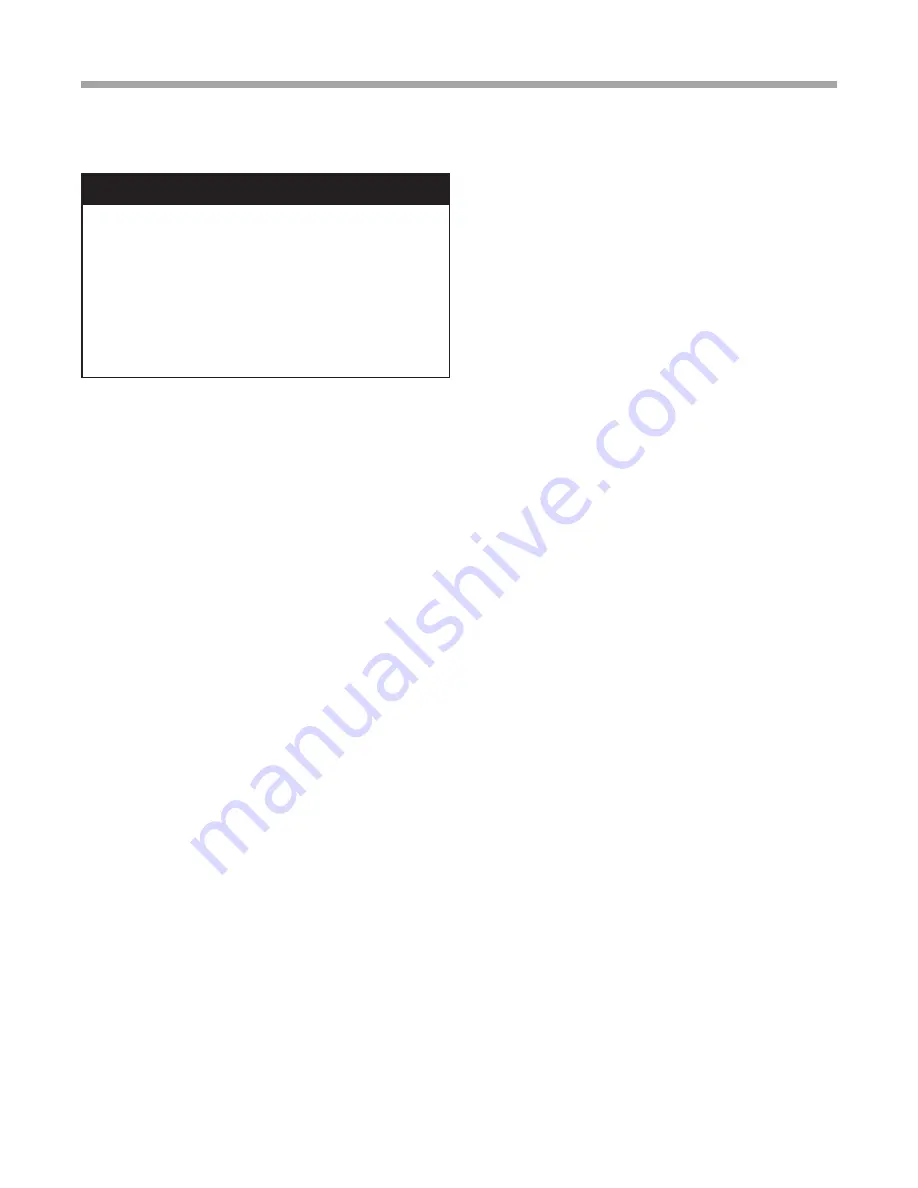
Unit Installation
CAUTION!
The following instructions represent industry
accepted installation practices for closed loop earth
coupled heat pump systems. Instructions are provided
to assist the contractor in installing trouble free ground
loops. These instructions are recommendations only.
State/provincial and local codes MUST be followed and
installation MUST conform to ALL applicable codes. It is
the responsibility of the installing contractor to determine
and comply with ALL applicable codes and regulations.
�
CAUTION!
�
Ground-Loop Heat Pump Applications
Pre-Installation
Prior to installation, locate and mark all existing underground
utilities, piping, etc. Install loops for new construction before
sidewalks, patios, driveways, and other construction has
begun. During construction, accurately mark all ground loop
piping on the plot plan as an aid in avoiding potential future
damage to the installation.
