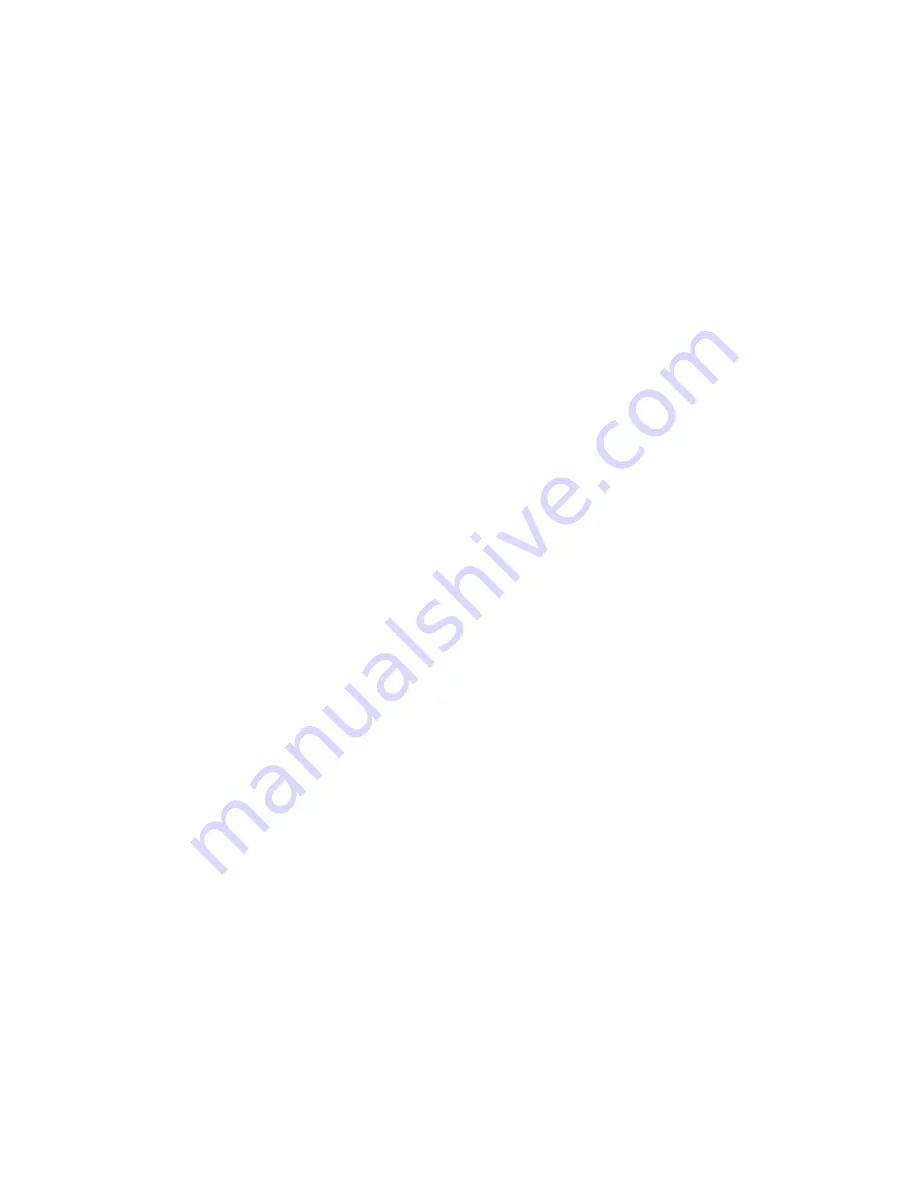
6-21
T--317
7. The Display module will go blank briefly, then read
“Pro donE” when the software loading has loaded. (If
a problem occurs while loading the software: the Dis-
play will blink the message “Pro FAIL” or “bad 12V”.
Turn start-stop switch OFF and remove the card.)
8. Turn unit OFF, via start-stop switch (ST).
9. Remove the programming card from the program-
ming/software port and return the unit to normal op-
eration by placing the start-stop switch in the ON
position.
b. Procedure for loading Configuration Software
1. Turn unit OFF using start-stop switch (ST).
2. Insert the programming card for Operationa Soft-
ware into the programming/software port. (See
Figure 6-22.)
