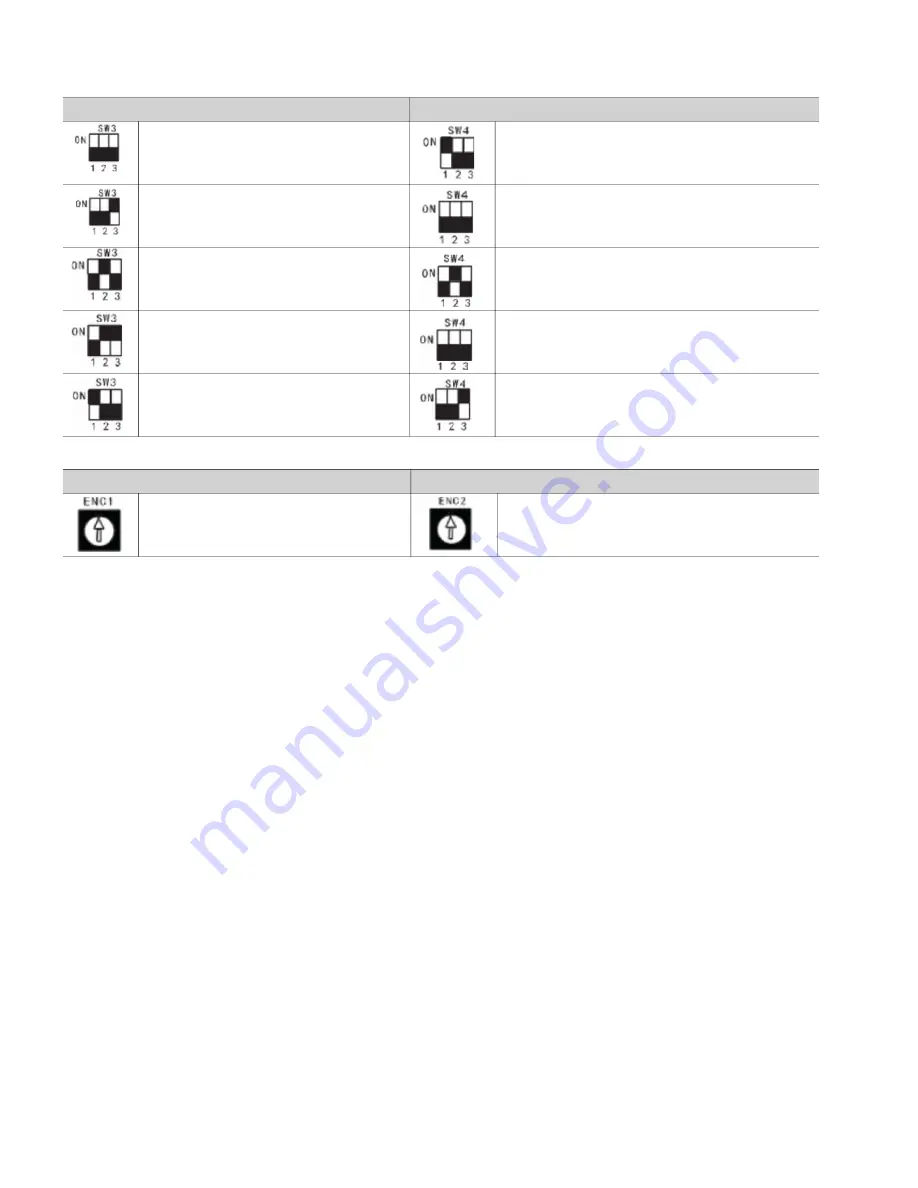
14
Unit Settings
Table 11: SW3 and SW4 Function Definition
Table 12: ENC1 and ENC2
SW3 Function Definition
SW4 Function Definition
Heating priority mode
Automatic addressing
Cooling priority mode
Non-automatic addressing (factory default)
First running priority mode
Clear IDU address
Heating mode only
Fahrenheit temperature (factory default)
Cooling mode only
Celsius temperature
ENC1 Function Definition (factory use only)
ENC2 Function Definition
For factory use only
ODU network address dial-up
Only 0-7 used