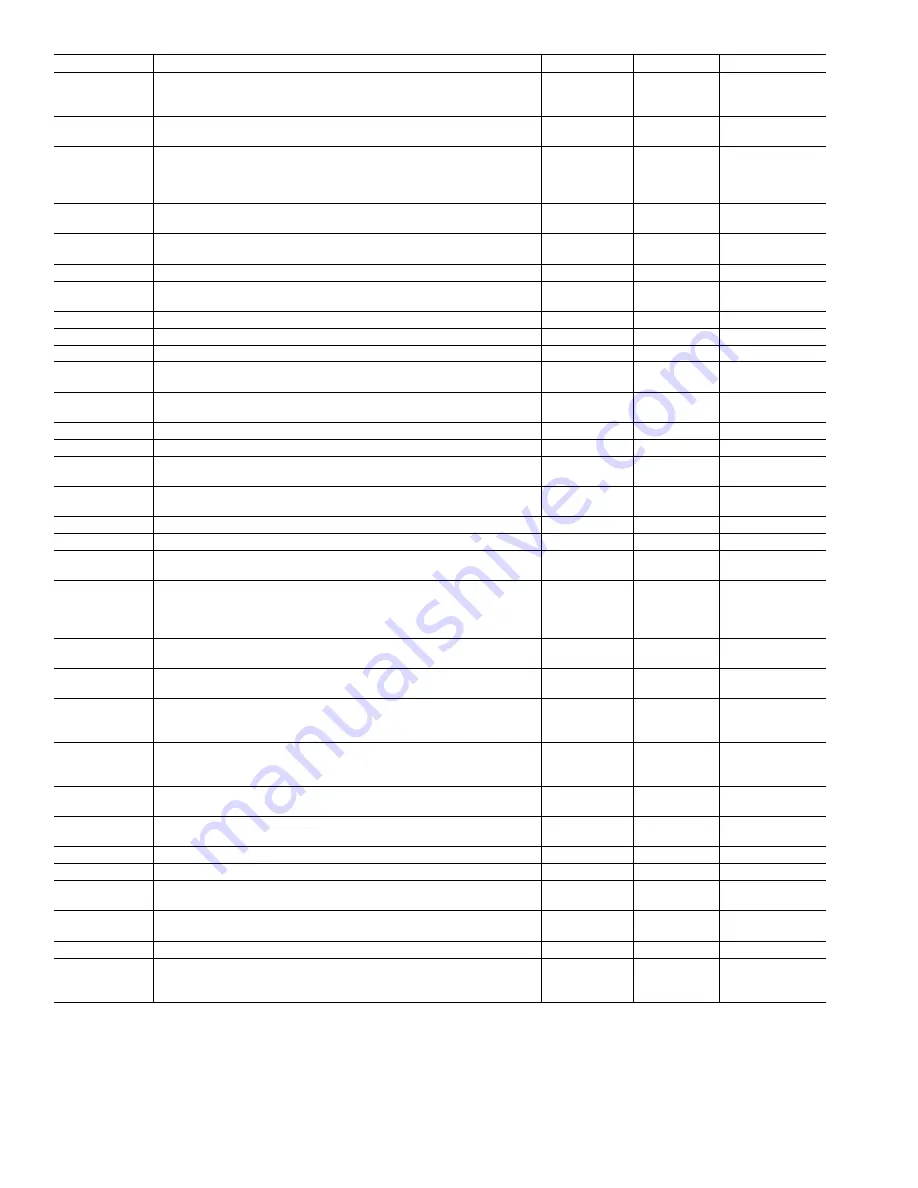
STEP
ACTION
YES
NO
GO TO
19
You have an open wire or bad terminal on the BROWN
wire from the high heat pressure switch HPS to the variable
speed furnace control.
12
20
Turn power off and disconnect jumper wire across R,
W/W1, and W2 thermostat terminals.
21
21
Connect 1 side of slope manometer with a tee to collector
box pressure tap. Connect other side with a tee to gas
valve pressure fitting. Refer to pressure check diagram in
Appendix C.
22
22
Turn power on and jumper R, W/W1, and W2 thermostat
terminals.
23
23
Do you have atleast 1.90 in. wc pressure drop across heat
exchangers when status code 31 flashes?
24
25
24
Replace the pressure switch assembly.
8
25
Is inducer motor rotating in direction indicated on inducer
housing?
27
26
26
Replace inducer motor or inducer motor assembly.
8
27
Turn power off.
28
28
Is inducer wheel okay?
30
29
29
If possible, replace inducer wheel. Otherwise, replace in-
ducer motor assembly.
8
30
Is the inducer wheel properly mounted to the inducer motor
shaft?
31
32
31
Is there any frost build-up on the combustion-air inlet?
14
33
32
Fix problem.
8
33
You have excessive restriction in combustion-air or vent
pipe. Also check for proper vent sizing for installation.
32
34
Continue to observe furnace operation for 20 minutes or
until status code starts flashing.
35
35
Does status code 31 flash?
37
36
36
Does a different status code flash?
7
43
37
Turn power off and disconnect jumper wire across R,
W/W1, and W2 thermostat terminals.
38
38
Connect 1 side of slope manometer with a tee to collector
box pressure tap. Connect other side with a tee to gas
valve pressure fitting. Refer to pressure check diagram in
Appendix C.
39
39
Turn power on and jumper R, W/W1, and W2 thermostat
terminals.
40
40
Monitor slope manometer. Does the pressure reading ap-
pear to be stable when fault occurs?
41
42
41
Replace pressure switch assembly. If problem persists,
check wiring for an intermittent connection in high heat
pressure switch HPS circuit.
8
42
Check for a sag in vent pipe or partially clogged drain trap
or line. Also check for improperly plumbed drainage tubing
within furnace.
8
43
Disconnect jumper wire across R, W/W1, and W2 thermo-
stat terminals and wait for the blower off-delay to finish.
44
44
Reset the power and jumper R and W/W1 thermostat termi-
nals.
45
45
Does status code 31 flash?
47
46
46
Does a different status code flash?
7
8
47
Turn power off and disconnect the GRAY wire to the high
heat pressure switch HPS.
48
48
Turn power ON and jumper R and W/W1 thermostat termi-
nals.
49
49
Does status code 31 flash?
50
13
50
The BROWN wire is shorting to the ORANGE wire that
goes the low heat pressure switch LPS. Reconnect the
GRAY wire to the high heat pressure switch HPS.
12
22