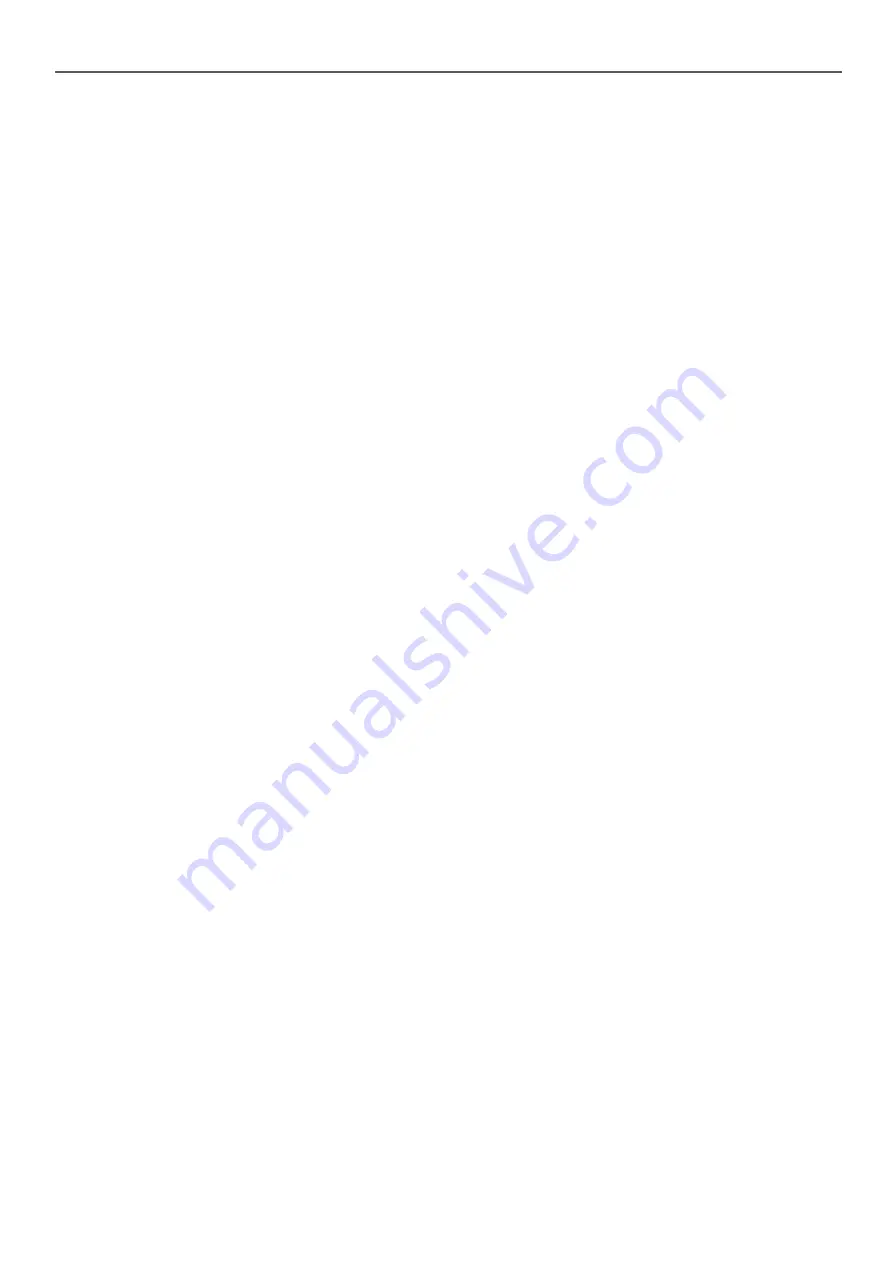
57
13 - STANDARD MAINTENANCE
Air conditioning equipment must be maintained by profes-sional
technicians, whilst routine checks can be carried out locally by
specialised technicians. See the standard EN 378-4.
IMPORTANT : Before performing any work on the machine
ensure it is de-energised. If a refrigerant circuit is opened, it
must be evacuated, recharged and tested for leaks. Before
any operation on the refirgerant circuit, it is necessary to
remove the complete refrigerant charge from the unit with a
refrigerant charge transfer unit.
Simple preventive maintenance will allow you to get the best
performance from your HVAC unit:
-
Improved cooling performance
-
Reduced power consumption
-
Prevention of accidental component failure
-
Prevention of major time-consuming and costly inter-ventions
-
Protection of the environment.
There are five maintenance levels for HVAC units, as defined by
the AFNOR X60-010 standard.
