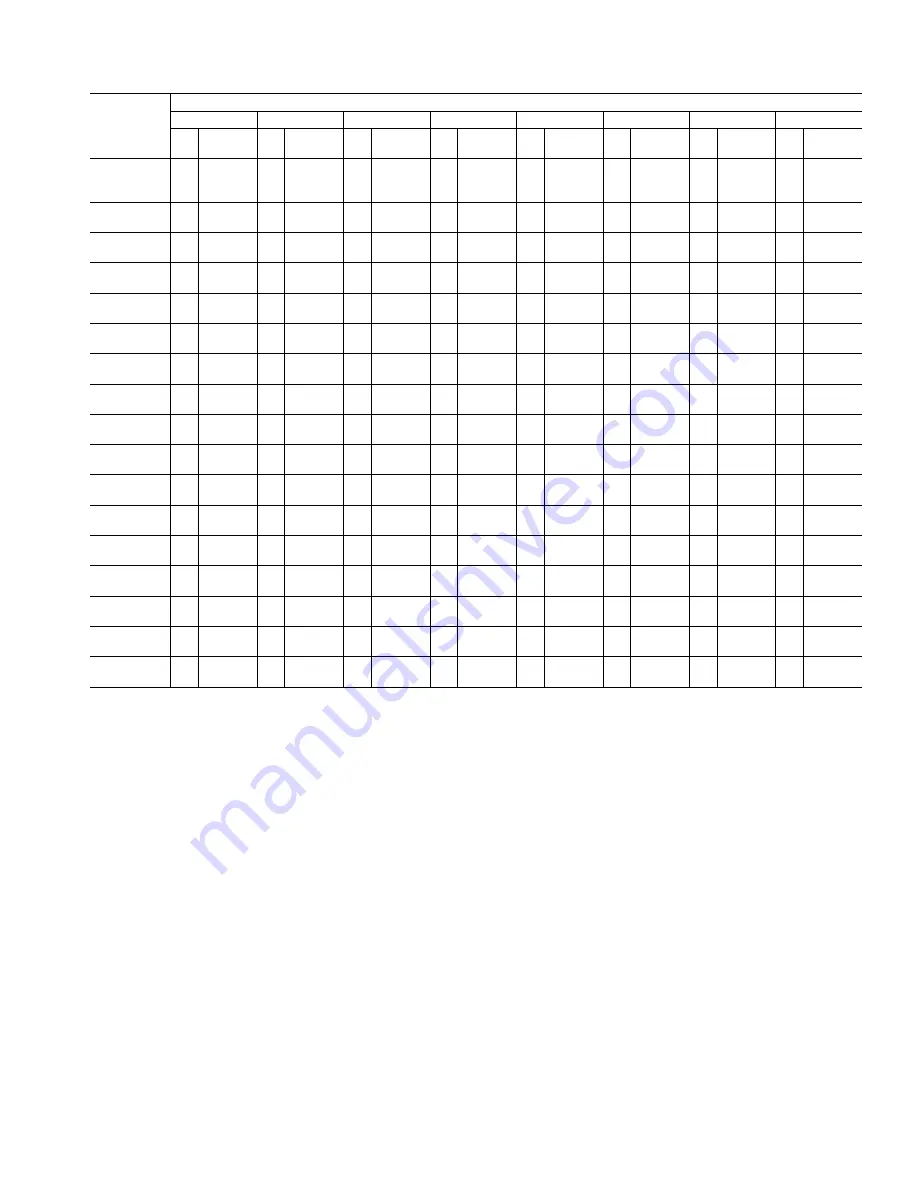
(3.) Turn high-fire adjusting screw (5/64-in. hex Allen
wrench) counterclockwise (out) to decrease input rate
or clockwise (in) to increase rate. When adjusting
input rate, DO NOT set manifold pressure less than
3.2-in. wc or more than 3.8-in. wc for natural gas. If
manifold pressure is outside this range, change main
burner orifices.
(4.) Remove R-to-W2 jumper on control to place furnace
in low-gas-heat operation for low-fire adjustment.
(5.) Turn low-fire adjusting screw (5/64-in. hex Allen
wrench) counterclockwise (out) to decrease input rate
or clockwise (in) to increase rate. When adjusting
input rate, DO NOT set manifold pressure less than
1.3-in wc or more than 1.7-in. wc for natural gas. If
manifold pressure is outside this range, change main
burner orifices.
NOTE:
If orifices are changed, both high-fire and low-fire input
rates must be readjusted with manifold pressures within ranges
specified in items (3). and (5).
NOTE:
If orifice hole appears damaged or is suspected to have
been redrilled, check the orifice size with a numbered drill bit of
the correct size. Never use a redrilled orifice. A burr-free and
squarely aligned orifice hole is essential for proper flame charac-
teristics.
(6.) Remove jumper on R-W/W1 after low-fire adjust-
ments.
(7.) When correct input is obtained, replace gas control
regulator adjustment caps. Main burner flame should
be clear blue, almost transparent. (See Fig. 17.)
2. Set temperature rise.
Place SW-2 in the ON position. Jumper R to W/W1 and W2
to check high-gas-heat temperature rise. To check low-gas-
heat temperature rise, remove jumper to W2. Determine air
temperature rise for both high and low fire using the following
steps. DO NOT exceed the temperature rise ranges specified
on the unit rating plate for high and low fire.
a. Place duct thermometers in return and supply ducts as near
furnace as possible. Be sure thermometers do not see heat
exchangers so that radiant heat will not affect thermometer
readings. This is particularly important with straight-run
ducts.
b. When thermometer readings stabilize, subtract return-air
temperature from supply-air temperature to determine tem-
perature rise.
