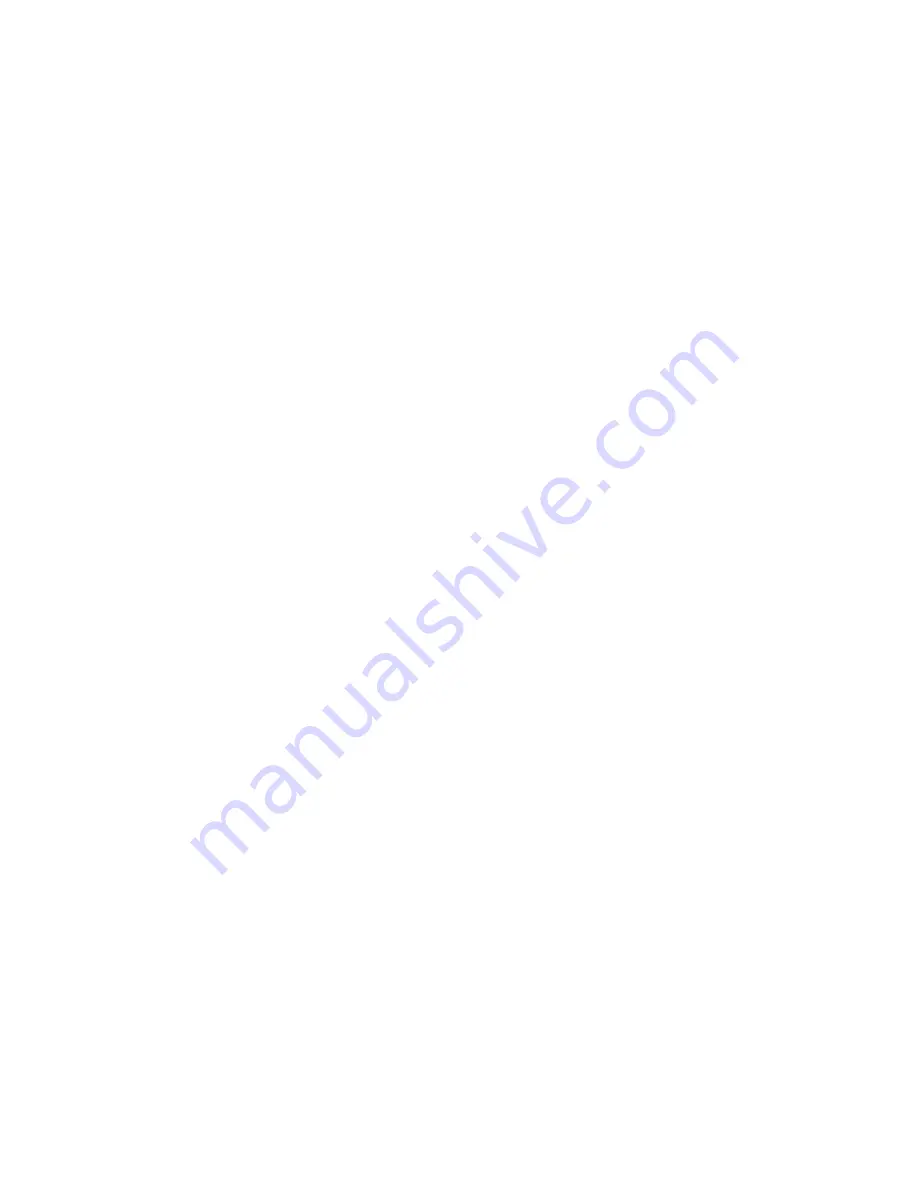
switch to high-heat, as long as the thermostat continues to call for
heat. Subsequent selection is based on stored history of the
thermostat cycle times.
The wall thermostat
″
calls for heat
″
, closing the R to W circuit.
The furnace control performs a self-check, verifies the low-heat
and high-heat pressure switch contacts LPS and HPS are open.
1. Inducer Prepurge Period - The furnace control CPU turns on
inducer motor IDM and slowly increases the inducer motor
speed. When the low-heat pressure switch LPS closes, inducer
motor RPM is noted by the furnace control CPU, and a
25-second prepurge period begins. The RPM is used to
evaluate vent system resistance. This evaluation is then used
to determine the required RPM necessary to operate the
inducer motor during the low-heat prepurge period and
low-heat mode.
NOTE:
The heat cycle can start in either high- or low-heat. If a
high-heat cycle is initiated, the furnace control CPU will de-
energize the high-heat pressure switch relay HPSR to close the NC
contact and continues to increase the inducer motor speed after the
low-heat pressure switch LPS closes. When the high-heat pressure
switch closes, inducer motor RPM is noted by the furnace control
CPU, and a 25-second prepurge period begins. The RPM is used to
evaluate vent system resistance. This evaluation is then used to
determine the required RPM necessary to operate the inducer
motor in high-heat mode.
2. Igniter Warm-Up - At the end of the prepurge period, the
Hot-Surface Igniter HSI is energized for a 17-second igniter
warm-up period.
