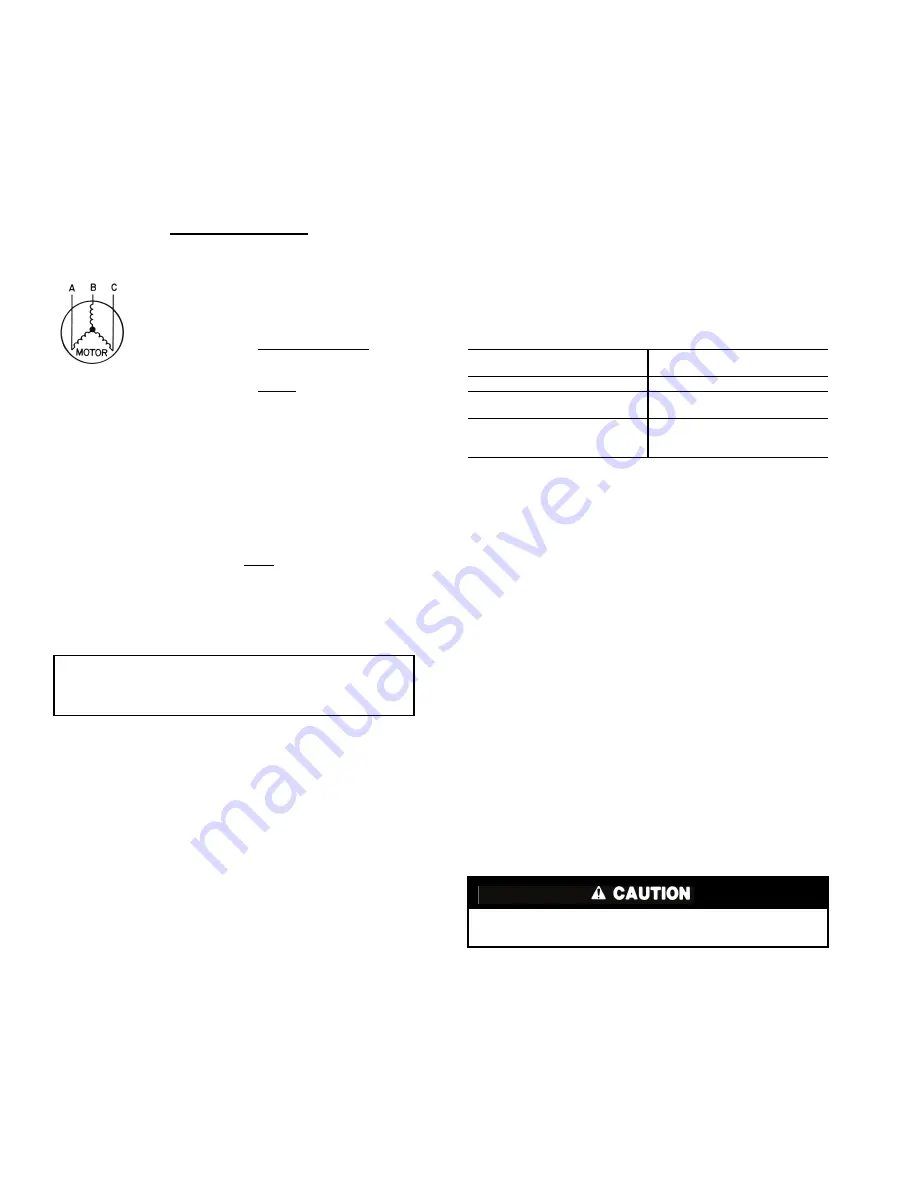
18
Step 4 — Complete Electrical Connections
GENERAL — Verify that nameplate electrical requirements
match available power supply. Voltage at condenser must be
within the minimum and maximum shown in Table 3 and
phases must be balanced within 2%. Contact local power com-
pany for line voltage corrections. Never operate a motor where
a phase imbalance in supply voltage is greater than 2%. Use
the following formula to determine the percentage of voltage
imbalance:
Example: Supply voltage is 240-3-60.
