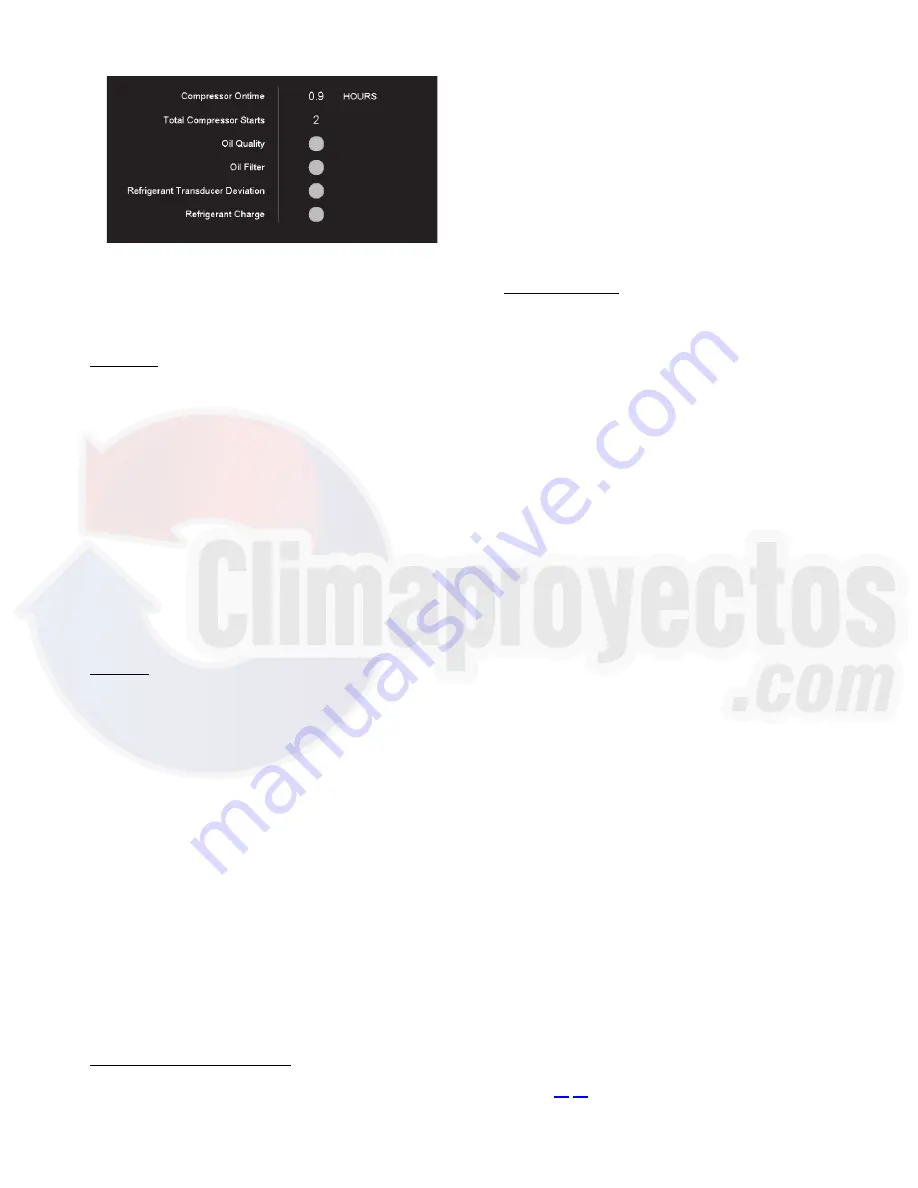
29
The Prognostics status screen displays the following func-
tions (green indicates normal, red indicates program function,
and yellow indicates caution):
Oil Quality — The lubrication oil should be changed regularly
to maintain the appropriate lubrication for the motor and com-
pressor. On the Prognostics status screen, a green light is dis-
played for Oil Quality if the operating time is less than 90% of
the configured oil change duration and total time (includes
operation and non-operation) is less than 90% of the oil store
duration.
A yellow light is displayed if the operating time is more
than 90% of configured oil change duration or if total time (in-
cludes operation and non-operation) is more than 90% of the
oil store duration.
A red light is displayed if the operating time is greater than
configured oil change duration, or if total time (includes opera-
tion and non-operation) is more than oil store duration, and oil
change is not completed.
When the light is red or yellow, the oil change completed
flag is set to NO by the controller. After the oil has been
changed, the oil change completed flag should be set to YES
manually. The controller then changes the light to green.