3. Trial-For-Ignition Sequence - When the igniter warm-up
period is completed the main gas valve relay contact GVR
closes to energize the gas valve solenoid GV-M. The gas valve
solenoid GV-M permits gas flow to the burners where it is
ignited. After 5 seconds, the igniter HSI is de-energized and a
2-second Flame-Proving period begins. If the furnace control
CPU selects high-heat operation, the high-heat gas valve
solenoid GV-HI is also energized.
4. Flame-Proving - When the burner flame is proved at the
flame-proving sensor electrode FSE, the furnace control CPU
begins the blower-ON delay period and continues to hold the
gas valve GV-M open. If the burner flame is not proved within
two seconds, the control CPU will close the gas valve GV-M,
and the control CPU will repeat the ignition sequence for up
to three more Trials-For-Ignition before going to Ignition-
Lockout. Lockout will be reset automatically after three
hours, by momentarily interrupting 115 vac power to the
furnace, or by interrupting 24 vac power at SEC1 or SEC2 to
the furnace control CPU (not at W/W1, G, R, etc.). If flame is
proved when flame should not be present, the furnace control
CPU will lock out of Gas-Heating mode and operate the
inducer motor IDM at full speed until flame is no longer
proved.
5. Inducer Speed Change - If the cycle starts in low-heat, the
furnace control CPU reduces the inducer speed slightly after
flame sense. If the cycle starts in high-heat, the furnace control
CPU increases the inducer speed 15 seconds after flame sense.
The reduction in speed in low-heat is to optimize combustion
for maximum efficiency.
6. Blower-On delay - If the burner flame is proven the
blower-ON delay for low-heat and high-heat are as follows:
Low-heat - 60 seconds after the gas valve GV-M is opened
the blower motor BLWM is turned ON at low-heat airflow.
High-heat - 35 seconds after the gas valve GV-M is opened
the BLWM is turned ON at high-heat airflow.
Simultaneously, the humidifier terminal HUM and electronic
air cleaner terminal EAC-1 are energized and remain ener-
gized throughout the heating cycle.
7. Switching from Low- to High-Heat - If the furnace control
CPU switches from low-heat to high-heat, the furnace control
CPU will de-energize the high-heat pressure switch relay
HPSR to close the NC contact and slowly increase the inducer
motor speed until the high-heat pressure switch HPS closes.
When the high-heat pressure switch HPS closes, the high-heat
gas valve solenoid GV-HI is energized and the inducer motor
RPM is noted by the furnace control CPU. The RPM is used
to evaluate vent system resistance. This evaluation is then
used to determine the required RPM necessary to operate the
inducer motor in high-heat mode. The blower motor BLWM
will transition to high-heat airflow five seconds after the
furnace control CPU switches from low-heat to high-heat.
8. Switching from High- to Low-Heat - The furnace control
CPU will not switch from high-heat to low-heat while the
thermostat R to W circuit is closed when using a single-stage
thermostat.
9. Blower-Off Delay - When the thermostat is satisfied, the R to
W circuit is opened, de-energizing the gas valve GV-M,
stopping gas flow to the burners, and de-energizing the
humidifier terminal HUM. The inducer motor IDM will
remain energized for a 15-second post-purge period. The
blower motor BLWM and air cleaner terminal EAC-1 will
remain energized at low-heat airflow or transition to low-heat
airflow for 90, 120, 150, or 180 seconds (depending on
selection at blower-OFF delay switches). The furnace control
CPU is factory-set for a 120-second blower-OFF delay.
Step 2—Two-Stage Thermostat and Two-Stage Heating
NOTE:
In this mode the low-heat only switch SW1-2 must be ON
to select the low-heat only operation mode in response to closing
the thermostat R to W1 circuit. Closing the thermostat R to
W1-and-W2 circuits always causes high-heat operation, regardless
of the setting of the low-heat only switch.
The wall thermostat
″
calls for heat
″
, closing the R to W1 circuit for
low-heat or closing the R to W1-and-W2 circuits for high-heat.
The furnace control performs a self-check, verifies the low-heat
and high-heat pressure switch contacts LPS and HPS are open, and
starts the inducer motor IDM in high-speed.
The start up and shut down functions and delays described in item
1. above apply to the 2-stage heating mode as well, except for
switching from low- to high-Heat and vice versa.
1. Switching from Low- to High-Heat - If the thermostat R to
W1 circuit is closed and the R to W2 circuit closes, the furnace
control CPU will de-energize the high-heat pressure switch
relay HPSR to close the NC contact and slowly increase the
inducer motor speed until the high-heat pressure switch HPS
closes. When the high-heat pressure switch HPS closes, the
high-heat gas valve solenoid GV-HI is energized and the
inducer motor RPM is noted by the furnace control CPU. The
RPM is used to evaluate vent system resistance. This evalu-
ation is then used to determine the required RPM necessary to
operate the inducer motor in high-heat mode. The blower
motor BLWM will transition to high-heat airflow five seconds
after the furnace control CPU switches from low-heat to
high-heat.
2. Switching from High- to Low-Heat - If the thermostat R to
W2 circuit opens, and the R to W1 circuit remains closed, the
furnace control CPU will energize the high-heat pressure
switch relay HPSR to open the NC contact and slowly
decrease the inducer motor speed to the required low-heat
RPM. When the high-heat pressure switch HPS opens, the
4