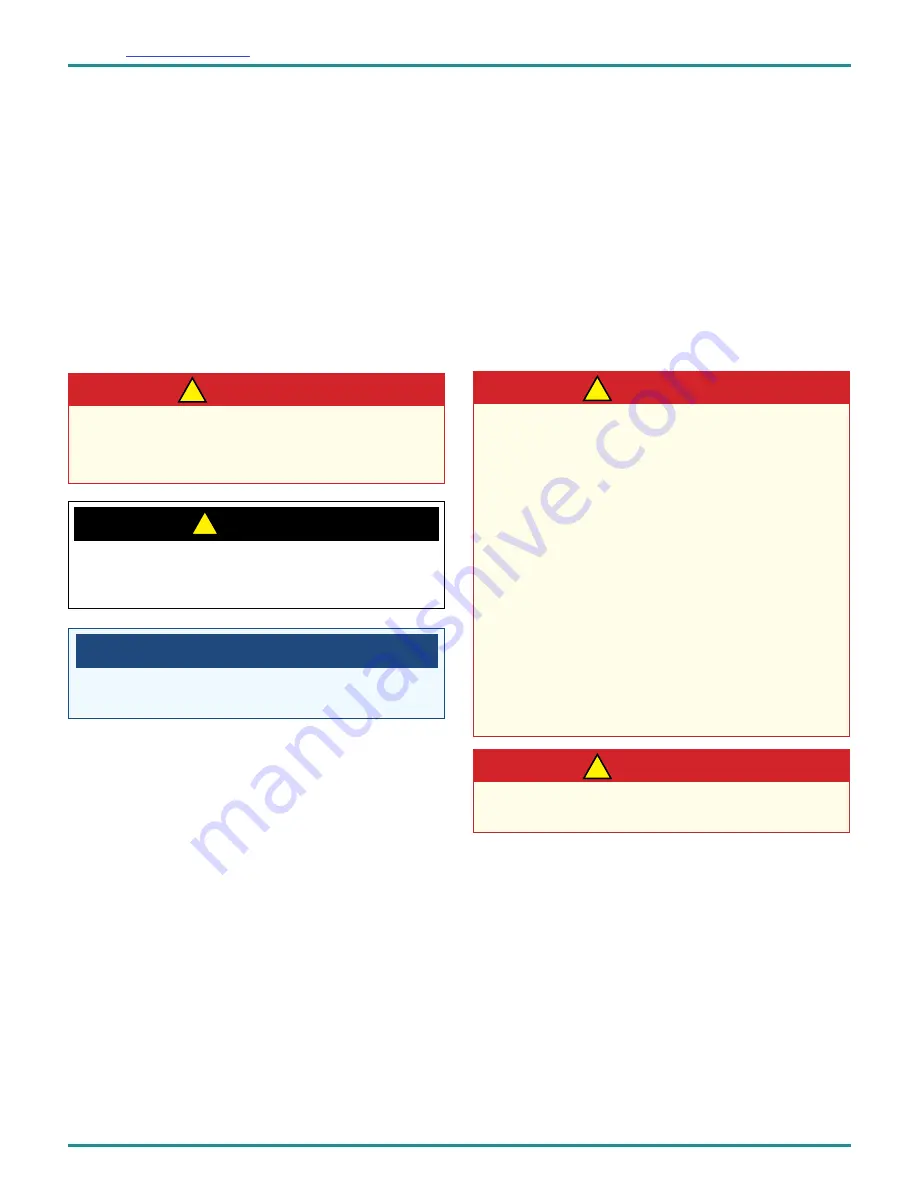
CAUTION
!
WA R N I N G
!
NOTE
SAFETY PRECAUTIONS
Before operating, maintaining or servicing any electrostatic
coating system, read and understand all of the technical
and safety literature for your products. This manual
contains information that is important for you to know and
understand. This information relates to
USER SAFETY
and
PREVENTING EQUIPMENT PROBLEMS
. To help you
recognize this information, we use the following symbols.
Please pay particular attention to these sections.
A WARNING! states information to alert you to
a situation that might cause serious injury if
instructions are not followed.
A CAUTION! states information that tells how to
prevent damage to equipment or how to avoid a
situation that might cause minor injury.
A NOTE is information relevant to the procedure
in progress.
While this manual lists standard specifications and service
procedures, some minor deviations may be found between
this literature and your equipment. Differences in local codes
and plant requirements, material delivery requirements, etc.,
make such variations inevitable. Compare this manual with
your system installation drawings and asscoiated equipment
manuals to reconcile such differences.
WA R N I N G
!
WA R N I N G
!
The user
MUST
read and be familiar with the
Safety Section in this manual and the safety literature
therein identified.
This equipment is intended to be used by
trained personnel
ONLY
.
This manual
MUST
be read and thoroughly
understood by
ALL
personnel who operate, clean
or maintain this equipment! Special care should
be taken to ensure that the
WARNINGS
and safety
requirements for operating and servicing the
equipment are followed. The user should be aware
of and adhere to
ALL
local building and fire codes
and ordinances as well as
NFPA-33 AND EN 50177
SAFETY STANDARDS, LATEST EDITION
, or
applicable country safety standards, prior to installing,
operating, and/or servicing this equipment.
The hazards shown on the following pages may
occur during the normal use of this equipment.
SAFETY
Repairs may only be performed by authorized personnel.
Careful study and continued use of this manual will provide a
better understanding of the equipment and process, resulting
in more efficient operation, longer trouble-free service and
faster, easier troubleshooting. If you do not have the manuals
and safety literature for your equipment, contact your local
Carlisle Fluid Technologies representative or Carlisle Fluid
Technologies technical support.
PA-19-04-R0 (02/2019)
3 / 29
www.carlisleft.com
SAFETY
EN