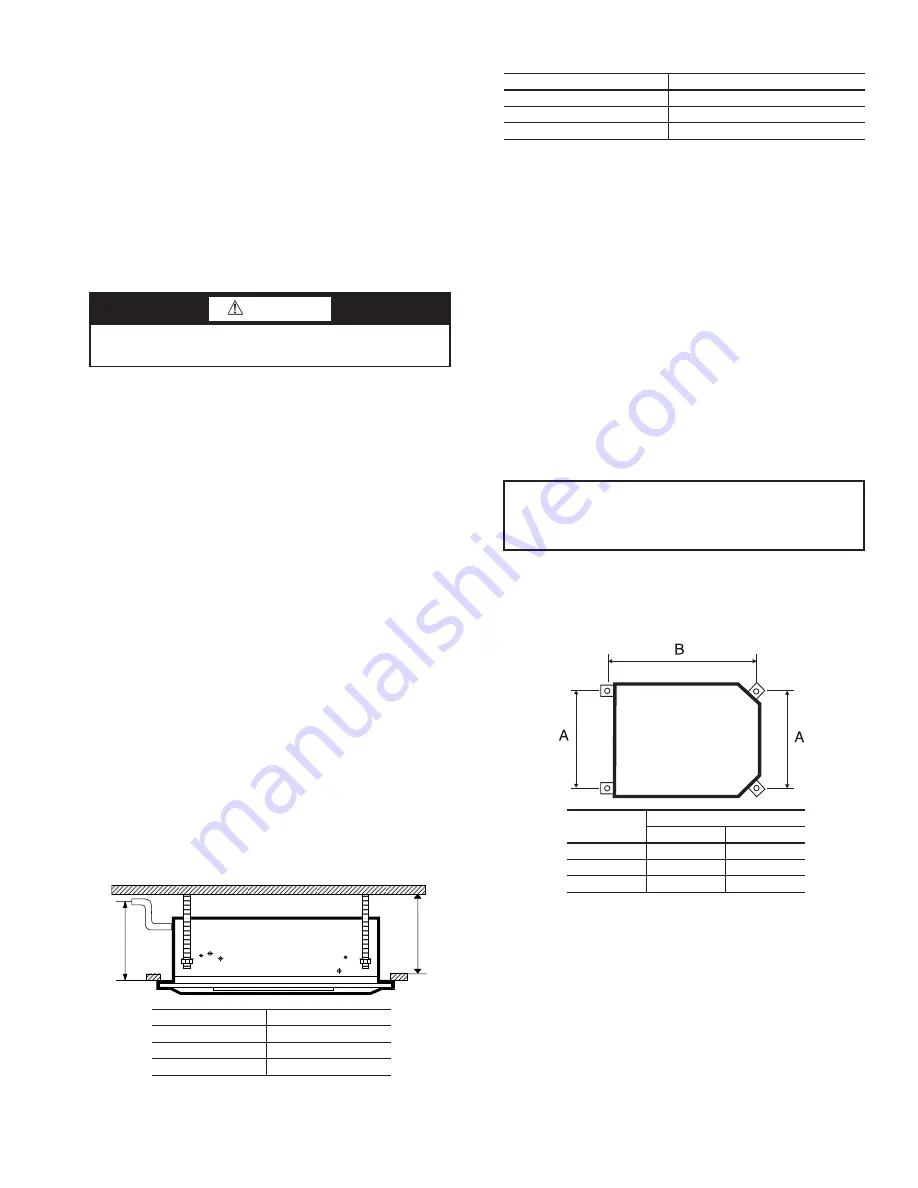
19
PRE-INSTALLATION
Unpack Unit —
Remove the banding straps and lift the
cardboard lid. Remove the fascia, packed in bubble wrap, and
polystyrene packing pieces to expose the unit.
When removing the unit chassis from the box, the four cor-
ner brackets should be utilized for lifting. In order to protect the
fascia from dirt and damage, it should be returned to the box
until it is ready to be installed.
