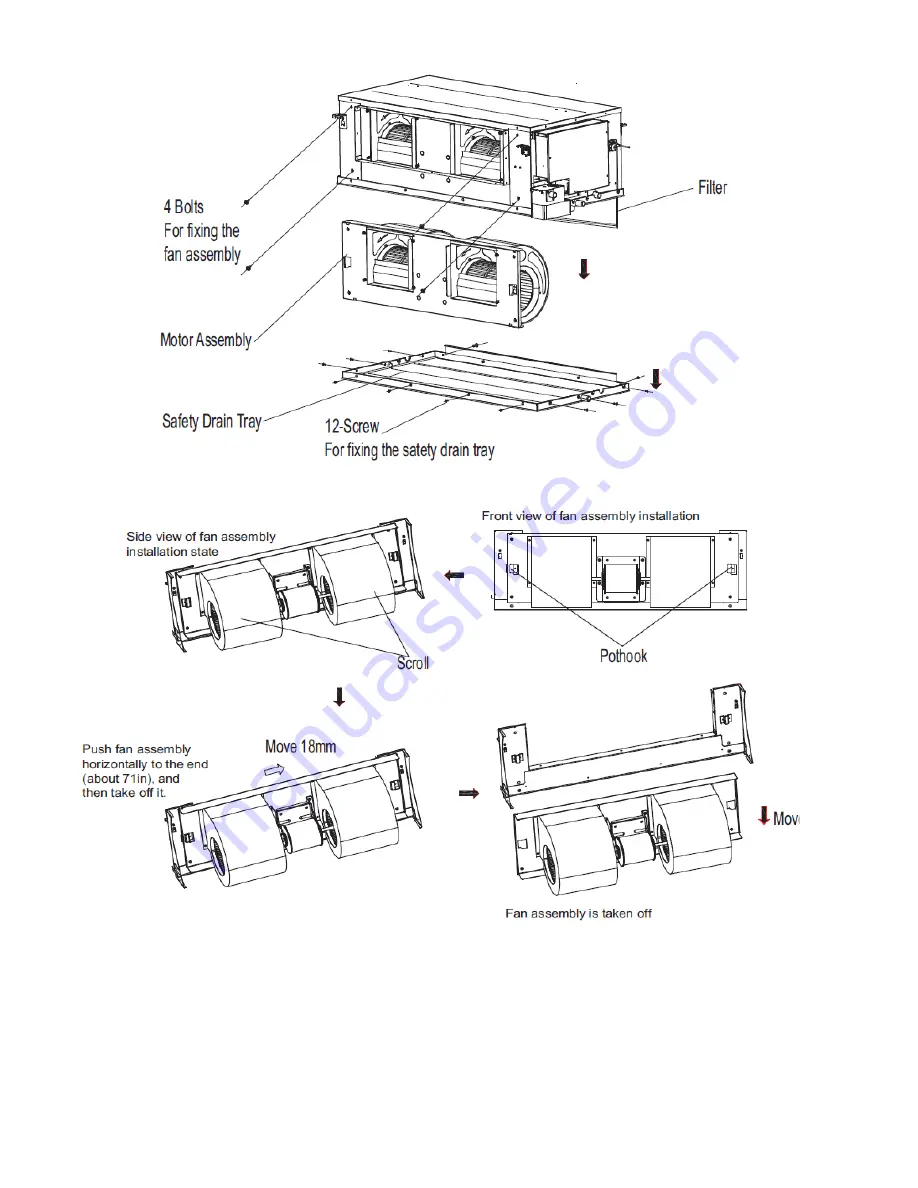
20
Fig. 32 —Fan Disassembly 036-054
Fig. 33 —Fan Disassembly 036-054
1. Remove all 12 screws from the Safety Drain Tray, and remove the safety drain tray as shown in Fig. 32.
2. Remove all four bolts from the fan assembly as shown in Fig. 33.
3. Horizontally push fan assembly until it cannot not move any further.
4. Lift up slightly and take down to remove as shown in Fig. 33.
5. After the motor maintenance is complete, reinstall the fan assemblies, and connect the motor with electric control box.