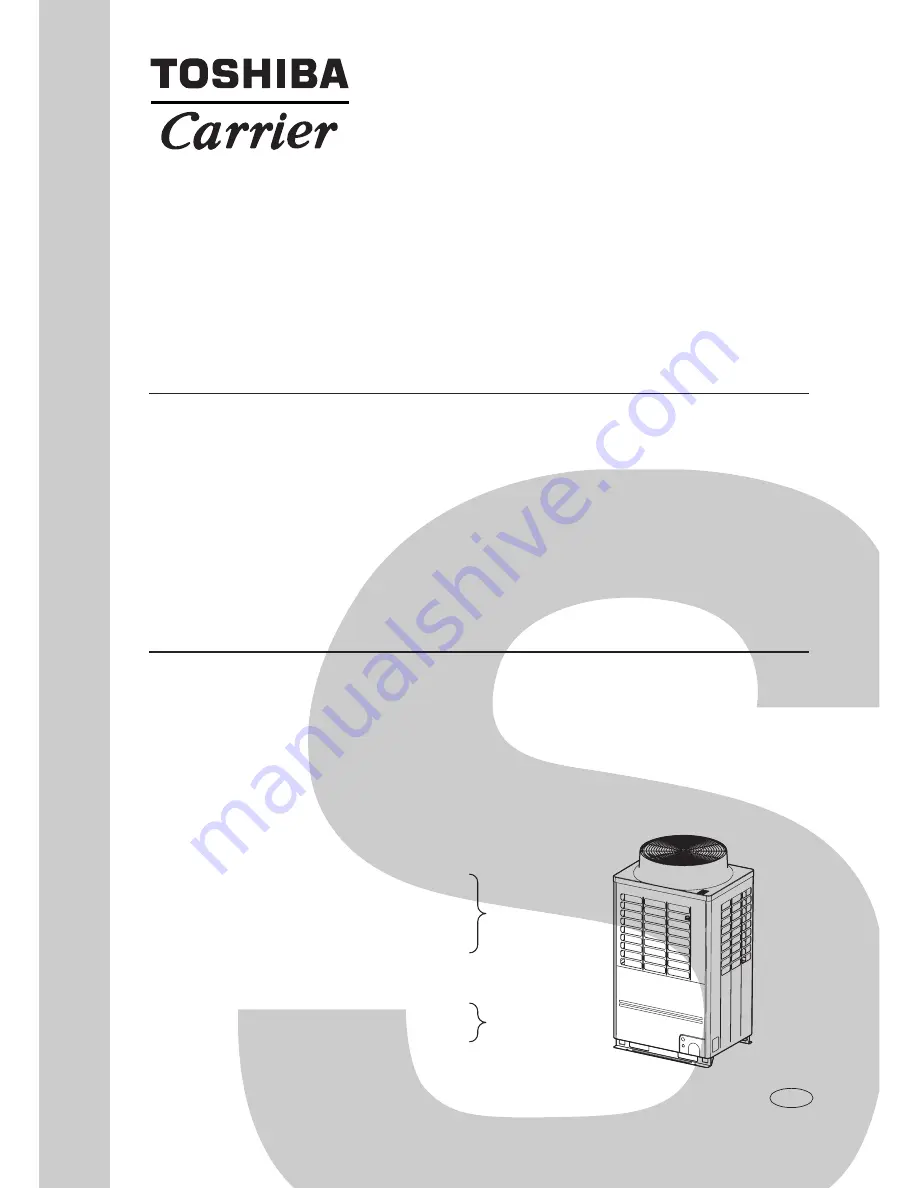
AIR CONDITIONER (MULTI TYPE)
SERVICE MANUAL
Outdoor Unit
< SUPER HEAT RECOVERY MULTI-i >
Model name:
MMY-MAP0724FT9UL
MMY-MAP0964FT9UL
MMY-MAP1204FT9UL
MMY-MAP0724FT6UL
MMY-MAP0964FT6UL
MMY-MAP1204FT6UL
Flow Selector Unit (FS unit)
Model name:
RBM-Y0383FUL
RBM-Y0613FUL
RBM-Y0963FUL
This service manual provides relevant explanations about new outdoor unit (SHRM-i).
Please refer to the following service manuals for each indoor units.
PRINTED IN JAPAN, Jun, 2013, TOMO
FILE No. A13-002
<4-Way Cassette Type> ........................
<Compact 4-Way Cassette Type> ........
<Ceiling Type> .......................................
<High Wall Type> ...................................
<Medium Static Ducted Type> ..................
<Slim Ducted Type> ..............................
<High Static Ducted Type> ...................
A10-019
A11-011
A11-020
Revision 1 : Jun., 2013
Revision 2 : Jul., 2013
Revision 3 : Dec., 2013
Revision 4 : Sep., 2014
Summary of Contents for MMY-MAP0724FT6UL
Page 35: ...35 3 5 Parts Layout in Outdoor Unit 072 type Model MMY MAP0724FT...
Page 36: ...36 096 120 type Model MMY MAP0964FT MAP1204FT...
Page 37: ...37 3 6 Parts Layout in Inverter Assembly 208 230V model MMY MAP0724FT9UL...
Page 38: ...38 208 230V model MMY MAP0964FT9UL MMY MAP1204FT9UL...
Page 39: ...39 460V model MMY MAP0724FT6UL...
Page 40: ...40 460V model MMY MAP0964FT6UL MMY MAP1204FT6UL...
Page 41: ...41 3 7 Outdoor Inverter print circuit board 3 7 1 Interface P C board MCC 1606...
Page 42: ...42 3 7 2 Inverter P C board for compressor MCC 1595 A3 IPDU For 208 230V model MMY MAP 4FT9UL...
Page 43: ...43 3 7 3 Inverter P C board for compressor MCC 1596 A3 IPDU For 460V model MMY MAP 4FT6UL...
Page 44: ...44 3 7 4 Inverter P C board for fan motor MCC 1610 FAN IPDU...
Page 45: ...45 3 7 5 Noise Filter P C board MCC 1608 A B For 208 230V model MMY MAP 4FT9UL...
Page 46: ...46 3 7 6 Noise Filter P C board MCC 1625 A B C For 460V model MMY MAP 4FT6UL...
Page 195: ...195...
Page 197: ...197...
Page 257: ...257 15 EXPLODED DIAGRAM PARTS LIST Outdoor unit 15 1 MMY MAP0724FT9UL...
Page 258: ...258 15 1 MMY MAP0724FT9UL...
Page 262: ...262 15 1 Inverter Assembly MMY MAP0724FT9UL...
Page 264: ...264 15 2 MMY MAP0964FT9UL MMY MAP1204FT9UL...
Page 265: ...265 15 2 MMY MAP0964FT9UL MMY MAP1204FT9UL...
Page 269: ...269 15 2 Inverter Assembly MMY MAP0964FT9UL MMY MAP1204FT9UL...
Page 271: ...271 15 3 MMY MAP0724FT6UL...
Page 272: ...272 15 3 MMY MAP0724FT6UL...
Page 276: ...276 15 3 Inverter Assembly MMY MAP0724FT6UL...
Page 278: ...278 15 4 MMY MAP0964FT6UL MMY MAP1204FT6UL...
Page 279: ...279 15 4 MMY MAP0964FT6UL MMY MAP1204FT6UL...
Page 283: ...283 15 4 Inverter Assembly MMY MAP0964FT6UL MMY MAP1204FT6UL...