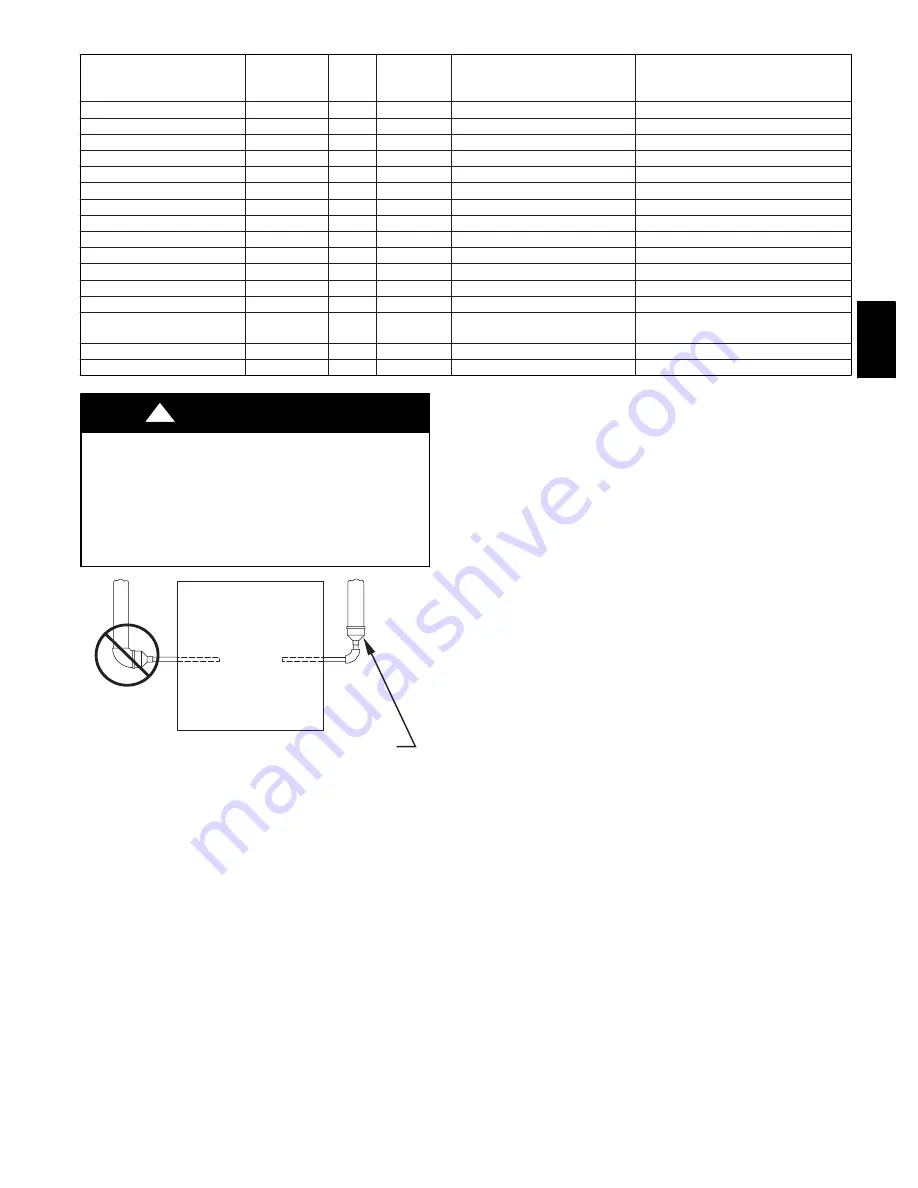
19
TABLE 5—APPROVED COMBUSTION--AIR AND VENT PIPE, FITTING AND CEMENT MATERIALS
ASTM
SPECIFICATION
(MARKED ON MATERIAL)
MATERIAL
PIPE
FITTINGS
SOLVENT CEMENT AND
PRIMERS
DESCRIPTION
D1527
ABS
Pipe
—
—
Schedule---40
D1785
PVC
Pipe
—
—
Schedule---40
D2235
For ABS
—
—
Solvent Cement
For ABS
D2241
PVC
Pipe
—
—
SDR---21 & SDR---26
D2466
PVC
—
Fittings
—
Schedule---40
D2468
ABS
—
Fittings
—
Schedule---40
D2564
For PVC
—
—
Solvent Cement
For PVC
D2661
ABS
Pipe
Fittings
—
DWV at Schedule---40 IPS sizes
D2665
PVC
Pipe
Fittings
—
DWV
F438
CPVC
—
Fittings
—
Schedule---40
F441
CPVC
Pipe
—
—
Schedule---40
F442
CPVC
Pipe
—
—
SDR
F493
For CPVC
—
—
Solvent Cement
For CPVC
F628
ABS
Pipe
—
—
Cellular Core DWV at Schedule---40
IPS sizes
F656
For PVC
—
—
Primer
For PVC
F891
PVC
Pipe
—
—
Cellular Core Schedule---40 & DWV
UNIT MAY NOT OPERATE
Failure to follow this caution may result in intermittent unit
operation.
