking collar on fan bearing.
5. Remove bearing from the shaft.
6. Install new bearing onto the shaft, and reverse Steps 1-3
above.