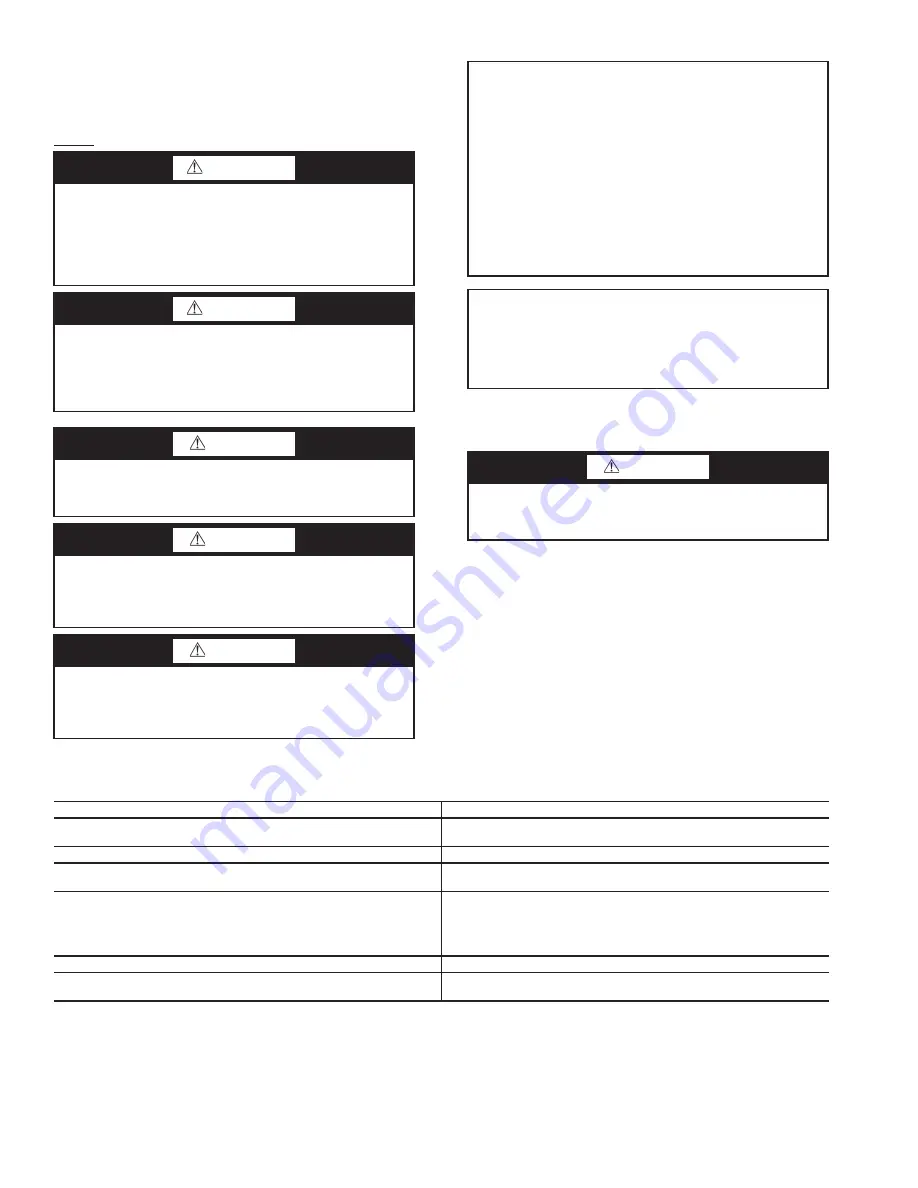
32
• LOW suction pressure and frosting of the valve and/or
equalizer line may indicate a failed valve. However,
these symptoms may also indicate an undercharge of
refrigerant. Calculate the subcooling and superheat to
verify a failed valve or refrigerant charge issue.
Repair
See Table 14 for suggestions of good practices regarding
regular repairs. See Table 15 for additional troubleshooting
information.
Moisture Check —
To perform moisture check:
• Check that connectors are orientated “down” (or as rec-
ommended by equipment manufacturer).
• Arrange harnesses with “drip loop” under motor.
• Check if condensate drain is plugged.
• Check for low airflow (too much latent capacity).
• Check for undercharged condition.
• Check and plug leaks in return ducts, cabinet.
Table 14 — Good Practices
WARNING
Puron
®
refrigerant (R-410A) operates at higher pressure
than R-22, which is found in other WSHPs. Tools such as
manifold gages must be rated to withstand the higher pres-
sures. Failure to use approved tools may result in a failure
of tools, which can lead to severe damage to the unit, injury
or death.
WARNING
Most TXVs are designed for a fixed superheat setting and
are therefore considered non-adjustable. Removal of the
bottom cap will not provide access for adjustment and can
lead to damage to the valve or equipment, unintended vent-
ing of refrigerant, personal injury, or possibly death.
CAUTION
Always recover the refrigerant from the system with suit-
able approved tools, recovery equipment, and practices
prior to attempting to remove or repair any TXV.
CAUTION
Use caution when tightening the strap. The strap must be
tight enough to hold the bulb securely but caution must be
taken not to over-tighten the strap, which could dent, bend,
collapse or otherwise damage the bulb.
CAUTION
Puron
®
refrigerant (R-410A) requires the use of synthetic
lubricant (POE oil). Do not use common tools on systems
that contain R-22 refrigerants or mineral oil. Contamina-
tion and failure of this equipment may result.
IMPORTANT: Due to the hygroscopic nature of the
POE oil in Puron refrigerant (R-410A) and other envi-
ronmentally sound refrigerants, any component replace-
ment must be conducted in a timely manner using
caution and proper service procedure for these types of
refrigerants. A complete installation instruction will be
included with each replacement TXV/filter drier assem-
bly. It is of critical importance these instructions are
carefully understood and followed. Failure to follow
these instructions can result in a system that is contami-
nated with moisture to the extent that several filter drier
replacements may be required to properly dry the
system.
IMPORTANT: Repair of any sealed refrigerant system
requires training in the use of refrigeration tools and proce-
dures. Repair should only be attempted by a qualified ser-
vice technician. A universal refrigerant handling certificate
will be required. Local and/or state license or certificate
may also be required.
CAUTION
Disconnect power from unit before removing or replacing
connectors, or servicing motor. Wait 5 minutes after dis-
connecting power before opening motor.
DO
DO NOT
Check motor, controls wiring, and connections thoroughly before replac-
ing motor.
Automatically assume the motor is bad.
Orient connectors down so water cannot get in. Install “drip loops.”
Locate connectors above 7 and 4 o’clock positions.
Use authorized motor and control model numbers for replacement.
Replace one motor or control model number with another (unless
replacement is authorized).
Keep static pressure to a minimum by:
•
Using high efficiency, low-static filters.
•
Keeping filters clean.
•
Designing ductwork for minimum static and maximum comfort.
•
Improving ductwork when replacement is necessary.
Use high pressure drop filters.
Use restricted returns.
Size equipment wisely.
Oversize system then compensate with low airflow.
Check orientation before inserting motor connectors.
Plug in power connector backwards.
Force plugs.