When vent pipe is exposed to temperatures below freezing,
such as when it passes through an unheated space or when a
chimney is used as a raceway, pipe must be insulated as
shown in Table 7 with Armaflex--type insulation.
CAUTION
!
FURNACE
PIPE DIAMETER
TRANSITION IN
VERTICAL SECTION
NOT IN
HORIZONTAL
SECTION
A93034
Fig. 24
---
Combustion--Air and Vent Pipe Diameter
Transition Location and Elbow Configuration
Furnace combustion air and vent pipe connections are sized for
2--in. pipe. Any pipe size change should be made outside furnace
casing in vertical pipe. The transition has to be made as close to
the furnace as reasonably possible. (See Fig. 24.)
Installation Guidelines for Combustion Air Pipe and Vent
Pipe
It is recommended that all pipes be cut, prepared, and
preassembled before permanently cementing any joint.
1. Attach combustion air pipe and vent pipe per instructions
in sections “Combustion Air Pipe” and “Vent Pipe.”
2. Working from furnace to outside, cut pipe to required
length(s).
3. Deburr inside and outside of pipe.
4. Chamfer outside edge of pipe for better distribution of
primer and cement.
5. Clean and dry all surfaces to be joined.
6. Check dry fit of pipe and mark insertion depth on pipe.
7. After pipes have been cut and preassembled, apply
generous layer of cement primer to pipe fitting socket and
end of pipe to insertion mark. Quickly apply approved
cement to end of pipe and fitting socket (over primer).
Apply cement in a light, uniform coat on inside of socket
to prevent buildup of excess cement. Apply second coat.
8. While cement is still wet, twist pipe into socket with 1/4
turn. Be sure pipe is fully inserted into fitting socket.
9. Wipe excess cement from joint. A continuous bead of
cement will be visible around perimeter of a properly
made joint.
10. Handle pipe joints carefully until cement sets.
11. Horizontal portions of the venting system shall be
supported to prevent sagging. Support combustion air
piping (if applicable) and vent piping a minimum of every
5 ft (3 ft for SDR--21 or --26 PVC) using perforated metal
hanging strap.
12. Slope combustion air piping (if applicable) and vent
piping downward towards furnace a minimum of 1/4--in.
per linear ft with no sags between hangers.
13. Horizontal portions of the venting system shall be installed
so as to prevent the accumulation of condensate.
14. Use appropriate methods to seal openings where
combustion air pipe (if applicable) and vent pipe pass
through roof or sidewall.
Combustion--Air and Vent Pipe Diameter
Determine combustion--air and vent pipe diameter.
1. Using Table 8, individually determine the diameter of the
combustion--air and vent pipe allowed. If different, pick
the larger of these two diameters and use this diameter for
both combustion--air and vent pipes.
2. When installing vent systems of short pipe length, use the
smallest allowable pipe diameter. Do not use pipe size
greater than required or incomplete combustion, flame
disturbance, or flame sense lockout may occur.
NOTE
: Do not count elbows or pipe sections in terminations or
within furnace.
58U
VB