3. Turn unit ON using start-stop switch (ST).
4. The Display module will show “nt40” on the left LCD
display and “541###” on the right LCD display. “###”
will indicate the dash number for a given unit model
number, use the UP or DOWN ARROW key to scroll
through the list to obtain the proper model dash num-
ber. For example, to program a model number
69NT40-541-05, press the UP or DOWN ARROW
key until the right display shows “nt40” on the right
display and “54105” on the left. (If a defective card is
being used, the Display will blink the message “bAd
CArd”. Turn start-stop switch OFF and remove the
card.)
5. Press the ENTER key on the keypad.
6. When the software loading has successfully com-
pleted, the Display will show the message “EEPrM
donE.” (If a problem occurs while loading the soft-
ware, the Display will blink the message “Pro FAIL”
or “bad 12V.” Turn start-stop switch OFF and remove
the card.)
7. Turn unit OFF using start-stop switch (ST).
8. Remove the programming card from the program-
ming/software port and return the unit to normal op-
eration by placing the start-stop switch in the ON
position.
6.21.4 Removing and Installing the Controller
a. Removal:
1. Disconnect all front wire harness connectors and
move wiring out of way.
2 The lower controller mounting is slotted, loosen the
top mounting screw (see Figure 6-22) and lift up and
out.
3 Disconnect the two back connectors (EC) and re-
move module.
4 When removing the replacement controller from its
packaging , note how it is packaged. When returning
the old controller for service, place it in the packaging
in the same manner as the replacement. The pack-
aging has been designed to protect the controller
from both physical and electrostatic discharge dam-
age during storage and transit.
b.Installation:
Install the module by reversing the removal steps.
Torque values for mounting screws (item 2, see
Figure 6-22) are 0.23 mkg (20 inch-pounds). Torque
value for the connectors is 0.12 mkg (10 inch-pounds).
6.21.5 Battery Replacement
If required, use tool 07-00418-00.
6.22 VENT POSITION SENSOR SERVICE
The fresh air vent position sensor alarm (AL50) will
occur if the sensor reading is not stable for 4 minutes or if
the sensor is outside of its valid range (shorted or open).
This can occur if the vent is loose or the panel is
defective. To confirm a defective panel, assure that the
wing nut is secure and then power cycle the unit. If the
alarm immediately reappears as active, the panel
should be replaced.
The alarm should immediately go inactive, check the
4--minute stability requirement. If the alarm reoccurs
after the four minutes and the panel was known to have
been stable, then the panel should be replaced.
The vent position sensor is calibrated using the keypad
as follows (Only required when installing a new panel) :
1. Set the vent to the 0 CMH/ CFM position.
2. Code select 45 will automatically displayed. Press the
Enter key and hold for 5 seconds.
3. After the enter key has been pressed CAL for calibra-
tion is displayed.
4. Press the ALT MODE key on the display and hold for
five seconds.
5. After the calibration has been completed, Code 45 will
display 0 CMH / CFM.
6.23 TEMPERATURE SENSOR SERVICE
Procedures for service of the Return Recorder, Return
Temperature, Supply Recorder, Supply Temperature,
Ambient, Defrost Temperature, Compressor Discharge
and Compressor Suction temperature sensors are
provided in the following sub paragraphs.
6.23.1 Sensor Checkout Procedure
To check a sensor reading, do the following:
a. Remove the sensor and place in a 0
_
C (32
_
F) ice-wa-
ter bath. The ice-water bath is prepared by filling an
insulated container (of sufficient size to completely
immerse bulb) with ice cubes or chipped ice, then fill-
ing voids between ice with water and agitating until
mixture reaches 0
_
C (32
_
F) measured on a labora-
tory thermometer.
b. Start unit and check sensor reading on the control
panel. The reading should be 0
_
C (32
_
F). If the read-
ing is correct, reinstall sensor; if it is not, continue with
the following.
c. Turn unit OFF and disconnect power supply.
d. Refer to paragraph 6.21 and remove controller to gain
access to the sensor plugs.
e. Using the plug connector marked “EC”, that is con-
nected to the back of the controller, locate the sensor
wires (RRS, RTS, SRS, STS, AMBS, DTS, CPDS
OR CPSS as required). Follow those wires to the con-
nector and using the pins of the plug, measure the
resistance. Values are provided in Table 6-1.