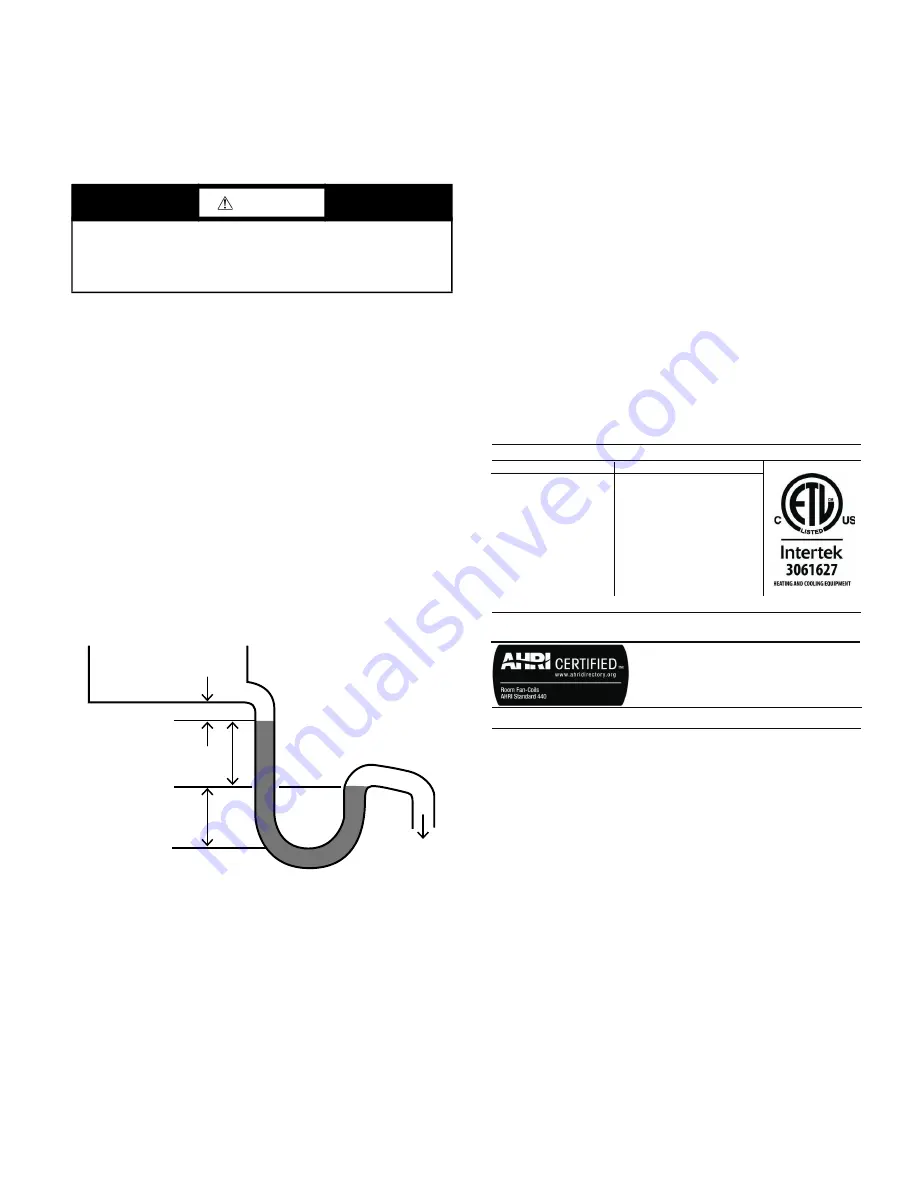
19
LEAK TESTING
After securing the connections, test the system for any leaks.
Always test hydronic systems with water as some components are
not designed to be inert gas pressurized.
Field pressure testing for leaks should not exceed 300 psi for
hydronic coil and valve package components. Consult factory if
higher limits are required.
REFRIGERANT COIL TESTING
Test refrigerant systems with dry nitrogen rather than air to pre
-
vent the introduction of moisture into the system. In the event that
leaking or defective components are discovered, notify the Sales
Representative BEFORE any repairs are attempted. All leaks must
be repaired before proceeding with the installation. In DX
systems, adequate freeze protection should be field-installed. Ex
-
ternal equalizer should be installed by others.
PIPING INSULATION
After system integrity has been established, insulate the piping in
accordance with the project specifications. This is the responsibili
-
ty of the installing or insulation contractor.
