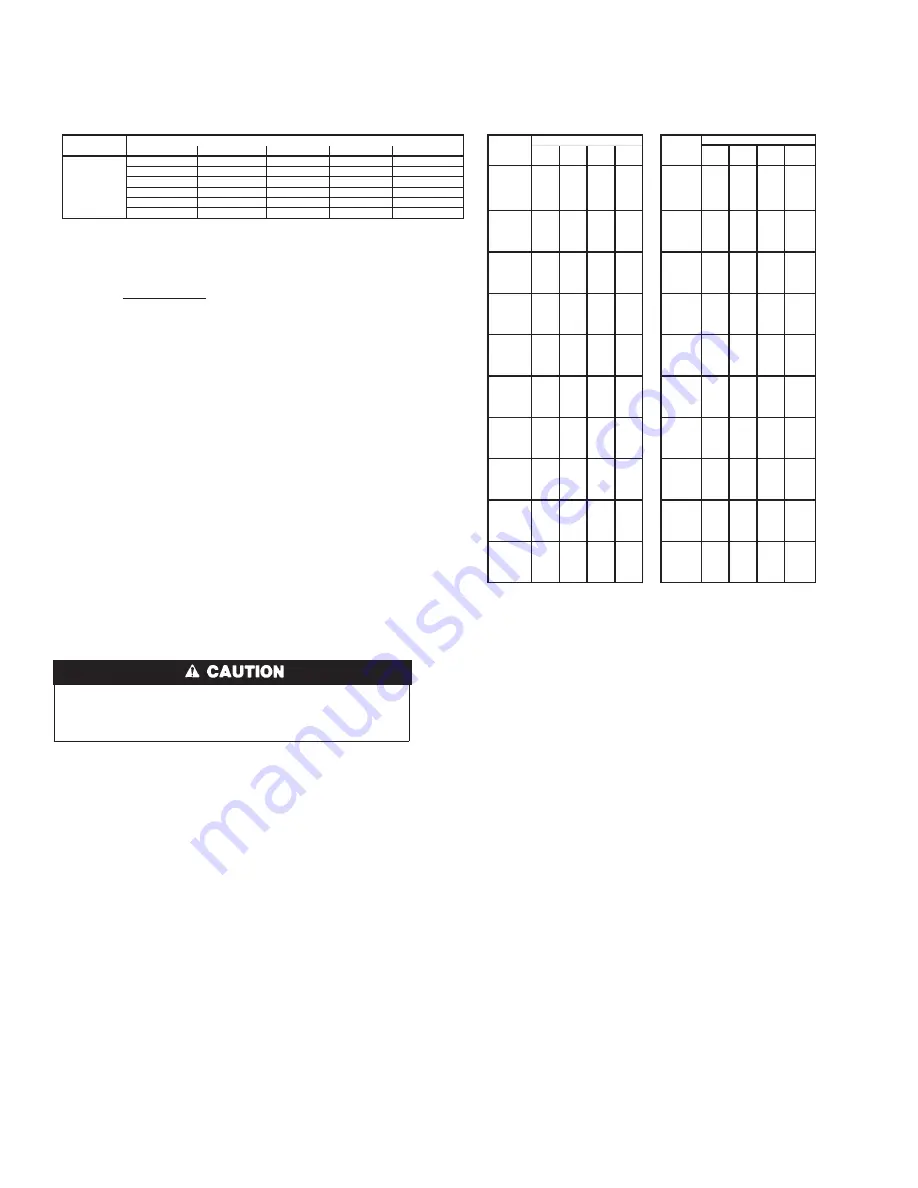
Step 4—Outdoor Fan
Keep the condenser fan free from all obstructions to ensure
proper cooling operation. Never place articles on top of the
unit. Damage to unit may result.
1. Remove 6 screws holding outdoor grille and motor to top
cover.
2. Turn motor/grille assembly upside down on top cover to
expose fan blade.
3. Inspect the fan blades for cracks or bends.
4. If fan needs to be removed, loosen setscrew and slide fan off
motor shaft.
5. When replacing fan blade, position blade so that the hub is 1/8
in. away from the motor end (1/8 in. of motor shaft will be
visible). (See Fig. 23)
6. Ensure that setscrew engages the flat area on the motor shaft
when tightening.
7. Replace grille.
Step 5—Electrical Controls and Wiring
Inspect and check the electrical controls and wiring annually. Be
sure to turn off the electrical power to the unit.
Remove access panel to locate all the electrical controls and
wiring. Check all electrical connections for tightness. Tighten all
screw connections. If any smoky or burned connections are
noticed, disassemble the connection, clean all the parts, restrip the
wire end and reassemble the connection properly and securely.
After inspecting the electrical controls and wiring, replace all the
panels. Start the unit, and observe at least one complete cooling
cycle to ensure proper operation. If discrepancies are observed in
operating cycle, or if a suspected malfunction has occurred, check
each electrical component with the proper electrical instrumenta-
tion. Refer to the unit wiring label when making these checkouts.
