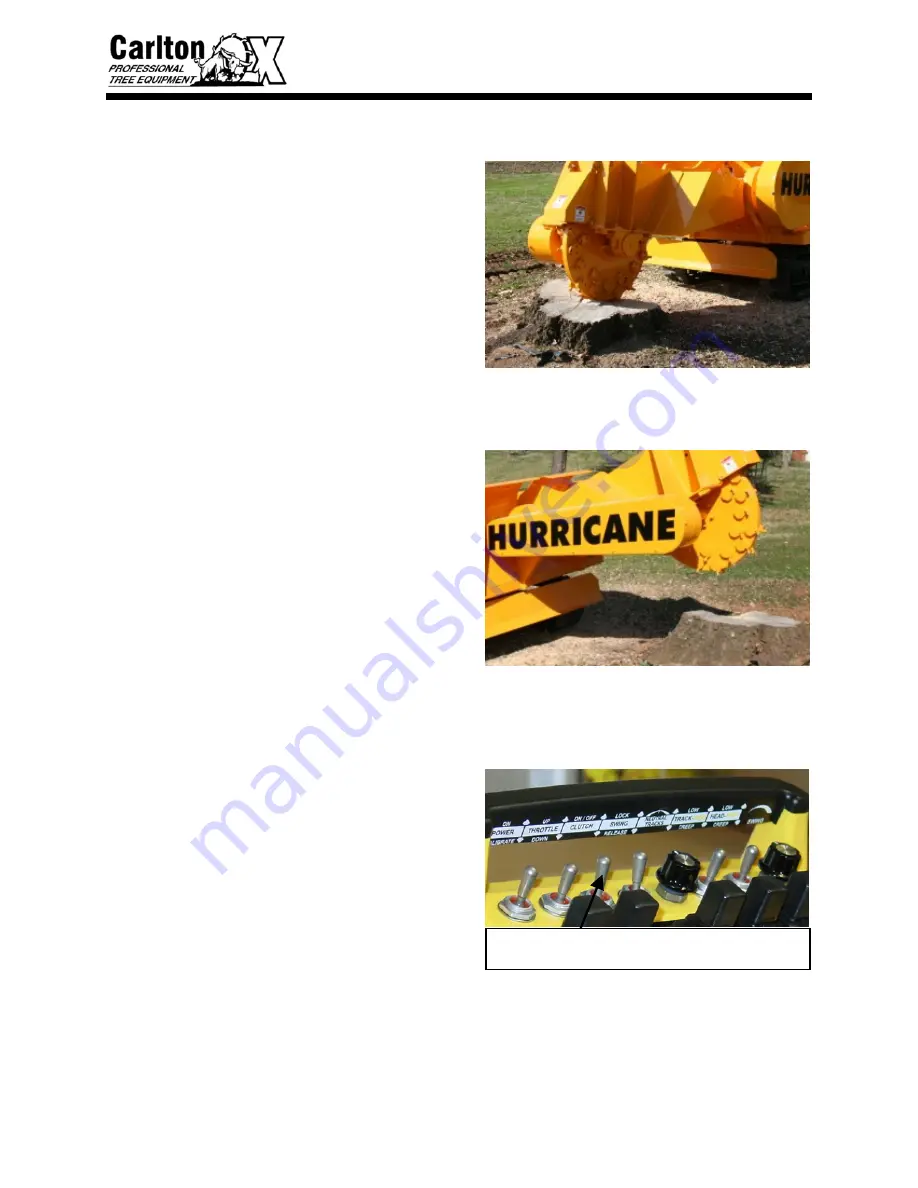
Hurricane Track MACHINE OPERATION
25
•
Continue cutting the stump by adjusting
the cutting head progressively lower
until the stump is cut well below ground
level.
•
Raise and swing cutter wheel clear of
stump and position machine closer to
stump for next series of passes. Lower
and continue cutting.
•
Continue in this manner until stump has
been removed.
•
Larger stumps may require repositioning
machine to work at best advantages.