Piping Installation
All earth loop piping materials should be limited to polyethylene
fusion only for in-ground sections of the loop. Galvanized
or steel fittings should not be used at any time due to their
tendency to corrode. All plastic to metal threaded fittings
should be avoided due to their potential to leak in earth
coupled applications. A flanged fitting should be substituted.
P/T plugs should be used so that flow can be measured using
the pressure drop of the unit heat exchanger.
Earth loop temperatures can range between 25 and 110°F [-4
to 43°C]. Flow rates between 2.25 and 3 gpm per ton [2.41
to 3.23 l/m per kW] of cooling capacity is recommended in
these applications.
Test individual horizontal loop circuits before backfilling.
Test vertical U-bends and pond loop assemblies prior to
installation. Pressures of at least 100 psi [689 kPa] should be
used when testing. Do not exceed the pipe pressure rating.
Test entire system when all loops are assembled.
Flushing the Earth Loop
Once piping is completed between the unit, the flow controller
and the ground loop (Figure 1), the loop is ready for final
purging and charging. A flush cart with at least a 1.5 hp
[1.1 kW] pump is required to achieve enough fluid velocity
in the loop piping system to purge air and dirt particles. An
antifreeze solution is used in most areas to prevent freezing.
All air and debris must be removed from the earth loop piping
before operation. Flush the loop with a high volume of water
at a minimum velocity of 2 fps (0.6 m/s) in all piping. The steps
below must be followed for proper flushing.
1. Fill loop with water from a garden hose through the
flush cart before using the flush cart pump to insure an
even fill.
2. Once full, the flushing process can begin. Do not allow
the water level in the flush cart tank to drop below the
pump inlet line to avoid air being pumped back out to
the earth loop.
3. Try to maintain a fluid level in the tank above the return
tee so that air cannot be continuously mixed back into
the fluid. Surges of 50 psi (345 kPa) can be used to help
purge air pockets by simply shutting off the return valve
going into the flush cart reservoir. This “dead heads” the
pump to 50 psi (345 kPa). To purge, dead head the pump
until maximum pumping pressure is reached. Open the
return valve and a pressure surge will be sent through the
loop to help purge air pockets from the piping system.
4. Notice the drop in fluid level in the flush cart tank when
the return valve is shut off. If air is adequately purged
from the system, the level will drop only 1-2 inches (2.5 -
5 cm) in a 10” (25 cm) diameter PVC flush tank (about a
half gallon [2.3 liters]), since liquids are incompressible. If
the level drops more than this, flushing should continue
since air is still being compressed in the loop fluid.
Perform the “dead head” procedure a number of times.
Note: This fluid level drop is your only indication of air
in the loop.
Antifreeze may be added before, during or after the flushing
procedure. However, depending upon which time is chosen,
antifreeze could be wasted when emptying the flush cart
tank. See antifreeze section for more details.
Loop static pressure will fluctuate with the seasons.
Pressures will be higher in the winter months than during
the cooling season. This fluctuation is normal and should be
considered when charging the system initially. Run the unit in
either heating or cooling for a number of minutes to condition
the loop to a homogenous temperature. This is a good time
for tool cleanup, piping insulation, etc. Then, perform final
flush and pressurize the loop to a static pressure of 50-75 psi
[345-517 kPa] (winter) or 35-40 psi [241-276 kPa] (summer).
After pressurization, be sure to loosen the plug at the end
of the Grundfos loop pump motor(s) to allow trapped air to
be discharged and to insure the motor housing has been
flooded. This is not required for Taco circulators. Insure that
the Flow Controller provides adequate flow through the
unit by checking pressure drop across the heat exchanger
and compare to the pressure drop tables at the back of the
manual.
Antifreeze
In areas where minimum entering loop temperatures drop
below 40°F [5°C] or where piping will be routed through
areas subject to freezing, antifreeze is required. Alcohols
and glycols are commonly used as antifreeze; however your
local sales manager should be consulted for the antifreeze
best suited to your area. Low temperature protection should
be maintained to 15°F [9°C] below the lowest expected
entering loop temperature. For example, if 30°F [-1°C] is
the minimum expected entering loop temperature, the
9
Wa t e r- t o - Wa t e r ( 5 0 Y E R ) S e r i e s - P u r o n
®
R e v. : 1 J u l y, 2 0 1 0