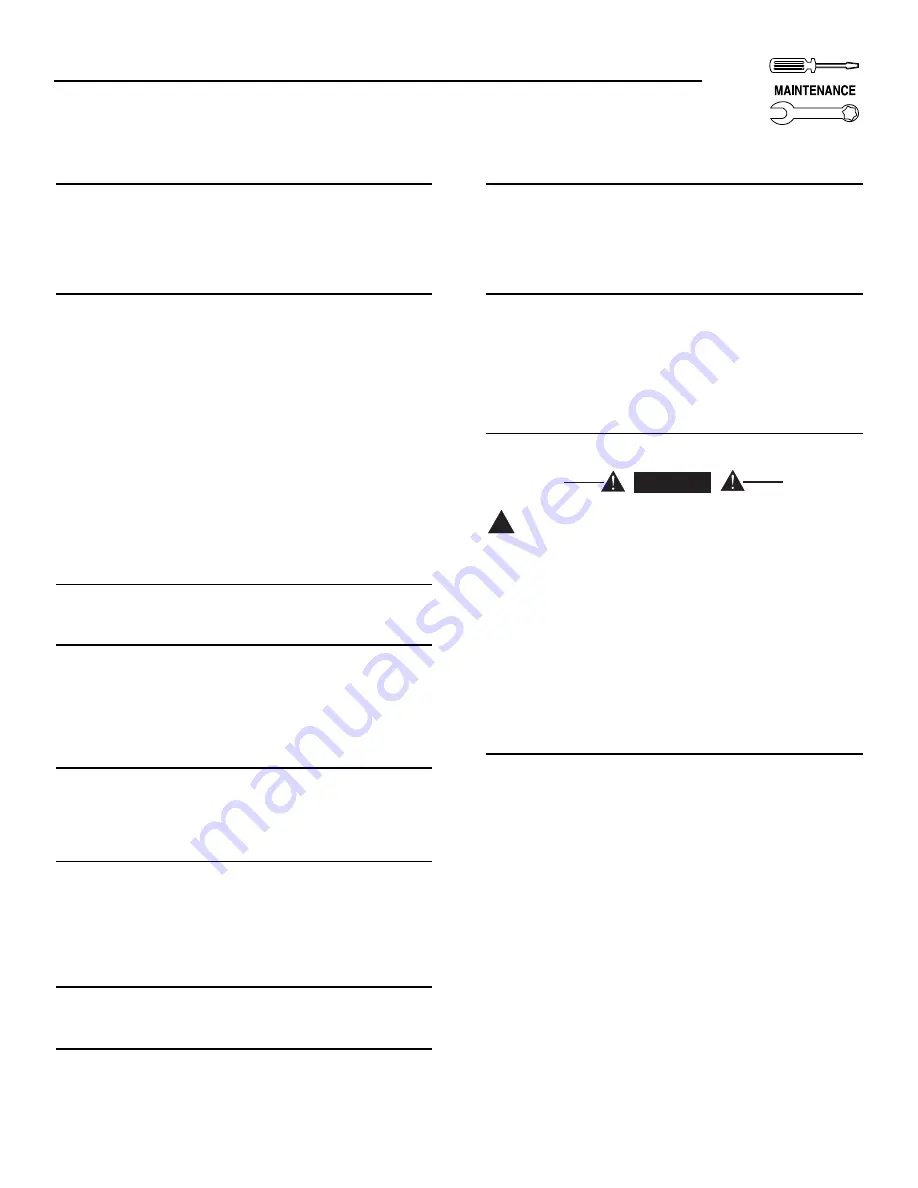
Carrier
15
4.4.2 BATTERY FLUID
Check battery electrolyte fluid at least once a month.
Fluid should cover separators in all battery cells. If
fluid level is low, add distilled water to cover tops of
separators. DO NOT USE TAP WATER IN BATTERY.