Oil Filter — This alert function is active only in an oil pump
control test. Two transducers, one located before the oil pump
and the other located after the oil filter, are used to identify
when the pressure differential has fallen below the alert thresh-
old. If the oil pump is forced to ON and after 10 seconds, if the
pressure differential is lower than the threshold set in the Oil
Filter Pres Diff field, the filter needs to be replaced and the
dedicated alert 160 is reported.
The Oil Filter light is updated in control test mode automat-
ically and can be reset to green in all modes manually.
If the oil pump is forced to ON and after 10 seconds, if the
pressure differential is lower than the threshold, the Oil Filter
red light is displayed on the Prognostics status screen.
If the oil pump is forced to ON and after 10 seconds, if the
pressure differential is between the threshold and the threshold
plus 2 psig, the yellow light is displayed on the Prognostics sta-
tus screen.
If oil pump is forced to ON and after 10 seconds, if the pres-
sure differential is greater than the alert threshold plus 2 psig,
the green light is displayed on the Prognostics status screen.
When the light is red or yellow, the Oil Filter Change Done
flag is set to NO by the controller. After the oil filter is changed,
the Oil Filter Change Done flag should be set to YES manually.
The controller then changes the Oil Filter light to green.
Refrigerant Transducer Calibration — When the unit is
offline for more than 5 minutes, a comparison is made among
the evaporator, condenser, and economizer refrigerant pres-
sure transducers. A difference of more than the configurable
threshold set in the Trans Calib Threshold option generates
an alert 161 that a calibration is required. The comparison is
done for all of the transducers.
A value more than the configurable threshold displays the
red light in for Refrigerant Transducer Calibration in the Prog-
nostics status screen. A value more than 0.9 times the configu-
rable threshold displays the yellow light in the Prognostics sta-
tus screen. A value less than 0.9 times the configurable thresh-
old displays the green light in the Prognostics status screen.
When the light is red or yellow, the Trans Calibration Done
flag is set to NO by the controller. After transducer re-calibra-
tion, the Trans Calibration Done flag should be set to YES
manually. The controller then changes the Refrigerant Trans-
ducer Calibration light to green.
Refrigerant Charge — This function uses the evaporator
approach (Evap Design Approach) setting and compressor dis-
charge temperature (Bearing Degradation) setting in relation to
the condenser refrigerant temperature (Low Charge Cond
Approach) setting to generate an alert 162 of possible low
refrigerant charge and display the red light based on the fol-
lowing conditions:
• compressor is running but not in ramp loading status; and
• condenser approach is greater than 0.9 times the low
refrigerant charge condenser approach threshold; and
• evaporator approach is 2° F (1.1° C) greater than design
approach (ap_dgap)
The Refrigerant Charge yellow light is displayed under the
following conditions:
• compressor is running but not in ramp loading status; and
• condenser approach is greater than low refrigerant
charge condenser approach threshold (rch_cath); and
• evaporator approach is 1.8° F (1° C) greater than design
approach (ap_dgap)
When the light is red or yellow, the Refrigerant Charge
Done flag is set to NO by the controller. After the refrigerant
charge is completed, the Refrigerant Charge Done flag should
be set to YES manually. The controller then changes the Re-
frigerant Charge light to green.
MASTER SLAVE CONTROL — This control, available
from page 2 of the Configuration Menu, provides the capabil-
ity to operate 2 chillers in Master/Slave mode. The slave chiller
should be set to NETWORK mode and controlled by the mas-
ter chiller.
The two chillers can be configured to be in parallel or in se-
ries. When they are in series mode, the master chiller’s evapo-
rator must be downstream. The user can configure which con-
denser (master or slave) is downstream. The master chiller
shall monitor all external commands such as start/stop, demand
limiting, or setpoint configuration.
The master/slave function provides the ability to select a
lead chiller from the master and the slave chillers. Selection is
based on the delta between the master and the slave run hours,
and tries to optimize the runtime hours. If this function is not
set, the lead chiller is always the master chiller and should be
changed to lag in case of failure.
The lead chiller shall always be started first, and the lag
chiller shall be maintained at zero percent capacity. When the
lead chiller cannot be loaded anymore, then the lag start timer
is started. The lag chiller shall always be stopped prior to lead
chiller.
If a communication failure is detected between the master
and the slave chillers, all master/slave functions are disabled
and chillers return to stand-alone operations until communica-
tion is reestablished. If middle sensor is installed, this, among
other things, can be configured in the Master Slave Config ta-
ble. Fig. 51-53 show Master/Slave Config options.
a19-2324
Fig. 50 — Prognostics Status Screen