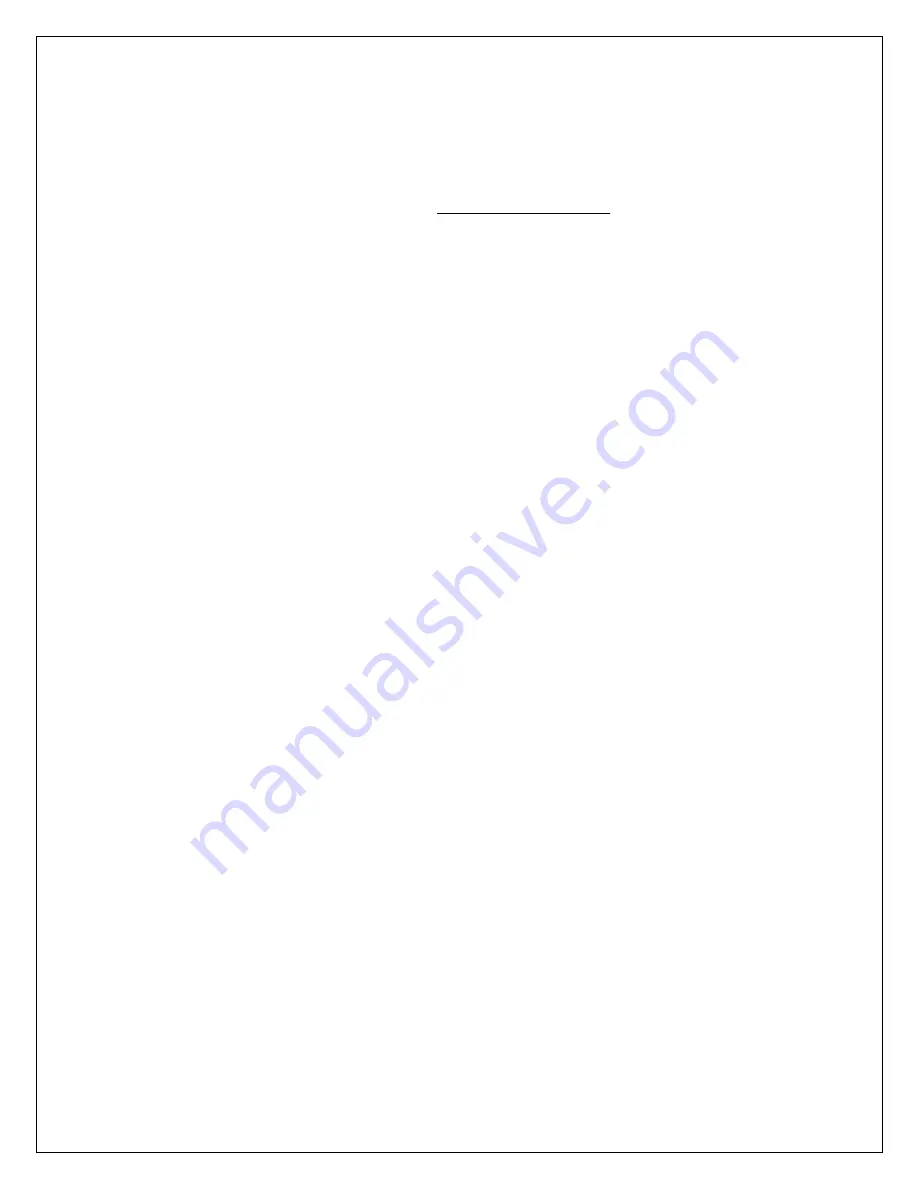
11
Step 4: Build Ratio
1. Determine the
Build Ratio
of the winder. If multiple sizes are used, calculate with
the smallest core diameter and largest maximum diameter. Note that the PI240-
000 module is only designed to handle build ratios of approximately 3 or less. For
larger
Build Ratios
, contact Carotron, Inc. for assistance.
lDiameter
MinimumRol
lDiameter
MaximumRol
BuildRatio
=
Step 5: Teach Process Variable (Feedback)
1. The order in which the two extreme feedback levels (minimum and maximum) are
taught determines the logic of the control loop.
2. For Dancer systems, position the dancer at the extreme position that should force
the follower drive to increase in speed. For Loadcell systems, apply either no load
or full load (by hanging weights in the material path) to the loadcell that should
cause the follower drive to increase in speed.
3. Apply power to the PI240-000 Module. Within one minute, connect the Teach
input (terminal 12) to circuit common (terminal 11).
4. For Dancer systems, position the dancer at the other extreme position that should
force the follower drive to decrease in speed. For Loadcell systems, apply the
other extreme signal (either no load of full load) that should cause the follower
drive to decrease in speed.
5. Disconnect the Teach input (terminal 12) from circuit common (terminal 11).
Step 6: Select Bipolar Integral
1. Wait at least one minute after applying power to the module and place a jumper
from the Teach input (terminal 12) to circuit common (terminal 11).
Step 7: Speed Match
1. Ensure the enable contact between terminals 10 & 11 is open.
2. Enable the lead and takeup drives. Run the lead drive up to maximum desired
speed. The line speed reference signal that is connected to the Summing Input
on terminal 5 should be scaled to a maximum of 9 volts.
3. Using a handheld tachometer, measure the surface speed of the lead drive. This
is the
MaximumSurfaceSpeed
. Adjust the (empty core) speed of the takeup drive
until its surface speed is slightly faster (10%) than this value. The takeup drive
speed would typically be adjusted by using its Max Speed or Analog Input Gain
adjustment.
Step 8: PI Trim
1. Manually force the dancer or loadcell feedback sensor so it is in the “slow down”
state.
2. Enable the PI loop by closing the contact across terminals 10 & 11. Verify that the
module output decreases and causes the takeup drive to decrease in speed.
3. Likewise, manually force the dancer or loadcell feedback sensor so it is in the
“speed up” state, and verify that the takeup drive increases in speed.
4. If the module exhibits opposite logic (i.e. increases speed when it should decrease
speed), then repeat Step 5 teaching the feedback levels in the opposite order.
5. With the dancer or loadcell in the “slow down” state, wait until the PI module
output on terminal 7 saturates (stops decreasing). Adjust the PI Trim
Summary of Contents for PI240-000
Page 1: ...Proportional Integral Loop Module Instruction Manual PI240 000 ...
Page 5: ...5 3 2 Signal Connections Figure 2 General Connections ...
Page 17: ...17 4 Prints 6 6 6 6 ...
Page 18: ...18 ...
Page 19: ...19 ...
Page 20: ...20 ...