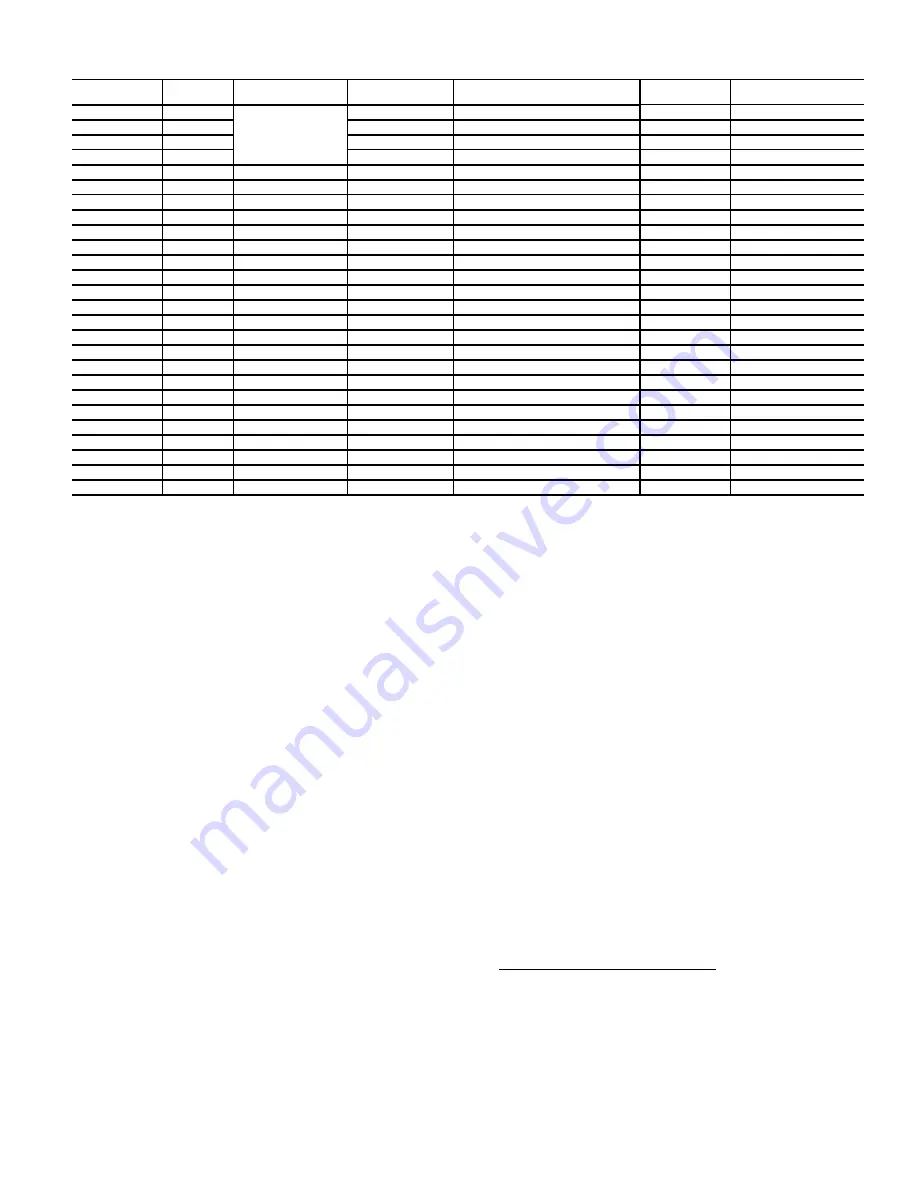
19
Table 12 — EMM Board Inputs and Outputs
Local Equipment Network
Information is transmitted between modules via a 3-wire com-
munication bus or LEN.
Board Addresses
All boards (except the Carrier Controller display and the Energy
Management Module) have DIP switches to set the address.
Control Module Communication
RED LED
Proper operation of the control boards can be visually checked
by looking at the red status LEDs (Light-Emitting Diodes).
When operating correctly, the red status LEDs will blink in
unison at a rate of once every 2 seconds. If the red LEDs are
not blinking in unison, verify that correct power is being sup-
plied to all modules and that all communication wiring is con-
nected securely. Confirm current version of software installed
on SmartView panel by navigating to Control Identification
Menu (
Main Menu
Configuration Menu
HMI Config-
uration Menu
Control Identification Menu
Software
Part Number
). If a newer version of the software exists, con-
tact your Carrier service representative service to reload current
software. If the problem still persists, replace the Carrier Con-
troller module. A red LED that is lit continuously or blinking at
a rate of once per second or faster indicates that the board
should be replaced.
GREEN LED
All boards have a green LEN LED which should be blinking
whenever power is on. If the LEDs are not blinking as de-
scribed check LEN connections for potential communication
errors at the board connectors. A 3-wire bus accomplishes
communication between modules. These 3 wires run in parallel
from module to module. They connect to J9 on EMM and
AUX boards, and to J12 or J13 on SIOBs. A valid unit config-
uration must be in the Carrier Controller module for proper
LEN communication.