•
IF RED LOW BATTERY LIGHT
LIGHTS UP ON THE TRANSMITTER,
THERE IS APPROXIMATELY 20
HOURS OF BATTERY POWER LEFT.
•
Raise cutter wheel clear of stump and
return to center position. On the radio
control transmitter, put the Swing Brake
switch in the LOCK position before
moving or turning off the machine.
•
Reduce engine speed to idle. DO NOT
TURN OFF MOTOR. Engine must be
allowed to cool slowly at idle for 3-5
minutes to avoid damage.
•
With engine at idle (below 1100 RPM),
disengage clutch by pushing the switch
down on the radio control transmitter.
The clutch will disengage immediately
and the Clutch Engage light will go off
on the clutch control panel. The cutter
wheel will take several minutes to come
to a complete stop.
•
Move the machine away from the work
area after the cutter wheel has come to a
complete stop.
•
Turn off machine using key on machine
control panel. CLUTCH MUST BE
DISENGAGED BEFORE TURNING
MACHINE OFF. Allow cutter wheel to
come to a complete stop before
inspecting the work area.
DISENGAGE CLUTCH WITH ENGINE AT IDLE. CLUTCH
MUST BE DISENGAGED BEFORE TURNING ENGINE OFF
Summary of Contents for Hurricane RS
Page 2: ......
Page 4: ......
Page 5: ...HURRICANE TRACK SAFETY ALERT...
Page 6: ......
Page 7: ...HURRICANE TRACK SAFETY ALERT...
Page 8: ......
Page 9: ...HURRICANE TRACK SAFETY ALERT...
Page 10: ......
Page 11: ...HURRICANE TRACK SAFETY ALERT...
Page 12: ......
Page 14: ......
Page 16: ......
Page 18: ......
Page 20: ......
Page 77: ...Hurricane Track MACHINE WIRING 54...
Page 82: ...TRACK MAINTENANCE 1 RUBBER TRACK ON HURRICANE TRX...
Page 83: ...TRACK MAINTENANCE 2 3 2 1...
Page 84: ...TRACK MAINTENANCE 3...
Page 85: ...TRACK MAINTENANCE 4...
Page 86: ...TRACK MAINTENANCE 5...
Page 87: ...TRACK MAINTENANCE 6...
Page 88: ...TRACK PARTS LIST 7...
Page 89: ...TRACK PARTS LIST 8...
Page 90: ...TRACK PARTS LIST 9...
Page 91: ...TRACK PARTS LIST 10...
Page 92: ...TRACK PARTS LIST 11...
Page 93: ...TRACK PARTS LIST 12...
Page 94: ...TRACK PARTS LIST 13...
Page 95: ...TRACK PARTS LIST 14...
Page 96: ...TRACK PARTS LIST 15...
Page 97: ...TRACK PARTS LIST 16...
Page 108: ...I M BULLETIN HPTO8TD 100 HYDRAULIC POWER TAKE OFF 9 11 2007 10 of 10...
Page 109: ...I M BULLETIN HPTO8TD 100 HYDRAULIC POWER TAKE OFF 9 11 2007 11 of 11...
Page 120: ...I M BULLETIN HPTO8TD 100 HYDRAULIC POWER TAKE OFF Page 10 of 10...
Page 121: ...I M BULLETIN HPTO8TD 100 HYDRAULIC POWER TAKE OFF Page 11 of 11...
Page 135: ...I M BULLETIN CMCCU 004 BASIC CONTROLLER Page 13 of 13...
Page 136: ...I M BULLETIN CMCCU 004 BASIC CONTROLLER Page 14 of 14...
Page 138: ......
Page 139: ......
Page 140: ......
Page 141: ......
Page 142: ......
Page 143: ......
Page 144: ......
Page 145: ......
Page 146: ......
Page 147: ......
Page 148: ......
Page 149: ......
Page 150: ......
Page 151: ......
Page 152: ......
Page 153: ......