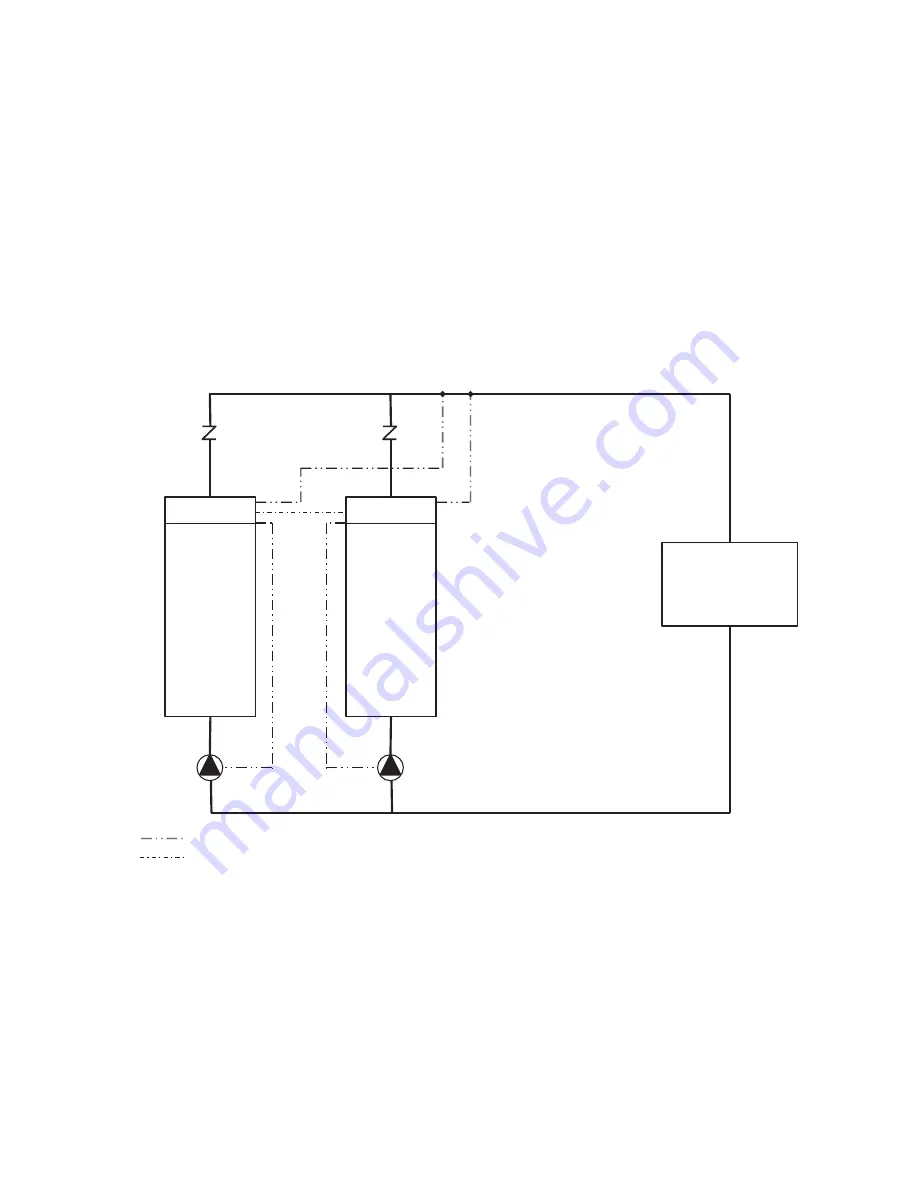
35
DUAL CHILLER PUMP CONTROL FOR PARALLEL
CHILLER APPLICATIONS
Parallel chiller control with dedicated pumps is recommended.
The chiller must start and stop its own water pump located in
its own piping. If pumps are not dedicated for each chiller’s
piping, chiller isolation valves are required; each chiller must
open and close its own isolation valve through the control. Fig-
ures 32-35 show typical pump arrangements for dual chiller
parallel applications.
