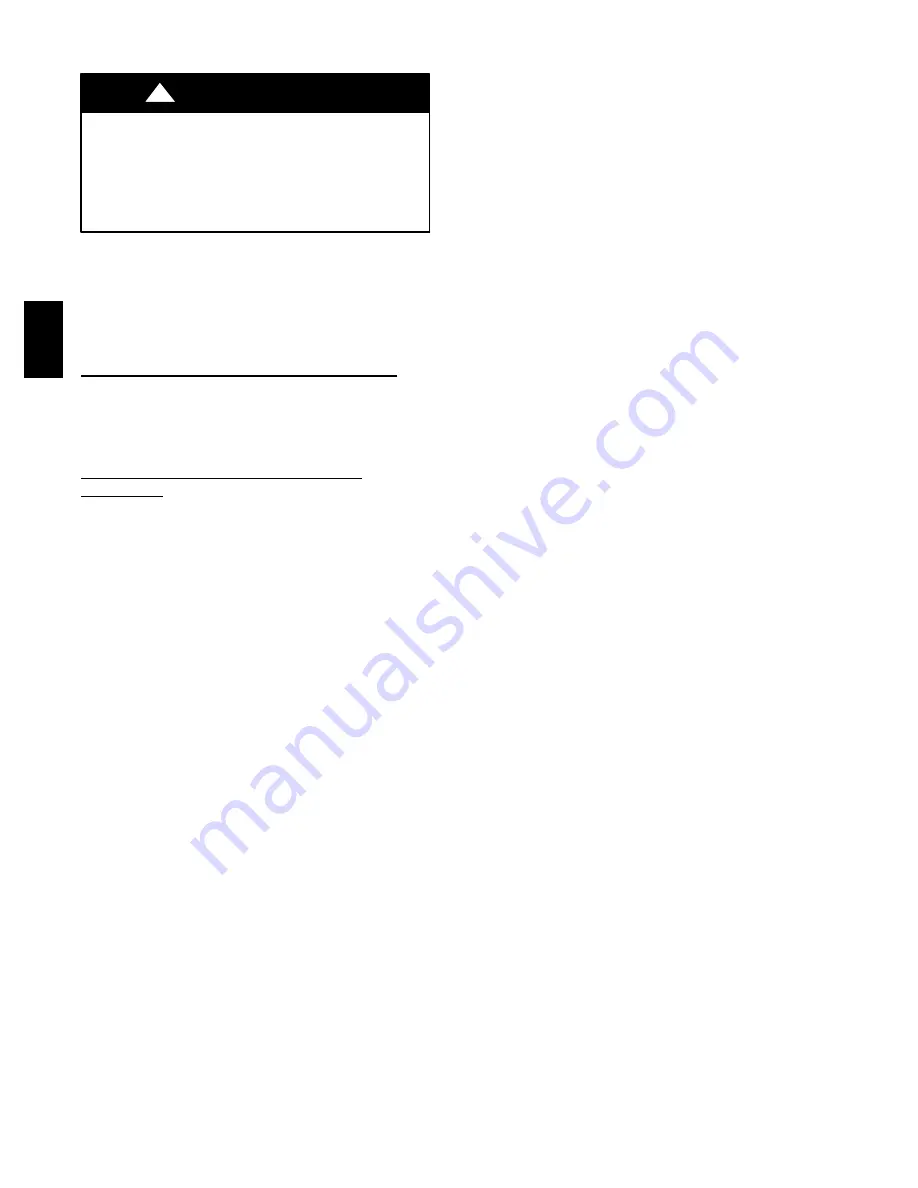
8
and pressure tubes are connected as shown in Fig. 7.
See
appropriate application instructions for these procedures.
PROPERTY DAMAGE HAZARD
Failure to follow this caution may result in property
damage.
Local codes may require a drain pan under entire furnace
and condensate trap when a condensing furnace is used in
an attic application or over a finished ceiling.
CAUTION
!
NOTE
: In Canada, installations shall be in accordance with
current CAN/CSA--B149.1--05 and/or local codes.
UPFLOW APPLICATION
An upflow furnace application is where furnace blower is located
below combustion and controls section of furnace, and conditioned
air is discharged upwards.
Condensate Trap (Factory--Shipped Orientation)
The condensate trap is factory installed in the blower shelf and
factory connected for UPFLOW applications. A factory--supplied
tube is used to extend the condensate trap drain connection to the
desired furnace side for field drain attachment. See Condensate
Trap Tubing section for drain tube extension details. (See Fig. 6.)
Condensate Trap Tubing (Factory--Shipped
Orientation)
NOTE
: See Fig. 7 or tube routing label on main furnace door to
confirm location of these tubes.
1. Collector Box Drain, Inducer Housing Drain, Relief Port,
and Pressure Switch Tubes.
These tubes should be factory attached to condensate trap
and pressure switch ready for use in UPFLOW applications.
These tubes can be identified by their connection location
and also by a color label on each tube. These tubes are
identified as follows: collector box drain tube (blue label),
inducer housing drain tube (violet label or molded), relief
port tube (green label), and pressure switch tube (pink
label).
2. Condensate Trap Drain Tube
The condensate trap drain connection must be extended for
field attachment by doing the following:
f. Determine location of field drain connection. (See Fig. 2
or 7.)
NOTE
: If internal filter or side filter/media cabinet is used, drain
tube should be located to opposite side of casing from return duct
attachment to assist in filter removal.
g. Remove and discard casing drain hole plug button from
desired side.
h. Install drain tube coupling grommet (factory--supplied
in loose parts bag) in selected casing hole.
i. Slide drain tube coupling (factory--supplied in loose
parts bag) through grommet so long end of coupling
faces blower.
j. Cement 2 factory--supplied 1/2--in. (13 mm) street
CPVC elbows to rigid drain tube connection on
condensate trap. (See Fig. 7.) These elbows must be
cemented together and cemented to condensate trap
drain connection.
58MV
C