CONDENSATE DRAIN
Any fan coil unit with a drain pan is recommended to be equipped
with a drain trap to provide condensate drainage and prevent prop
-
erty damage.
The drain U-trap should be deep enough to offset maximum unit
static pressure difference as shown at Fig. 26, to prevent conden
-
sate flowing back to drain pan.
Fig. 26 —
Condensate Drain U-Trap
CONDENSATE FLOAT SWITCH
The condensate float switch is used to detect clogged or restricted
condensate pan drains. The condensate switch uses a Normally
Closed contact to allow the system control power to pass through
the switch energizing the water valves and fans allowing normal
operation. When an overflow condition is detected by the switch,
it opens the NC contacts and de-energizes the water valves and
fans.
Step 4 — Make Electrical Connections
The unit serial plate lists the unit electrical characteristics includ
-
ing the required supply voltage, fan and heater amperage and re
-
quired circuit ampacity. (See Fig. 27.) The unit wiring diagram
displays all unit and field wiring. Every project is different and
each unit on a project may be different, the installer must be famil
-
iar with the wiring diagram and serial plate on the unit BEFORE
beginning any wiring.
Ensure all field electrical connections are in accordance with unit
wiring diagram and all applicable national and local code. The
type and size of all wiring and other electrical components includ
-
ing circuit breakers, disconnect switches, etc. shall be determined
by the individual job requirements. Verify conductor size is suit
-
able for the distance to the equipment connection and will support
the equipment electrical load. All installations including field
wiring shall be made in compliance with all governing codes and
ordinances. Compliance with all codes is the responsibility of the
installing contractor.
All components furnished for field installation by either the facto
-
ry or the controls contractor shall be located and checked for prop
-
er function and compatibility. Inspect all internal components for
shipping damage. Inspect all electrical connections within the unit
control box and accessories and tighten if necessary.
NOTE: All field wiring must be in accordance with governing
codes and ordinances. Any modification of unit wiring without
factory authorization will invalidate all factory warranties and
nullify any agency listings. The manufacturer assumes no respon
-
sibility for any damages and/or injuries resulting from improper
field installation and/or wiring.
Fig. 27 —
Serial Plate Example
CABINET/CONTROL BOX MAINTENANCE LIGHT
Optional Service Light provides a source of illumination in the
main unit cabinet and the control box during routine maintenance
and troubleshooting in the dark ceiling spaces. Light turns "ON"
when access panel or control box door is open, but unit is not pow
-
ered. (See Fig. 28.)
Step 5 — Connect Ductwork
All ductwork shall be installed in accordance with the project
plans and specifications. See Fig. 22-25 for supply and return duct
flanges location and dimensions.
NOTE: When installing units that attach to branch duct piping, use
industry approved duct standards and configuration such as those
published by Air Conditioning Contractors of America (ACCA)
or American Society of Heating, Refrigeration and Air Condition
-
ing Engineers (ASHRAE). The standards provide necessary infor
-
mation on sizing, layout and installing supply and return air duct
systems.
Flexible duct connections should be used on all air handling
equipment. All ductwork and insulation shall be installed to allow
proper access to all components for service and repair such as fil
-
ters, motor/blower assemblies, etc.
CAUTION
Protect all water coils from freezing after initial filling with
water. Even if the system is drained, unit coils may still hold
enough water to cause damage when exposed to temperatures
below freezing.
Drain Pan
Safety Margin
TSP
TSP
To Drain
Max Water Coil Leaving Air or Max Motor AMB:
Max Fuse or Max Circ Breaker (HACR Type NEC):
Unit Intended for Indoor Use Only & Suited For 0.00 Clearance From Combustible Surfaces
-
25A - SCCR: 5KA
Unit Serial No:
Model No:
42DHA20
776004-60-1
ELECTRICAL
ENV/PERF
Motor(s):
Motor VPH:
Motor FLA:
Heater AMPS:
QTY of Motor(s):
Motor HP:
Min Circ Amps:
Heater VPH:
E020-71537402
277/1/60
5.10A
18.1A
5.0 kW
1
1 HP
29.0A
277/1/60
Max ESP:
Max Inlet Water Temp:
Coil Test:
High Side Coil Design:
Refrigerant Type:
1.65
300 PSIG
-
-
Max Outlet Air Temp:
Max Hot Water or Steam:
ARI Model:
Low Side Coil Design:
-
42DHA20
-
190F
2 PSIG
Heater Kw:
Motor Current:
5.10A
Manufactured in the USA