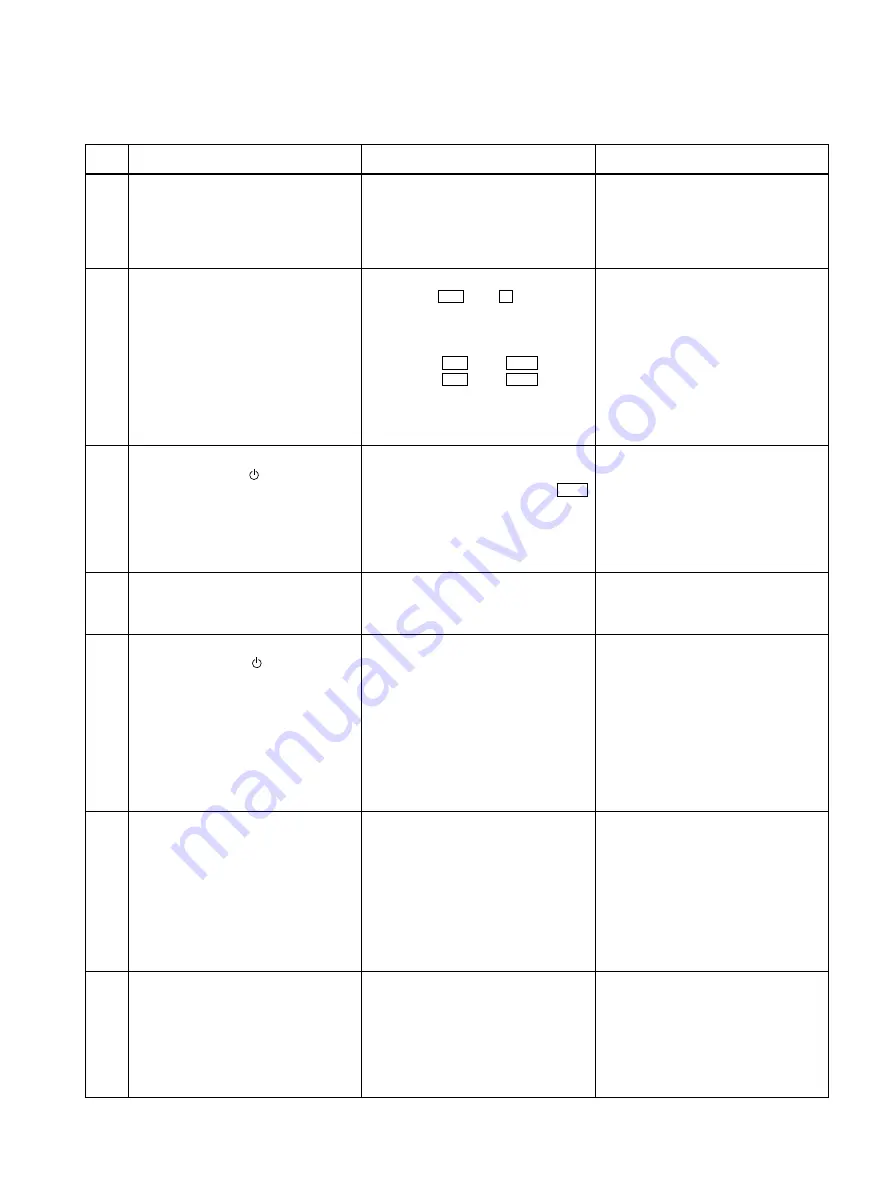
−
54
−
(3) Checking procedure
Table 9-6-1
No.
1
2
3
4
5
6
7
Procedure
1.
•
Application of shock voltage.
•
Overload by short-circuit of the
parts.
1.
•
AC power cord is defective.
•
Poor contact of the terminal plate.
•
Miss wiring of the power relay.
2.
•
Capacitor (C01, C02) is defective.
•
Line filter (L01) is defective.
•
Resistor (R01) is defective.
•
Diode (DB01) is defective.
3. M01, DB01, R01, C03 are
4. IC01 are defective.
defective.
defective relay driver. (Q07)
2. Poor contact of relay.
Defective indicator, or poor
housing assembly. (CN14)
1. The temperature of the indoor
heat exchanger is abnomally lower.
2. Poor contact of the heat
exchanger sensor. (The connector
is disconnected.) (CN01)
3. Heat exchanger sensor, main P.C.
board are defective. (Refer to
Table 9-6-2 for the judgment of
defective resistance values.)
4. Main P.C. board is defective.
1. The temperature of the heat
exchanger is abnormally high.
2. The heat exchanger sensor
connector has short-circuit. (CN01)
3. The heat exchanger sensor is
defective. (Refer to Table 9-6-2
for the judgment of defective
resistance values.)
4. P.C. board is defective.
1. Poor contact of the motor
connector.
2. P.C. board is defective.
1. Is the fuse blown?
Voltage check
1. Between
TP1
and
N
(AC 220
∼
240V)
2. B and
−
of C03
(DC 310 ~ 340V)
3. Between
12V
and
GND
4. Between
5V
and
GND
Voltage check
1. Voltage of relay coil. (DC 12V)
Between pin 2 of RY01 and
GND
2. Between No. 1 and 2 of connect-
ing cable terminal block.
(AC 220
∼
240V)
1. All indicators light for 3 sec..
2. Indicators do not indicate normally
after approximate 3 sec..
1. Compressor does not operate.
2. OPERATION lamp blinks.
1. Compressor does not operate.
2. OPERATION lamp blinks.
1. Motor does not rotate. (The key
operation is accepted.)
2. The Motor rotates, but it vibrates
too much.
Shut off the power supply and
remove the P.C. board assembly
from the electronic parts base.
Remove the connecting cable from
the terminal block.
Remove the connector for the motor,
and turn the power on.
If the OPERATION lamp blinks
(0.5 sec. : ON, 0.5 sec. : OFF) when
the power turning on, the checking
points described as 1-4 of right
column are not necessary to
perform.
Make the operation status by
pushing once the [ ]
button, except the status of [FAN
ONLY], [ON TIMER].
Start the operation with the system
which the time of the restart delay
timer is shortened.
Make the operation status by
pressing once the [ ]
button.
1. The time of the restart delay timer
is shortened.
2. Cool operation
3. Air volume [AUTO]
4. Make the setting temperature lower
enough than room temperature.
5. Continuous operation.
The status of No. 5 is continued, and
make the following condition.
1. Heat operation
2. Make the setting temperature
higher enough than room
temperature.
Turn the power on after connecting
the motor connector. Start the
operation with the following
condition.
1. Operation [Cooling]
2. Airflow [High fan]
3. Continuous operation
Check Point (Symptom)
Causes
}
FILE NO. SVM-10031
1.