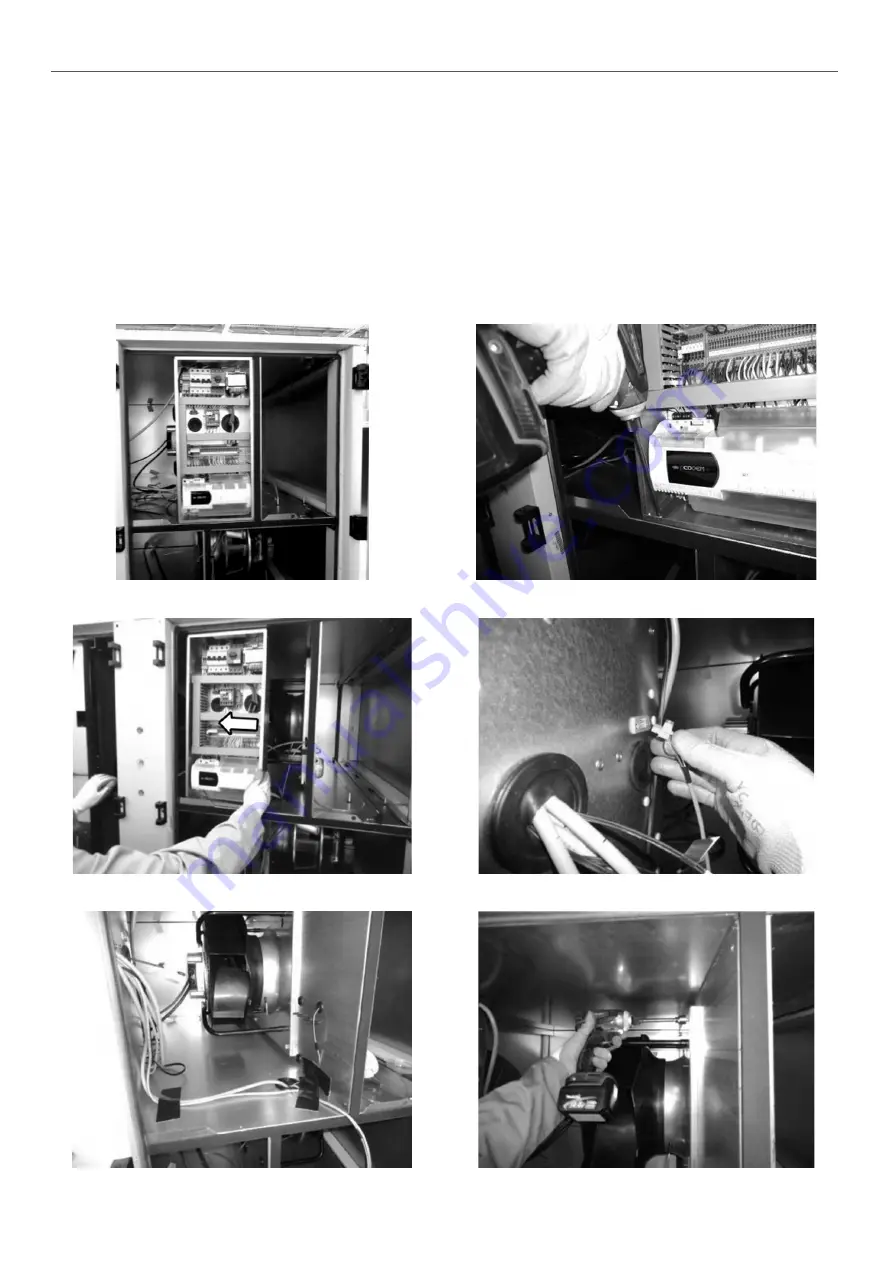
9.2 - FAN MOTOR ASSEMBLY
Check and retighten the electrical connections once a year.
Intake FMA removal method
1. Open the door
2. Release the 4 x M8 screws
3. Disconnect the motor's electrical connections
4. Take out the FMA
Exhaust FMA removal method
1. Open the door
2. Remove the upper and lower fixings from the electrics box
3. Move the electrics box; a sufficient length of cable is provided
4. Disconnect the various quick connectors
5. Provide sufficient clearance
6. Remove the 4 x M8 screws
9 - MAINTENANCE/SERVICE INTERVALS
24