Blank Off Pieces —
When branch ducting is to be used,
polystyrene pieces for blanking off fascia openings are includ-
ed with the fascia packing. Up to two opposing sides may be
blanked off. See Duct Collars in Installation section.
Positioning
The unit installation position should be selected with the fol-
lowing points in mind:
1. The appliance must be installed on a structure that is suit-
able to support the total weight of the appliance, piping,
and condensate.
2. Piping, electrical panel and condensate pump access pan-
el should be readily accessible for maintenance purposes.
A 2-ft clearance is recommended around the electrical
panel and condensate pump access panel.
3. The unit should not be positioned less than 5 ft from a
wall or similar obstruction, or in a position where the dis-
charge air could blow directly on to the thermostat. A 5 ft
clearance is required below the unit for service access.
4. The unit should not be positioned directly above any
obstructions.
5. The unit must be installed square and level.
6. The condensate drain should have sufficient downward
slope (1 inch in 100 in.) in any horizontal run between
unit and drain. Maximum condensate pump lift is
30 inches.
7. There should be sufficient room above the false ceiling
for installing the unit. Minimum distance as shown in
Fig. 18.
8. In case of high humidity, clogged or damaged condensate
piping, incorrect installation or faulty condensate pump,
water may drip from the unit. Do not install the appliance
where dripping water can cause damage.
Ceiling Opening Sizes —
An opening in the false ceil-
ing will then have to be cut to the size shown in Table 2.
Table 2 — Ceiling Opening Dimensions
A cardboard template for ceiling cutout and rod positions is
included with the unit.
Positioning the Electro-Mechanical Thermo-
stat —
In addition to positioning the unit correctly, it is very
important to locate the wall-mounted thermostat in the opti-
mum position to ensure good temperature control. Therefore,
the installation should be selected with the following points in
mind:
1. Position the thermostat approximately 48 in. above floor
level.
2. Do not position thermostat where it can be directly affect-
ed by the unit's discharge airstream.
3. Avoid external walls and drafts from windows and doors.
4. Avoid positioning near shelves and curtains as these re-
strict air movement.
5. Avoid heat sources e.g., direct sunlight, heaters, dimmer
switches and other electrical devices.
INSTALLATION
Hanger Bolts —
The hanger bolts can now be installed at
the centers shown in Fig. 19. Use
3
/
8
in. all thread rod.
Check the strength of the unit mounting hanger bolts. Refer
to Table 1 for unit weights.
Installation Guide —
An installation guide is included
in the Carrier Owner Information packet provided with the
unit. Prepare the installation guide by folding the flat metal
piece, by hand, along the perforations as shown in Fig. 20.
INSTALLATION GUIDE SETUP — The unit can now be
lifted onto the hanging rods and leveled at the correct distance
from the ceiling with the aid of the installation guide.
1. Hold the tab on the installation guide against the bottom
of the cassette case with the guide pointing away from the
cassette. See Fig. 21.
DANGER
Appliances must not be installed where they may be
exposed to potentially explosive or flammable atmosphere.
A
30 in.
MAX.
Fig. 18 — Minimum Distance to Ceiling
42WKN UNIT SIZE
DIMENSION A (in.)
08,12
12
3
/
4
18,20
11
1
/
2
33,36
13
1
/
2
a42-4049
42WKN UNIT SIZE
DIMENSIONS (in.)
08,12
23 in. x 23 in.
18,20
34 in. x 34 in.
33,36
46 in. x 34 in.
IMPORTANT: Make sure the ceiling grid is supported sep-
arately from the appliance. The ceiling must not be sup-
ported by any part of the appliance, fascia or any associated
wiring or pipe work.
Fig. 19 — Hanger Bolt Mounting Dimensions
42WKN
UNIT SIZE
DIMENSIONS (in.)
A
B
08,12
19
1
/
2
23
18,20
28
1
/
2
31
1
/
2
33,36
28
1
/
2
43
1
/
2
a42-4022