4.4.3 ENGINE COOLANT
Check coolant level in coolant recovery bottle. See
Specifications, Section 1.10.
• Add recommended coolant mixture as necessary.
• Periodically remove radiator pressure cap to make
sure the coolant recovery system is functioning
properly. Coolant should be at bottom of radiator
filler neck. If coolant level is low, inspect gasket in
radiator pressure cap. Replace cap, if necessary.
To have pressure cap tested, contact a dealer.
Inspect cooling system and coolant recovery sys-
tem for leaks.
4.5
MAINTENANCE OWNER/
OPERATOR CAN PERFORM
4.5.1 CHECK ENGINE OIL LEVEL
Refer to “Checking Fluid Levels” in Section 4.4.
4.5.2 CHECK BATTERY
• Check battery fluid level each week as outlined
under “Check Fluid Levels”.
• Check battery cables for condition, tightness, cor-
rosion or damage. Clean, tighten or replace as
necessary.
4.5.3 EXERCISE SYSTEM
Start the generator engine at least once every seven
days and let it run at least 20 minutes. See Section
3.5, “Weekly Exercise Cycle”.
4.5.4 INSPECT COOLING SYSTEM
• Inspect engine cooling system at least once each
month.
• Check hoses for damage, deterioration, leaks, etc.
Correct any discrepancies found.
• Check hose clamps for tightness.
4.5.5 CHECK ENGINE COOLANT LEVEL
See “Checking Fluid Levels” in Section 4.4.
4.5.6 PERFORM VISUAL INSPECTION
Complete a thorough visual inspection of the entire
engine-generator monthly. Look for obvious damage,
loose, missing or corroded nuts, bolts and other fas-
teners. Look for fuel, oil or coolant leaks.
4.5.7 INSPECT EXHAUST SYSTEM
Inspect the exhaust system at least once every three
months. Check all exhaust system pipes, mufflers,
clamps, etc. for condition, tightness, leaks, security,
damage.
4.5.8 CHECK FAN BELT
• Inspect fan belts every three months. Replace any
damaged, deteriorated, worn or otherwise defec-
tive belt.
• Check fan belt tension. Thumb pressure, exerted
midway between pulleys, should deflect about 3/8
to 3/4 inch. Adjust belt tension as required.
4.5.9 INSPECT ENGINE GOVERNOR
Visually inspect electronic governor.
Do not attempt to adjust the governor. Only
qualified service facilities should adjust the
governor. Excessively high operating speeds are
dangerous and increase the risk of personal
injury. Low speeds impose a heavy load on the
engine when adequate engine power is not
available and may shorten engine life. Correct
rated frequency and voltage are supplied only
at the proper governed speed. Some connected
electrical load devices may be damaged by
incorrect frequency and/or voltage. Only quali-
fied service technicians should adjust the gov-
erned speed.
4.5.10 CHANGING ENGINE OIL
Refer to maintenance performed by authorized service
facilities for engine oil and filter change frequencies.
Drain the oil while the engine is still warm from run-
ning. This means warm up the engine, shut it down
and drain immediately as follows:
1. Remove OIL DRAIN HOSE from its retaining clip.
2. Loosen and remove OIL DRAIN HOSE CAP.
Drain oil completely into suitable container.
3. When all oil has drained, install and tighten OIL
DRAIN HOSE CAP, and re-install into its retaining
clip.
4. Turn OIL FILTER (Figure 4.2) counterclockwise
and remove. Dispose of old filter.
5. Apply light coating of new engine oil to seal of new
oil filter. Install FILTER and tighten by hand only.
DO NOT OVERTIGHTEN.
6. Remove OIL FILL CAP. Add recommended oil (see
SPECIFICATIONS). DO NOT FILL ABOVE THE
DIPSTICK “FULL” MARK. Crankcase oil capacity
is 4.0 U.S. quarts (3.8 liters).
!
DANGER
Section 4 — Maintenance
Carrier Liquid-cooled 15 kW Generators