Carrier Comfort Network
®
Interface
All 30XV units can be connected to the CCN, if desired. The
communication bus wiring is RS-485 Communication Wiring,
CM or CMP rated consisting of a shielded, 3 conductor cable
with drain wire and is field supplied and installed. The system
elements are connected to the communication bus in a daisy
chain arrangement. The positive pin of each system element
communication connector must be wired to the positive pins of
the system elements on either side of it. The negative and signal
ground pins of each system element must also be wired in the
same manner. Wiring connections for CCN should be made at
TB3. See Fig. 22. For noise consideration, communication wir-
ing must be separate and not run in parallel with other wiring.
NOTE: Conductors and drain wire must be 20 AWG (American
Wire Gage) minimum stranded, tinned copper. Individual con-
ductors must be insulated with PVC (Polyvinyl Chloride), PVC/
nylon, vinyl, Teflon
1
, or polyethylene. An aluminum/polyester
100% foil shield and an outer jacket of PVC, PVC/nylon,
chrome vinyl, or Teflon with a minimum operating temperature
range of –20°C to 60°C is required. High temperature applica-
tions may require a higher temperature range. Plenum applica-
tions will require plenum rated cable. Cable voltage require-
ments must match the application.
CHANNEL
IN/OUT
TYPE
BOARD
CONNECTOR
CCN POINT
POINT
DESCRIPTION
I/O POINT
NAME
INPUT/OUTPUT
TYPE
CH 01
AI
J6
—
—
AI-01
5/10K Thermistor
CH 02
AI
SPACETMP
Space temperature
AI-02
10K Thermistor
CH 03
AI
—
—
AI-03
5/10K Thermistor
CH 04
AI
—
—
AI-04
5/10K Thermistor
CH 05
AI
J7A
SP_RESET
Setpoint reset
AI-06
0-5V
CH 06
AI
J7B
LIM_ANAL
Capacity limit
AI-07
0-5V
CH 07
AO
J8
CAP_T
% Total capacity running
AO-01
0-10 Vdc
CH 08
DI
J4, CH8
OCC_OVSW
Occupancy override
DI-01
—
CH 09
DI
J4, CH9
LIM_SW2
Demand limit SW2
DI-02
—
CH 10
DI
J4, CH10
REM_LOCK
Remote lockout switch
DI-03
—
CH 11a
DI
J4, CH11A
ICE_SW
Ice done
DI-04
—
CH 11b
DI
J4, CH11B
—
—
DI-05
—
CH 12
DI
J5, CH12
—
—
DI-06
—
CH 13
DI
J5, CH13
—
—
DI-07
—
CH 14
DI
J5, CH14
—
—
DI-08
—
CH 15
DI
J5, CH15
—
—
DI-09
—
CH 16
DO
J2A
CP_A
Compressor A run status
DO-01
Triac
CH 17
DO
J2A
CP_B
Compressor B run status
DO-02
Triac
CH 18
DO
J2A
—
—
—
—
CH 19
DO
J2A
—
—
—
—
CH 20
DO
J2B
—
—
—
—
CH 21
DO
J2B
—
—
—
—
CH 22
DO
J2B
—
—
—
—
CH 23
DO
J2B
—
—
—
—
CH 24
DO
J3
SHUTDOWN
Shutdown relay
DO-09
Relay
CH 25
DO
J3
ALERT
Alert relay
DO-10
Relay
1. Teflon is a registered trademark of DuPont.
Summary of Contents for AquaForce 30XV140
Page 79: ...79 Fig 76 VFD Communication Wiring Compressor A B Fan VFD A1 A2 B1 B2...
Page 228: ...228 Fig 90 30XV Typical Field Wiring Schematic cont...
Page 229: ...229 Fig 91 30XV Standard Tier 140 275 All Voltages Power Schematic NOTE See Legend on page 226...
Page 230: ...230 Fig 92 30XV Standard Tier 300 325 All Voltages Power Schematic NOTE See Legend on page 226...
Page 240: ...240 Fig 99 30XV Communication Wiring...
Page 241: ...241 Fig 100 30XV 115V Control Wiring All Tonnages All Voltages...
Page 242: ...242 Fig 101 30XV 24V Control Wiring 30XV140 325 All Voltages...
Page 243: ...243 Fig 101 30XV 24V Control Wiring 30XV140 325 All Voltages cont...
Page 244: ...244 Fig 102 30XV 24V Control Wiring 30XV350 500 All Voltages...
Page 245: ...245 Fig 102 30XV 24V Control Wiring 30XV350 500 All Voltages cont...
Page 246: ...246 Fig 103 Component Arrangement Diagram for 30XV140 325...
Page 247: ...247 Fig 103 Component Arrangement Diagram for 30XV140 325 cont...
Page 248: ...248 Fig 104 Component Arrangement Diagram for 30XV350 500...
Page 337: ...337 APPENDIX J FACTORY SUPPLIED PUMPS cont Fig L System Information...
Page 338: ...338 APPENDIX J FACTORY SUPPLIED PUMPS cont Fig M Unit and Language Settings...
Page 341: ...341 APPENDIX J FACTORY SUPPLIED PUMPS cont Fig P Data Input 2...
Page 342: ...342 APPENDIX J FACTORY SUPPLIED PUMPS cont Fig Q Data Input 3...
Page 347: ...347 APPENDIX J FACTORY SUPPLIED PUMPS cont Fig U Pump Wiring Diagram...