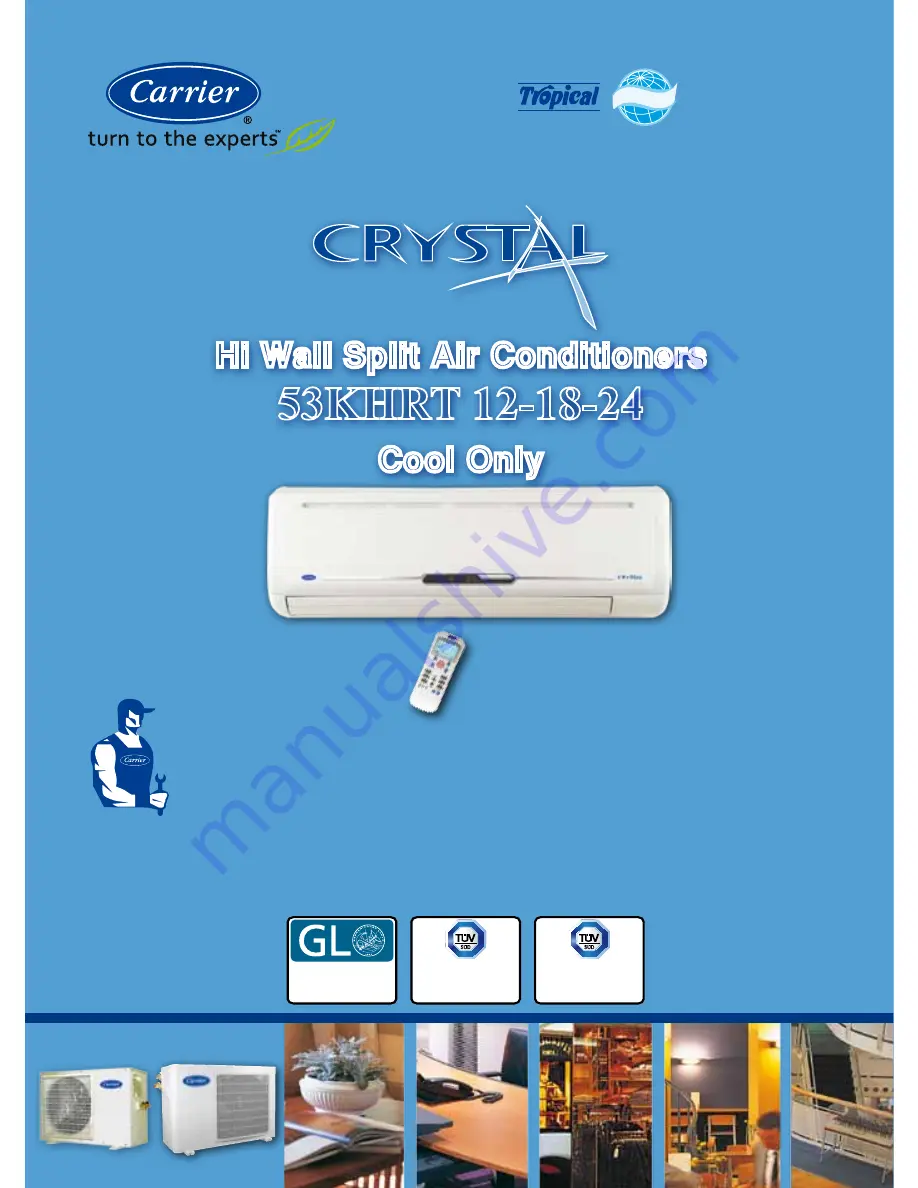
Rev. (0) - 2012
Quality
Management System
ISO 9001 : 2008
Certificate No.: QS-5519HH
Enviromental
Management System
ISO 14001 : 2004
Certificate No : 12 104 30334 TMS
Safety
Management System
BS OHSAS 18001 : 2007
Certificate No : 12 116 30334 TMS
03502825
Carrier is committed to continuously improving its products according to national and international standards
to ensure the highest quality and reliability standards, and to meet market regulations and requirements.
All specifications subject to change without prior notice according to Carrier policy of continuous development.
INSTALLATION MANUAL
Hi Wall Split Air Conditioners
53KHRT 12-18-24
Cool Only
220-240V ~, 50Hz
R22
Summary of Contents for 53KHRT 12-18-24 Crystal
Page 54: ...www miraco com eg...