13.1 - Level 1 maintenance
See note “Any deviation or non-observation ...” in chapter 13.3 -
“Level 3 (or higher) maintenance”. Simple procedure can be carried
out by the user:
-
Visual inspection for oil traces (sign of a refrigerant leak)
-
Air heat exchanger (condenser) cleaning - see chapter 13.6.1
- “Level 1”.
-
Check for removed protection devices, and badly closed
doors/covers
-
Check the unit alarm report when the unit does not work.
Refer to the SmartVu
TM
control manual for a more detailed
explanation.
-
Check the clogging state of filters of aeration openings of the
control box.
-
Check proper operation of the cooling fans of the control box
-
Verify the temperature difference at the heat exchanger inlet
and outlet is correct,
-
Verify the refrigerant charge in the liquid line sight glass,
-
Check the anti-corrosion coatings.
General visual inspection for any signs of deterioration.
A regular cleaning shall be carried out inside the unit and in the
ATEX zone in order to remove any flammable materials (leaves,
branches, cartons...).
13.2 - Level 2 maintenance
See note “Any deviation or non-observation ...” in the next column.
This level requires specific know-how in the electrical, hydraulic
and mechanical fields. It is possible that these skills are available
locally: Existence of a maintenance service, industrial site,
specialised subcontractor. In these cases, the following
maintenance operations are recommended.
Carry out all level 1 operations, then:
■
Electrical :
-
At least once a year tighten the power circuit electrical
connections (see table 13.4).
-
Check and re-tighten all control/command connections, if
required (see table 13.4).
-
Check the differential switches for correct operation every 6
months.
-
Remove the dust and clean the interior of the control boxes,
if required.
-
Once a year, replace the filter of electrical boxes, especially
in dusty environment.
-
Check the presence and the condition of the electrical
protection devices.
-
Check the correct operation of all heaters.
-
Replace the control box cooling fans used with option 22
(with designation EF22_) every five years.
-
Check the height of the anti-vibration mountings (located
between the compressor rails and the unit chassis) after 5 years
of operation, and then each year. When the total minimum height
of the mountings is less than 25 mm replace the mountings.
-
Check the water connections.
-
Purge the water circuit.
-
Clean the water filter.
-
Fully clean the condensers with a low-pressure jet and a
bio-degradable cleaner (counter-current cleaning - see
chapter 13.6.2 - “Level 2”).
-
Replace the stuffing box packing of the pump after 10000
hours of operation.
-
Check the unit operating parameters and compare them with
previous values.
-
Keep and maintain a maintenance sheet, attached to each
HVAC unit.
-
Units with option/QM231: proceed with the check list for the
verification of the capacitors.
■
Hydraulics:
-
When working on the hydraulic circuit, take care not to
damage the adjacent air heat exchanger,
-
Check the condition of the expansion tank (presence of
corrosion or loss of gas pressure) and replace it if required
(option 293),
-
Check the operation of the flow switch,
-
Check the condition of pipe thermal insulation,
-
Check the concentration of the anti-freeze protection solution
(ethylene glycol or propylene glycol),
-
Check the water flow via the heat exhanger pressure
difference (option 116),
-
Check the condition of the heat-transfer fluid or the water
quality,
-
Check for the corrosion of the steel pipe work.
■
Refrigerant circuit :
-
Check the unit operating parameters and compare them with
the previous values,
-
Check the operation of the high-pressure switches. Replace
them if there is a fault,
-
Check the fouling of the filter drier. Replace it if necessary,
-
Keep an up-to-date service booklet specific to the refrigeration
unit in question.
■
Mechanical :
-
Check that the mounting bolts for the ventilation sub-
assemblies, fans, compressors and electrics box are securely
tightened.
All these operations require strict observation of adequate safety
measures: Individual protection garments, compliance with all
industry regulations, compliance with applicable local regulations
and using common sense.
13.3 - Level 3 (or higher) maintenance
NOTE: Any deviation or non-observation of these maintenance
criteria will render the guarantee conditions for the HVAC unit
null and void, and the manufacturer, Carrier SCS will no longer
be held responsible.
The maintenance at this level requires specific skills/approval/
tools and know-how and only the manufacturer, his representative
or authorised agent are permitted to carry out these operations.
These maintenance operations concern for example:
-
A major component replacement (compressor, evapo-rator)
-
Any intervention on the refrigerant circuit (handling refrigerant)
-
Changing of parameters set at the factory (application
change)
-
Removal or dismantling of the HVAC unit
-
Any intervention due to a missed established mainte nance
operation
-
Any intervention covered by the warranty.
To reduce waste, the refrigerant and the oil must be transferred
in accordance with applicable regulations, using methods that limit
refrigerant leaks and with materials that are suitable for the
products.