Step 6—Refrigerant Circuit
Inspect all refrigerant tubing connections and the unit base for oil
accumulation annually. Detecting oil generally indicates a refrig-
erant leak.
If oil is detected or if low performance is suspected, leak-test all
refrigerant tubing using an electronic leak detector, or liquid-soap
solution. If a refrigerant leak is detected, refer to Check for
Refrigerant Leaks section.
If no refrigerant leaks are found and low performance is suspected,
refer to Checking and Adjusting Refrigerant Charge section.
Step 7—Indoor Airflow
The heating and/or cooling airflow does not require checking
unless improper performance is suspected. If a problem exists, be
sure that all supply- and return-air grilles are open and free from
obstructions, and that the air filter is clean. When necessary, refer
to Indoor Airflow and Airflow Adjustments section to check the
system airflow.
Step 8—Metering Devices–TXV & Accurater Piston
This unit uses 2 types of metering devices. The outdoor metering
device is a fixed orifice and is contained in the brass hex-body in
the liquid line feeding the outdoor coils. The indoor metering
device is a TXV type device.
Fig. 27—Cooling Charging Table-Subcooling
C03027
(psig)
5
10
15
20
(kPa)
3
6
8
11
189
61
56
51
46
1303
13
13
11
8
203
66
61
56
51
1399
13
16
13
10
10.3 (5.7)
9.8 (5.4)
9.4 (5.2)
9 (5)
8.6 (4.7)
210
68
63
58
53
1448
13
17
14
11
NA
NA
NA
NA
NA
217
70
65
60
55
1496
13
18
15
13
17.6 (9.8)
16.8 (9.3)
16.5 (9.2)
15.4 (8.6)
14.3 (7.9)
224
72
67
62
57
1544
13
19
16
14
NA
NA
NA
NA
NA
231
74
69
64
59
1593
13
20
18
15
17.5 (9.7)
16.9 (9.4)
16.6 (9.2)
15.7 (8.7)
14.8 (8.2)
238
76
71
66
61
1641
13
21
19
16
13.7 (7.6)
13 (7.2)
13 (7.2)
14.5 (8.1)
11.5 (6.4)
245
77
72
67
62
1689
13
22
20
17
252
79
74
69
64
1737
13
23
21
18
260
81
76
71
66
1792
13
25
22
19
268
83
78
73
68
1848
13
26
23
20
276
85
80
75
70
1903
13
27
24
21
284
87
82
77
72
1958
13
28
25
22
292
89
84
79
74
2013
13
29
26
23
300
91
86
81
76
2068
13
30
27
24
309
93
88
83
78
2130
13
31
28
26
318
95
90
85
80
2192
13
32
29
27
327
97
92
87
82
2254
13
33
31
28
336
99
94
89
84
2316
13
34
32
29
345
101
96
91
86
2378
13
35
33
30
354
103
98
93
88
2440
13
36
34
31
364
105
100
95
90
2509
13
38
35
32
374
107
102
97
92
2578
13
39
36
33
384
108
103
98
93
2647
13
40
37
34
394
110
105
100
95
2716
13
41
38
35
404
112
107
102
97
2785
13
42
39
36
414
114
109
104
99
2854
13
43
40
37
424
116
111
106
101
2923
13
44
41
38
434
118
113
108
103
2992
13
45
42
39
444
119
114
109
104
3061
13
46
43
40
454
121
116
111
106
3130
13
47
44
41
464
123
118
113
108
3199
13
48
45
42
474
124
119
114
109
3268
13
48
46
43
484
126
121
116
111
3337
13
49
47
44
494
127
122
117
112
3406
13
50
47
45
504
129
124
119
114
3475
13
51
48
46
514
131
126
121
116
3544
13
52
49
46
524
132
127
122
117
3612
13
53
50
47
534
134
129
124
119
3681
13
54
51
48
Required Liquid Line Temperature for
Required Subcooling Deg F (Deg C)
Model Size
a Specific Subcooling (R-410A)
Charging Procedure
7- Read across from the Pressure reading to obtain the Liquid line temperature for a
required Subcooling
6- Find the Pressure Value in the table corresponding to the the measured Pressure of
the Compressor Discharge line.
5- Interpolate if the Outdoor ambient temperature lies in between the table values.
Extrapolate if the temperature lies beyond the table range.
1- Measure Discharge line pressure by attaching a gauge to the service port.
2- Measure the Liquid line temperature by attaching a temperature sensing device to it.
3- Insulate the temperature sensing device so that the Outdoor Ambient doesn’t affect
the reading.
4- Refer to the required Subcooling in the table based on the model size and the
Outdoor Ambient temperature.
8- Add Charge if the measured temperature is higher than the table value.
9- Add Charge using the service connection on the Suction line of the Compressor.
024
030
036
042
048
060
Outdoor Ambient Temperature
75 (24) 82 (28) 85 (29) 95 (35) 105 (41)
Pressure
Pressure
196
1351
Required Subcooling (Deg F)
Required Subcooling (Deg C)
63
58
53
48
13
15
12
9
24