AB = 243 volts
BC = 236 volts
AC = 238 volts
Determine maximum deviation from average voltage:
(AB) 243 – 239 = 4 volts
(BC) 239 – 236 = 3 volts
(AC) 239 – 238 = 1 volt
Maximum deviation is then 4 volts. To determine the percent-
age of voltage imbalance:
This amount of phase imbalance is satisfactory since it is
below the maximum allowable of 2%.
Condenser operation on improper line voltage or excessive
phase imbalance may be considered abuse and any resulting
damage may not be covered by Carrier warranty.
All wiring must be in accordance with NEC (National Elec-
trical Code, U.S.A.) regulations or local codes.
CONNECTIONS — Refer to Table 3 and Fig. 21.
Install a field-supplied disconnect capable of being locked
at OFF position.
POWER
WIRING
—
Install field-supplied branch circuit
fused disconnect(s) of a type that can be locked OFF or OPEN.
Disconnect(s) must be within sight from and readily accessible
from unit in compliance with NEC Article 440-14 (U.S.A.) or
local code.
GENERAL WIRING NOTES
1.
The control
circuit field supply disconnect should
never be open except when unit is being serviced or is
to be down for a prolonged period.
2. Power entry is at one end only.
3. Terminals for field power supply are suitable for cop-
per, copper-clad aluminum, or aluminum conductors.
Insulation must be rated 60 C minimum.
4. Field power supply wires based on minimum 26 C
ambient temperature air are 8 AWG (American Wire
Gage) for Models 09DK034, 044 (208/230-3-60,
230-3-50), 12 AWG for all other models.
5. Connect field power wires to factory-supplied 8 AWG
wire from contactor with factory-supplied nut.
6. Route field wiring through factory-supplied wire ties
and base rail holes. See Fig. 3-5.
7. Control circuit power is as follows:
NOTE: Use 14 AWG (American Wire Gage) copper conductors only
for control circuit wiring.
Step 5 — Add Accessories as Needed —
Accessories include fan cycling head-pressure control, winter
start control, fan cycling, and electrical interlock. Refer to
installation instructions furnished with each accessory.
START-UP
System Evacuation and Dehydration —
Refer to
GTAC II, Module 4, “Dehydration for Proper Evacuation and
Dehydration techniques.”
Charging Procedure —
BEFORE CHARGING THE
SYSTEM, INSTALL OR REPLACE THE FILTER-
DRIER(S) CONNECTED TO THE LIQUID LINE WITHIN
THE IN-DOOR UNIT(S) TO PREVENT CONTAMINA-
TION WITHIN THE SYSTEM. Charge to a clear sight glass.
Refer to GTAC II, Module 5 “Charging, Recovery, Recycling,
and Reclamation” and Carrier Refrigerant Service Techniques
manual for proper charging techniques. Add 10 lbs (4.5 kg) of
R-22 over clear sight glass to flood subcooler sections of the
condenser coils. See Table 4 for charging data.
Check Operation of Condenser Fan Motor
Controls and Rotation of Fans —
R
otation should
be counterclockwise as viewed from top of unit.
% Voltage
Imbalance = 100 x
max voltage deviation
from average voltage
Average voltage
Average Voltage =
243 + 236 + 238
3
=
717
3
= 239 volts
% Voltage Imbalance = 100 x
4
239
= 1.7%
IMPORTANT: If supply voltage phase imbalance is
more than 2%, contact your local electric utility
company immediately.
CONTROL CIRCUIT
V-Hz
POWER
SUPPLY V-Hz
220-60
380-60
230-50
230-50
400-50
115-60
208/230-60
460-60
575-60
Before starting unit, be sure wire fan guards are secured in
place over each fan.
Summary of Contents for 09DK Series
Page 23: ......