Although not recommended, it is possible to configure the sys-
tem with no individual pump control. In applications where the
unit is configured for fresh water (
Main Menu
Configura-
tion Menu
Service Parameters, Evaporator Fluid Type=1
[Fresh Water]
), and Set Point temperature is close to the lower
limit of the fresh water range, it is possible for changeable
leaving water conditions as the chilled water flow rate drops to
an operating unit, causing the leaving chilled water tempera-
ture to drop and initiate the evaporator freeze protection over-
ride. Constant flow applications may alleviate this issue.
In constant water flow applications, the master chiller should
be the primary control source for the chilled water pump. The
slave chiller should have override capability. In the event of a
communication failure between the master and slave chillers,
the slave chiller will operate as a stand-alone machine and
therefore must be able to enable the chilled water pump.
DUAL CHILLER CONTROL FOR SERIES CHILLER
APPLICATIONS
When chillers are configured to work in series mode no addi-
tional chilled water supply sensor is required. The master
chiller will be installed downstream of the slave chiller (the
slave chiller outlet fluid is the master inlet fluid). If pump con-
trol is required, it will be controlled by the master chiller.
To configure the master chiller for series applications, see Ta-
ble 28. To configure the slave chiller for series applications,
see Table 29.
Fig. 32 — Typical Parallel Master/Slave Chillers
Dedicated Primary Pumping, Variable Flow, Leaving Water Control
CONTROL BOX
SLAVE
CHILLER
CONTROL BOX
MASTER
CHILLER
LOAD
CHECK VALVES
CHWS TEMP SENSORS
FIELD WIRING
FIELD COMMUNICATION WIRING
SLAVE
PUMP
MASTER
PUMP
NOTE: This is a simplified piping diagram.
Not all hydronic specialties are shown.
Summary of Contents for AquaForce 30XV140
Page 79: ...79 Fig 76 VFD Communication Wiring Compressor A B Fan VFD A1 A2 B1 B2...
Page 228: ...228 Fig 90 30XV Typical Field Wiring Schematic cont...
Page 229: ...229 Fig 91 30XV Standard Tier 140 275 All Voltages Power Schematic NOTE See Legend on page 226...
Page 230: ...230 Fig 92 30XV Standard Tier 300 325 All Voltages Power Schematic NOTE See Legend on page 226...
Page 240: ...240 Fig 99 30XV Communication Wiring...
Page 241: ...241 Fig 100 30XV 115V Control Wiring All Tonnages All Voltages...
Page 242: ...242 Fig 101 30XV 24V Control Wiring 30XV140 325 All Voltages...
Page 243: ...243 Fig 101 30XV 24V Control Wiring 30XV140 325 All Voltages cont...
Page 244: ...244 Fig 102 30XV 24V Control Wiring 30XV350 500 All Voltages...
Page 245: ...245 Fig 102 30XV 24V Control Wiring 30XV350 500 All Voltages cont...
Page 246: ...246 Fig 103 Component Arrangement Diagram for 30XV140 325...
Page 247: ...247 Fig 103 Component Arrangement Diagram for 30XV140 325 cont...
Page 248: ...248 Fig 104 Component Arrangement Diagram for 30XV350 500...
Page 337: ...337 APPENDIX J FACTORY SUPPLIED PUMPS cont Fig L System Information...
Page 338: ...338 APPENDIX J FACTORY SUPPLIED PUMPS cont Fig M Unit and Language Settings...
Page 341: ...341 APPENDIX J FACTORY SUPPLIED PUMPS cont Fig P Data Input 2...
Page 342: ...342 APPENDIX J FACTORY SUPPLIED PUMPS cont Fig Q Data Input 3...
Page 347: ...347 APPENDIX J FACTORY SUPPLIED PUMPS cont Fig U Pump Wiring Diagram...