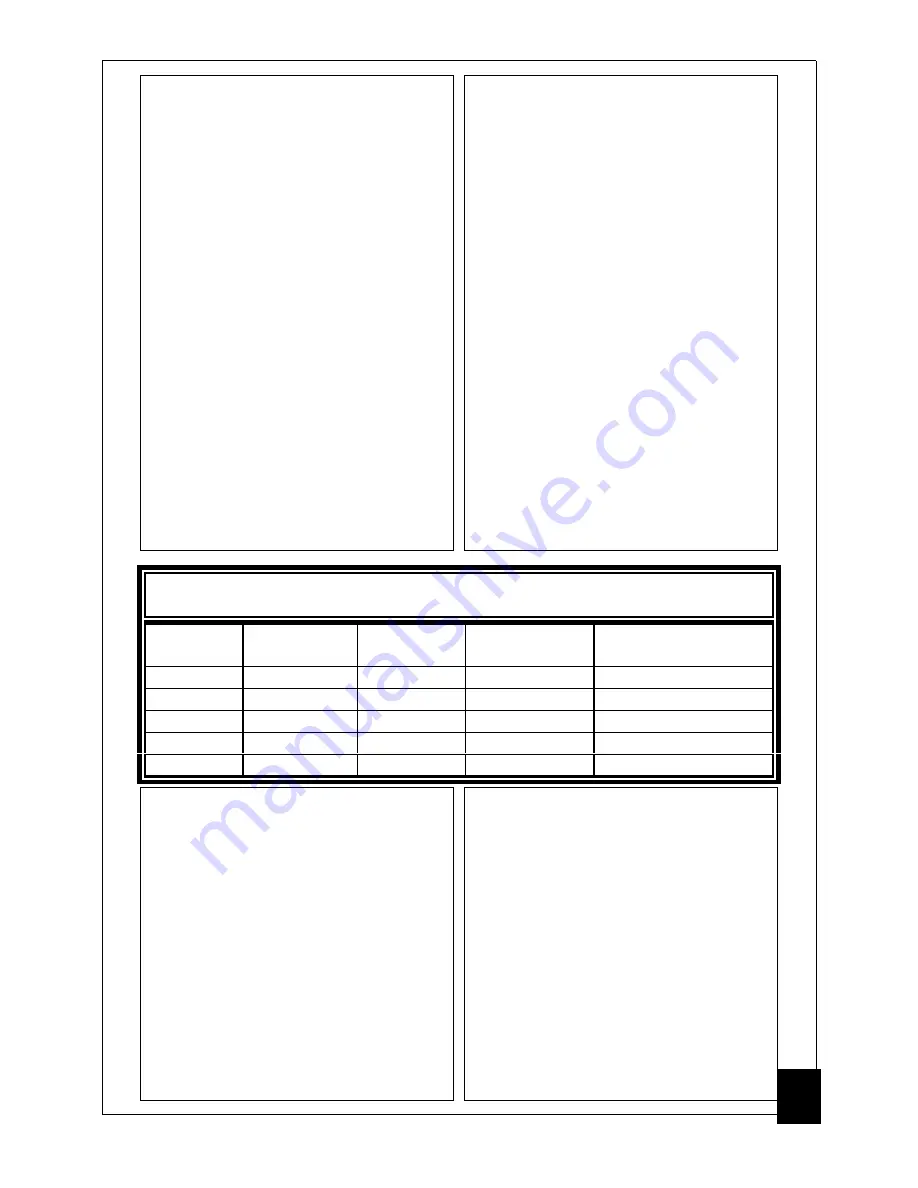
TABLE 2: ARMATURE CONTACTOR AND DYNAMIC BRAKE RISISTOR
RATING
MOTOR
HP
ARM
VOLTS
ARM
AMPS
CONTACTOR
RATING
D.B. RESISTOR
RATING
5
240
20
40 Amp
10 Ohms, 300 W
7.5
240
29
40 Amp
5 Ohms, 600 W
10
240
38
40 Amp
4.4 Ohms, 750 W
15
240
55
75 Amp
3 Ohms, 1000 W
20
240
72
75 Amp
2.2 Ohms, 1500 W
never
be switched by relay, contactor,
switch or any other manual or electro-
mechanical device.
The Carotron P22194-1 motor
control is
designed to sense field current
and will indicate an open circuit in the
field windings or wiring by initiating a
FIELD LOSS fault condition.
Armature
The armature leads are usually the
highest current wires associated with
the drive and warrant special attention
to sizing based on current rating as well
as length of run. Extra care should be
used where terminations and splices are
made. Refer to TABLE 2 for typical
armature voltage, current, contactor,
and dynamic braking resistor ratings.
Drawing C11977 shows the
armature, contactor and brake resistor
connections to the
A+
and
A-
terminals.
Note
: When present, the Series field
winding
(S1 and S2) is placed in series
with the armature leads. The series field
winding polarity must be kept at the
same polarity as the shunt field
winding, i.e. F1 and S1 the same, F2 or
F4 and S2 the same.
Motor Thermostat
Most motors include "J" or "P"
leads that connect to an internal
normally closed thermostat. Connecting
the thermostat in series with the O-Stop
circuit at Terminal 12 as shown in
Drawing C11977 will allow a motor
over-temperature condition to shut
down the control as in an O-Stop
condition.
4.3 Interlock Connections
Relay contact connections are
provided to interface with the Fault,
Current Limit, and Motor interlock
circuits. Refer to Drawing C11977 for
these connections.
TB1 Terminals 1-3
Motor Interlock
The Motor Interlock relay is
energized when power is applied and
releases when armature voltage is
greater than 6% of rated (about 15
VDC). The Motor LED also turns ON
at this point.
TB1 Terminals 4-6 Fault Interlock
The Fault Interlock relay is energized
when power is applied and releases
when a fault condition occurs (Field
Loss, Low Line/Phase Loss, or Over
Current Trip).
TB1 Terminals 7-9 Current Mode
Interlock
The Current Mode Interlock relay is
energized when power is applied and
during speed control operation. When
6
Summary of Contents for P22194-1
Page 1: ...P22194 1 DC DRIVE Instruction Manual ...
Page 22: ...Drawings 9 21 ...
Page 23: ...22 ...
Page 24: ...23 ...
Page 25: ...24 ...
Page 26: ...25 ...