NOTE:
If the temperature rise is outside this range, first check:
(1.) Gas input for low- and high-fire operation.
Table 8—Model 58TMA Orifice Size and Manifold Pressure for Correct Input Rate
(Tabulated Data Based on Altitude Up to 2000 ft and 21,000 Btuh High Heat/13,500 Btuh Low Heat Per Burner)*
GAS
HEAT
VALUE
(BTU/CU FT)
SPECIFIC GRAVITY OF NATURAL GAS
0.58
0.60
0.62
0.64
0.66
0.68
0.70
0.72
Orf
No.
Heat
High/Low
Orf
No.
Heat
High/Low
Orf
No.
Heat
High/Low
Orf
No.
Heat
High/Low
Orf
No.
Heat
High/Low
Orf
No.
Heat
High/Low
Orf
No.
Heat
High/Low
Orf
No.
Heat
High/Low
860
—
—
42
3.5/1.4
42
3.2/1.3
3.6/1.5
41
42
3.3/1.4
3.7/1.5
40
41
42
3.2/1.3
3.4/1.4
3.8/1.6
40
41
3.3/1.3
3.5/1.5
40
41
3.3/1.4
3.6/1.5
39
40
41
3.2/1.3
3.4/1.4
3.7/1.5
875
42
3.2/1.3
42
3.3/1.4
42
3.4/14
41
42
3.2/1.3
3.6/1.5
41
42
33.3/1.4
3.7/1.5
41
42
3.4/1.4
3.8/1.6
40
41
3.2/1.3
3.5/1.4
40
41
3.3/1.4
3.6/1.5
890
43
3.8/1.6
42
3.2/1.3
43
3.3/1.4
42
3.4/1.5
41
42
3.2/1.3
3.5/1.5
41
42
3.3/1.4
3.7/1.5
41
42
3.4/1.4
3.8/1.6
40
41
3.2/1.3
3.5/1.4
905
43
3.7/1.5
43
3.8/1.6
43
3.2/1.3
42
3.3/1.4
42
3.4/1.4
41
42
3.2/1.3
3.5/1.4
41
42
3.3/1.4
3.6/1.5
41
42
3.4/1.4
3.7/1.5
920
43
3.6/1.5
43
3.7/1.5
43
3.8/1.6
42
3.2/1.3
42
3.3/1.4
42
3.4/1.4
41
42
3.2/1.3
3.5/1.5
41
42
3.3/1.3
3.6/1.5
935
43
3.4/1.4
43
3.6/1.5
43
3.7/1.5
43
3.8/1.6
42
3.2/1.3
42
3.3/1.3
42
3.4/1.4
41
42
3.2/1.3
3.5/1.4
950
43
44
3.3/1.4
3.8/1.6
43
3.5/1.4
43
44
3.6/1.5
43
3.7/1.5
43
3.8/1.6
42
3.2/1.3
42
3.3/1.4
42
3.4/1.4
965
43
44
3.2/1.3
3.7/1.5
43
44
3.3/1.4
3.8/1.6
43
44
3.5/1.4
43
3.6/1.5
43
3.7/1.5
43
3.8/1.5
42
3.2/1.3
42
3.3/1.4
980
44
3.6/1.3
43
44
3.2/1.3
3.7/1.5
43
44
3.4/1.4
3.8/1.6
43
3.5/1.4
43
3.6/1.5
43
3.7/1.5
43
3.8/1.6
42
3.2/1.3
995
44
3.5/1.4
44
3.6/1.5
44
3.3/1.3
3.7/1.5
43
44
3.4/1.4
3.8/1.6
43
3.5/1.4
43
3.6/1.4
43
3.7/1.5
43
3.8/1.6
1010
44
3.4/1.4
44
3.5/1.4
44
3.2/1.3
3.6/1.5
43
44
3.3/1.3
3.7/1.5
43
44
3.4/1.4
3.8/1.6
43
3.5/1.4
43
3.6/1.5
43
3.7/1.5
1025
44
3.3/1.4
44
3.4/1.4
44
3.5/1.4
43
44
3.2/1.3
3.6/1.5
43
44
3.3/1.3
3.7/1.5
43
44
3.4/1.4
3.8/1.5
43
3.5/1.4
43
3.6/1.5
1040
44
3.1/1.3
44
3.3/1.4
44
3.4/1.4
44
3.5/1.4
43
44
3.2/1.3
3.6/1.5
43
44
3.3/1.3
3.7/1.5
43
44
3.4/1.4
3.8/1.6
43
3.5/1.4
1055
45
3.8/1.6
44
3.2/1.3
44
3.3/1.4
44
3.4/1.4
44
3.5/1.5
43
44
3.2/1.3
3.6/1.5
43
44
3.3/1.4
3.4/1.5
43
44
3.4/1.4
3.8/1.6
1070
45
46
3.7/1.5
3.8/1.6
45
3.8/1.6
44
3.2/1.3
44
3.3/1.4
44
3.4/1.4
44
3.5/1.5
43
44
3.2/1.3
3.6/1.5
43
44
3.3/1.4
3.7/1.5
1085
45
46
3.6/1.5
3.7/1.5
45
3.7/1.5
45
3.8/1.6
44
3.2/1.3
44
3.3/1.4
44
3.4/1.4
44
3.5/1.5
43
44
3.2/1.3
3.6/1.5
1100
45
46
3.5/1.4
3.6/1.5
45
46
3.6/1.8
3.8/1.6
45
3.7/1.5
45
3.8/1.6
44
3.2/1.3
44
3.3/1.4
44
3.4/1.4
44
3.5/1.5
* For size 060125 only, input is 20,500 for high fire. Deduct 0.1-in. wc from manifold pressure shown in table. Change orifice size if manifold pressure falls below 3.2-in.
wc.
15